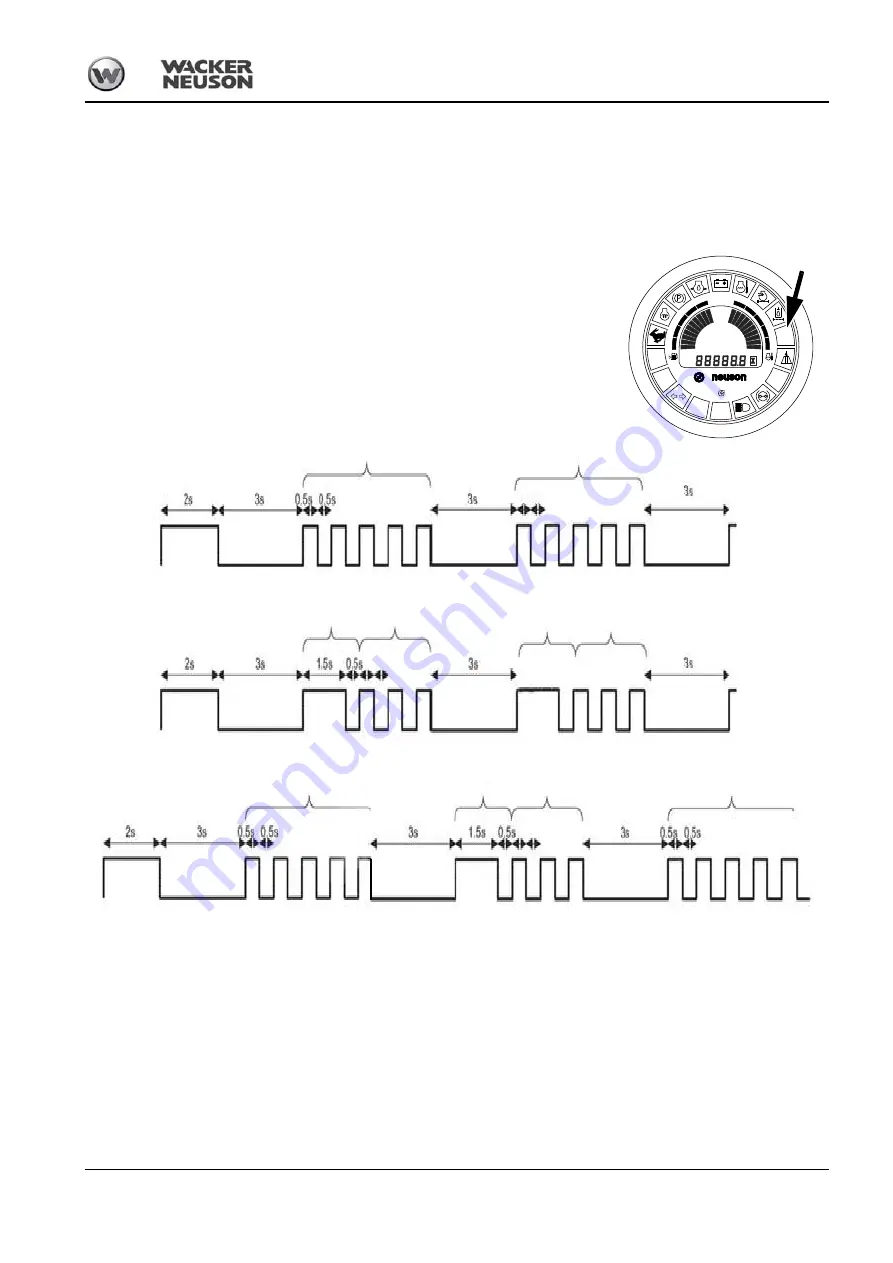
BA 50Z3/6003 en – Edition 4.3 * 5003b410.fm
4-5
Troubleshooting
4.2
Engine error codes
In the case of specific errors:
➥
Engine speed and output is reduced.
➥
The engine is switched off.
➥
The engine no longer starts.
Example C = ‘5’ and ‘1 – 3’
Example for flash codes:
mph
km/h
DP1
DP2
DP3
DP4
DP5
DP6
DP7
DP8
DP9
DP10
DP24
DP23
DP22
DP21
DP20
DP19
DP18
DP17
DP16
DP15
!
!
5x short
1x long
3x short
Ignition ON
Ignition ON
Example A = ‘5’
Example B = ‘1 – 3’
Ignition ON
1x long
3x short
5x short
5x short
5x short
1x long
3x short
Summary of Contents for 50Z3
Page 35: ...BA 50Z3 6003 en Edition 4 3 5003b110 fm 1 23 Introduction Overview of safety labels ...
Page 56: ...2 16 BA 50Z3 6003 en Edition 4 3 5003b210 fm Safety instructions ...
Page 178: ...3 122 BA 50Z3 6003 en Edition 4 3 5003b340 fm Operation ...
Page 190: ...4 12 BA 50Z3 6003 en Edition 4 3 5003b410 fm Troubleshooting ...
Page 254: ...5 64 BA 50Z3 6003 en Edition 4 3 5003b560 fm ...
Page 265: ...BA 50Z3 6003 en Edition 4 3 5003b610 fm 6 11 Specifications 6 16 Dimensions model 50Z3 ...
Page 267: ...BA 50Z3 6003 en Edition 4 3 5003b610 fm 6 13 Specifications 6 17 Dimensions model 50Z3 VDS ...