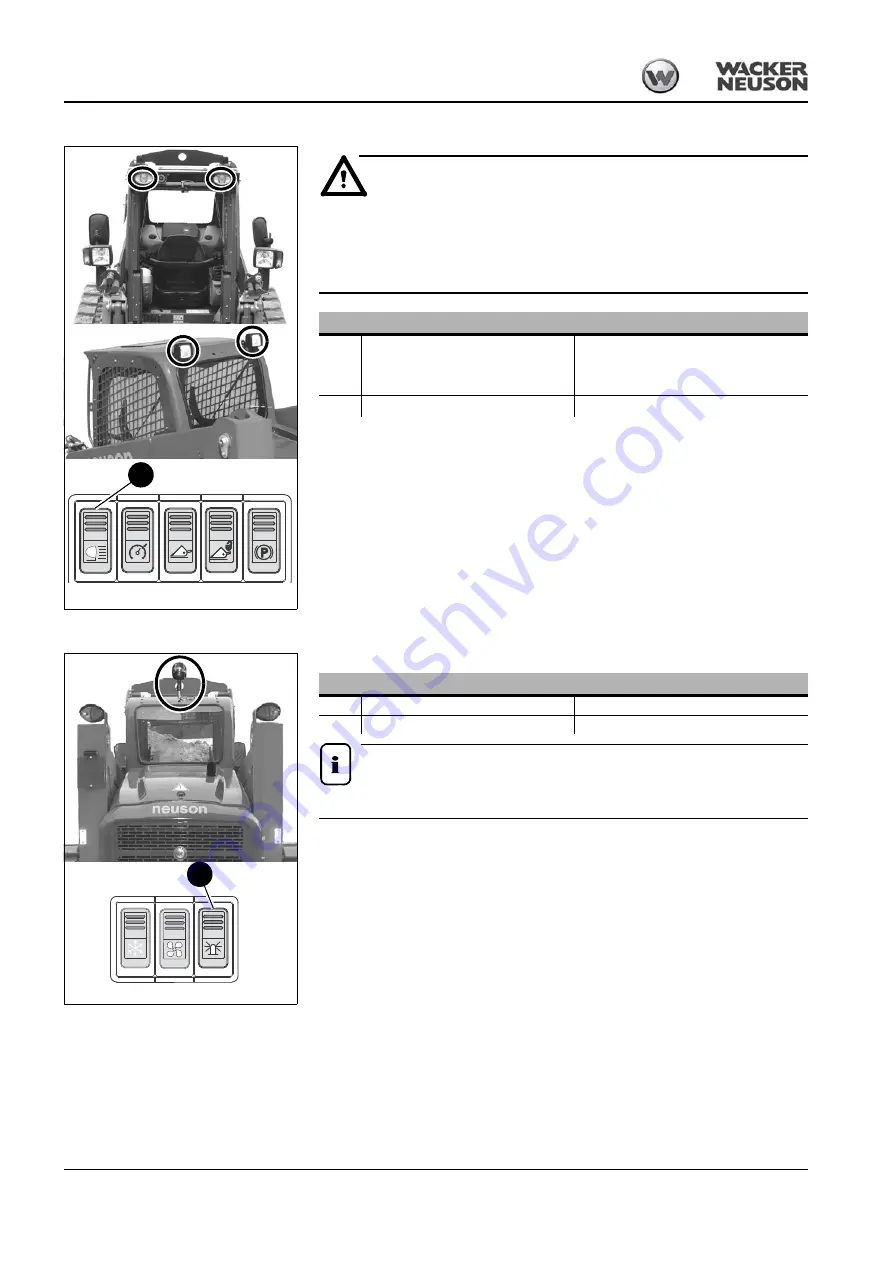
3-36
BA 901/1101 en – Edition 2.1 * 91101b330.fm
Operation
Working lights (option)
Danger!
The working lights can blind motorists on public roads.
☞
Do not switch on the working lights during machine travel on public roads.
When operating the machine, only switch the working lights on when no
one can be blinded by it!
Rotating beacon (option)
Notice!
Observe the legal regulations of your country for operating the rotating beacon.
Fig. 74: Working lights switch (option)
Rear working light
ON
☞
Press switch
to the
1st
position
☞
Press switch
to the
2nd
position
➥
Indicator light in switch
OFF
☞
Press switch
up
➥
Indicator light in switch
Fig. 75: Switch for rotating beacon (option)
Rotating beacon (option)
ON
☞
Press switch
down
➥
Indicator light in switch
OFF
☞
Press switch
down
➥
Indicator light in switch
Summary of Contents for 901S
Page 10: ...I 8 BA 901 1101 en Edition 2 1 Ba91101en2_1SIX fm Index...
Page 34: ...1 24 BA 901 1101 en Edition 2 1 91101b110 fm Introduction...
Page 46: ...2 12 BA 901 1101 en Edition 2 1 91101b210 fm Safety instructions...
Page 50: ...3 4 BA 901 1101 en Edition 2 1 91101b320 fm Operation 3 3 Instrument panel overview...
Page 122: ...3 76 BA 901 1101 en Edition 2 1 91101b340 fm Operation...
Page 166: ...5 42 BA 901 1101 en Edition 2 1 91101b560 fm Maintenance Maintenance plan model 1101...