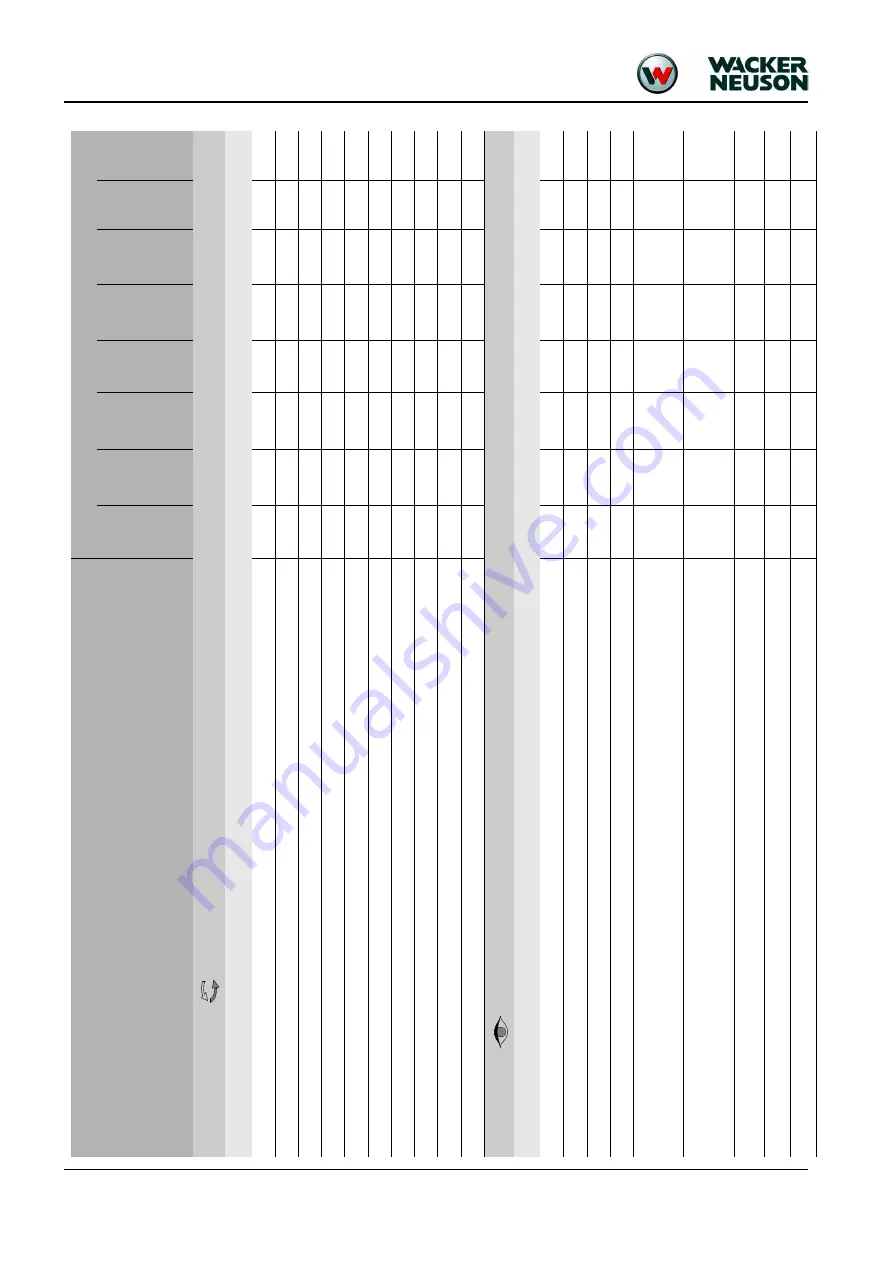
3-8
SHB 803 en – Edition 2.4 * 803s311.fm
Maintenance
3.3
M
ain
tenan
ce plan (
overview)
Work description
For servicing and maintenance on the attachment, p
lease refer to the ope
ration and maintenance manual of
the attachment manufacturer.
Maint
enan
ce plan/o
perat
ing
ho
urs (
o/h
)
Maintenance
(once a day)
Every 50 o/h
Every 250 o/h
Every 500 o/h
Every 1000 o/h
once a year
Every 2000 o/h
Customer
Authorized
service center
Fluid and filter changes (
):
Perform the following oil and filter changes
(check oil leve
ls after test run):
•
Engine oil
1
●●
●
•
Engine oil filter
2
●●
●
•
Fuel filter
3
●●
●
•
W
ater separator
●●
•
C
oolant
●●
•
H
ydr
aulic
oi
l fil
ter ins
ert
4
●●
●
•
H
ydr
aulic
oi
l
5
●●
●
•
D
rain condensation water from the hyd
raul
ic oil reservoir (fro
m se
rial no
. A
H
02272)
●●
•
Air filter ele
m
ent (up to
seria
l no. AI00875)
●●
•
Air filter ele
m
ent according to di
rt indicator (from serial no. AI00876)
6
●●
Inspection work (
):
Check the following materi
al. Refill if necessary:
•
Engine oil
●●
•
Engine coolant
●●
•
Fuel
●●
•
H
ydr
aulic
oi
l
●●
Check the function of the
pedals (up to serial n
o. A
I00975)
•
C
lean, lubricate or repair the pedals
●●
Check the function of the
pedals, they must flip back automatically (from serial no. AI00976)
•
C
lean, lubricate or repair the
pedals, check the torsion springs
●●
Clean water ducts
7
●●
Check radiator for engine and hydraulic
oil for dirt. Clean if necessary
●●
Check cooling systems and hoses for
leaks an
d pressure (visual check)
●●
Summary of Contents for 803 Dualpower
Page 1: ...Service Manual Track excavator Machine model 803 Edition 2 4 Order no 1000164843 Language en ...
Page 8: ...I 6 SHB 803 en Edition 2 4 803s20IVZ fm Table of contents ...
Page 9: ...Operation ...
Page 23: ...Technical data ...
Page 38: ...2 16 SHB 803 en Edition 2 4 803s210 fm Technical data ...
Page 39: ...Maintenance ...
Page 96: ...3 58 SHB 803 en Edition 2 4 803s314 fm Maintenance ...
Page 97: ...Engine ...
Page 133: ...Hydraulic system ...
Page 155: ...SHB 803 en Edition 2 4 803s511 fm 5 23 Hydraulic system Hydraulic system Hydraulics diagram ...
Page 157: ...SHB 803 en Edition 2 4 803s511 fm 5 25 Hydraulic system 5 11 Hydraulics diagram ...
Page 160: ...5 28 SHB 803 en Edition 2 4 803s511 fm Hydraulic system ...
Page 161: ...Electrical system ...
Page 168: ...6 8 SHB 803 en Edition 2 4 803s611 fm Wiring harnesses ...
Page 181: ...SHB 803 en Edition 2 4 803s612 fm 6 21 Electrical system Wiring diagrams Electrical system ...
Page 185: ...Options ...
Page 194: ...7 10 SHB 803 en Edition 2 4 803s710 fm Options ...