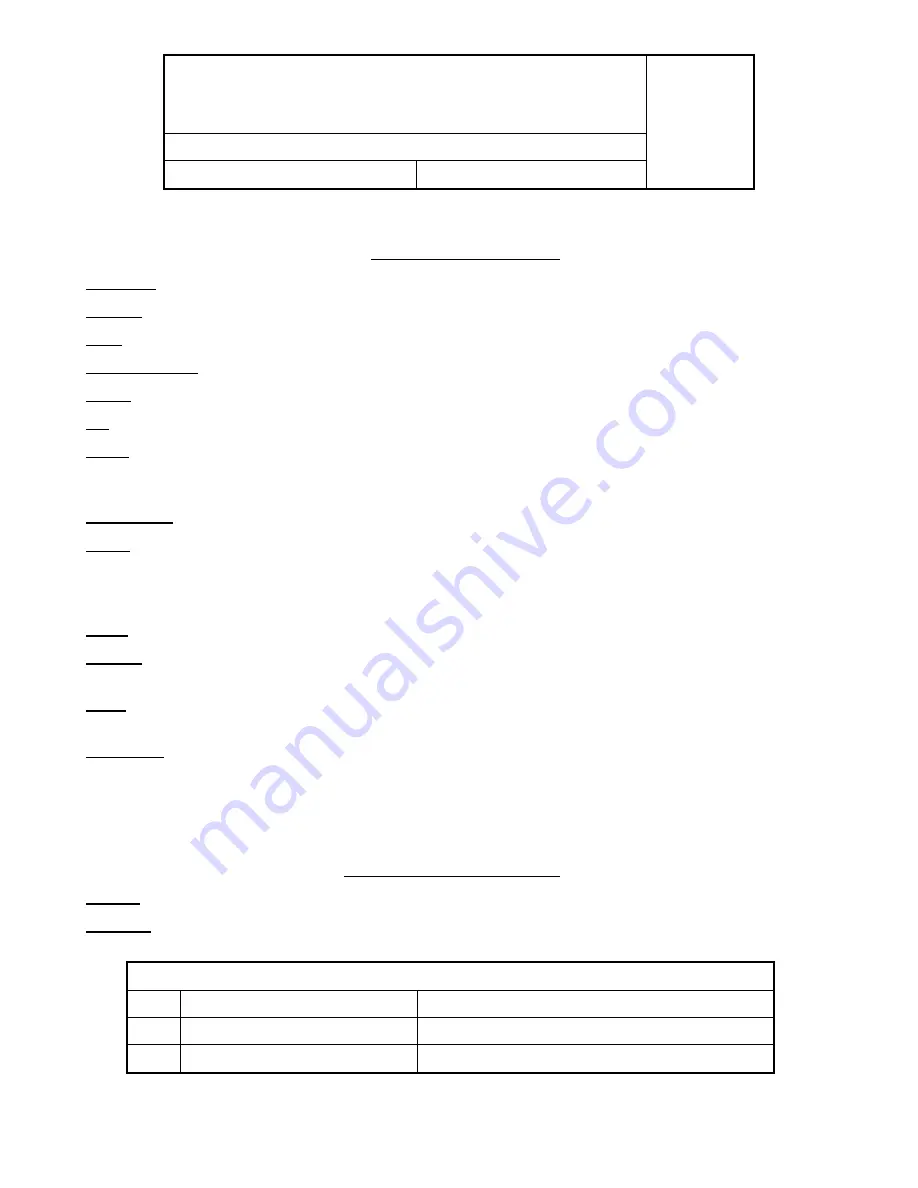
Vyaire Medical, Inc.
Cover Sheet
Title: Vela Ventilator Software Download Instructions
Part no.: 33373-001
Ver.: A
Do not print this page.
