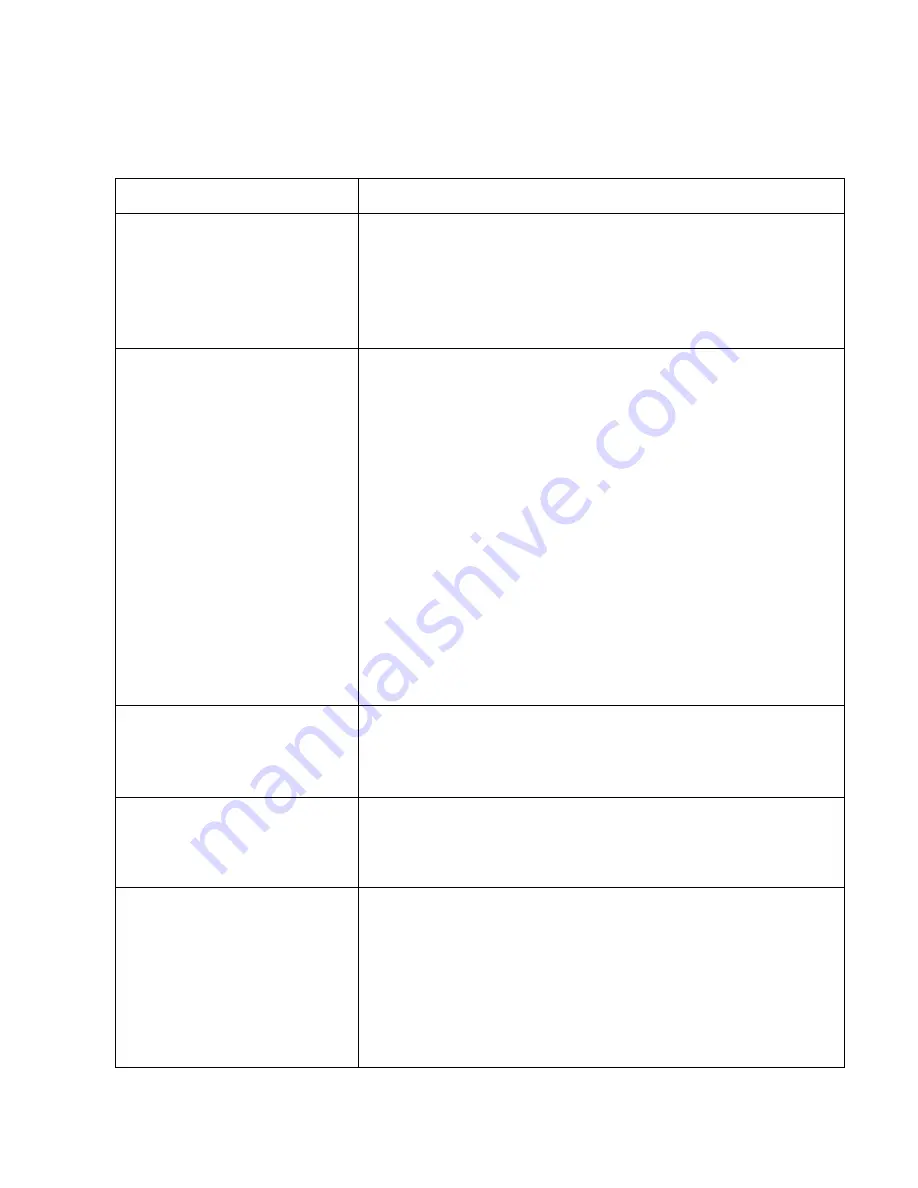
Part number 20073, Rev 0
10
QUICK TROUBLESHOOTING GUIDE
Check these items before calling for service
PROBLEM:
POSSIBLE CAUSE / SOULTIONS:
Unit does not run
Electrical circuit is not 110-120V 60Hz.
The power cord is not plugged in.
No power at electrical outlet. Check to make sure
breaker is not tripped or fuse is not blown. Additionally,
make sure unit is not plugged into a Ground Fault Circuit
Interrupter (GFCI) type of outlet.
Unit does not maintain at the
proper temperature
Check the room temperature. We recommend the
refrigerator or freezer should be placed in the air
conditioned room between 65°F to 85°F. If the room
temp is too warm, the refrigerator or freezer may not be
able to maintain the interior temp at proper range.
Door is not closed properly.
Amount of stored product is overloaded.
Product replacements are pushed against rear wall or
interrupted the proper refrigerator air circulation. For
the proper air circulation, place the products evenly on
each shelf. Do not push against the refrigerator’s rear or
side walls.
Evaporator is blocked by frost or ice. Remove the
products, unplug the refrigerator or freezer power, and
allow the unit to defrost. If the problem still exists, call
for service.
Appliance runs too long
Prolong door openings.
Control set too cold.
Room temperature is high which will make the unit work
harder to keep cool.
Temperature of external wall
surface is warm
The exterior walls can be as much as 30 degrees warmer
than room temperature due to the embedded
condenser coils. This is normal when the unit is
operating.
Compressor noises
Check the unit level. Also ensure none of the pipes in
the compressor area are touching each other or against
the side.
Compressor may be overheated. Please check the room
temp and ensure the range is within 65°F to 85°F.
A buzzing noise may indicate improper voltage to the
compressor. Check supply voltage.
If the problem still exists, call for service.