PRINTING INSTRUCTIONS
Literature:
33373-001
Artwork:
33373-001 Version A
Title:
Lit., Vela Ventilator Service Manual
Document Size: 8.5 X 11 and 11 X 17 schematics and drawings (accordion folded to 8.5 X 11)
Paper:
20# or similar printer / copier weight paper
Ink:
1/1 Black/Black
Sided:
Print two sided unless specifically instructed otherwise. Print 11 X 17 pages single
sided. Insert blank pages as needed to maintain proper page count and structure.
Start all chapters on right-facing, (odd-numbered) pages.
File formats:
Adobe Acrobat (*.pdf). See the literature’s electronic file.
Cover:
4/0 Color copy preferre
d. Size to “Document Size.” Print file from CD; “Cover. pdf”
or close file name. Paperweight equal to or heavier than “Paper” specifications,
preferably 80# C1S. Cover to be placed directly in the front cover, clear plastic
overlay.
Back:
NA
Binding:
Three
ring binders at least 0.75” or greater, white, clear window (View Binder),
inside pockets are not required but acceptable.
Proof:
A representative from marketing communications or purchasing will approve
proof for quality.
Packaging:
Manuals may be individually shrink-wrapped using clear material. The L# found
on the cover must not be hidden or obscured beyond recognition.
Contents/quantities are to be marked on all cartons. Cartons are not to exceed 40
pounds. All paperwork must include the purchase order number, part number(s),
and the description of the contents. All digital files, images, and material are the
property of Vyaire Medical.
PRINTER RECOMMENDATION
Printer:
Purchasing to choose printer.
Approval:
Incoming inspection to approve.
Versions
Ver.
Chg. Order
Description
A
QP-RES-CON-YL-18-001
Initial release.
Summary of Contents for VELA
Page 2: ...33373 001 Version A VELA Ventilator Service Manual ...
Page 19: ...2 6 Chapter 2 Theory of Operation 33373 001 Version A This page intentionally left blank ...
Page 87: ...B 2 Appendix B Reordering Instructions 33373 001 Version A This page intentionally left blank ...
Page 88: ...Appendix C Schematics Diagrams C 1 33373 001 Version A Appendix C Schematics Diagrams ...
Page 89: ...Appendix C Schematics Diagrams C 2 33373 001 Version A ...
Page 90: ...Appendix C Schematics Diagrams C 3 33373 001 Version A ...
Page 91: ...Appendix C Schematics Diagrams C 4 33373 001 Version A ...
Page 92: ...Appendix C Schematics Diagrams C 5 33373 001 Version A ...
Page 93: ...Appendix C Schematics Diagrams C 6 33373 001 Version A ...
Page 94: ...Appendix C Schematics Diagrams C 7 33373 001 Version A ...
Page 95: ...Appendix C Schematics Diagrams C 8 33373 001 Version A ...
Page 96: ...Appendix C Schematics Diagrams C 9 33373 001 Version A ...
Page 97: ...Appendix C Schematics Diagrams C 10 33373 001 Version A ...
Page 98: ...Appendix C Schematics Diagrams C 11 33373 001 Version A ...
Page 99: ...Appendix C Schematics Diagrams C 12 33373 001 Version A ...
Page 100: ...Appendix C Schematics Diagrams C 13 33373 001 Version A ...
Page 101: ...Appendix C Schematics Diagrams C 14 33373 001 Version A ...
Page 102: ...Appendix C Schematics Diagrams C 15 33373 001 Version A ...
Page 103: ...Appendix C Schematics Diagrams C 16 33373 001 Version A ...
Page 104: ...Appendix C Schematics Diagrams C 17 33373 001 Version A ...
Page 105: ...Appendix C Schematics Diagrams C 18 33373 001 Version A ...
Page 106: ...Appendix C Schematics Diagrams C 19 33373 001 Version A ...
Page 107: ...Appendix C Schematics Diagrams C 20 33373 001 Version A ...
Page 108: ...Appendix C Schematics Diagrams C 21 33373 001 Version A ...
Page 109: ...Appendix C Schematics Diagrams C 22 33373 001 Version A ...