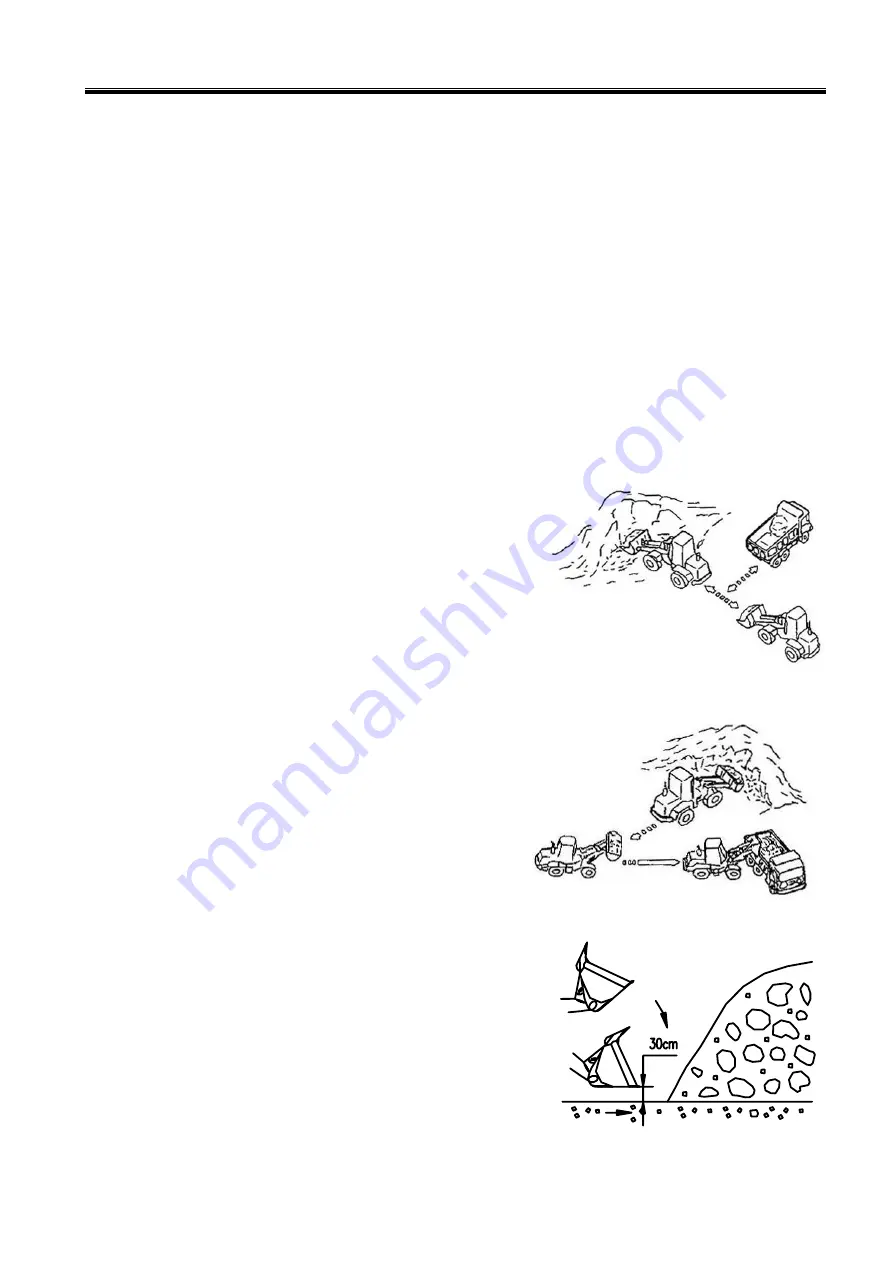
Operation & Maintenance Manual
──
LG956L Wheel Loader
84
z
Check the quantity of the brake oil by opening the oil bowl cover of the brake booster pump.
z
Drain the water in the air tank from the water outlet valve.
z
Clean the outside surface of machine and the inside of the bucket.
3.5 Operations
3.5.1 Prepare to Work
Clean the working area, and fill-up any hollow spaces. Clear away the sharp stones and roadblocks
that may break the wheels and operation.
3.5.2 Modes of Work
(1)
Loading Operation
z
Work together with a truck which can help improve working efficiency especially for long
distance transportation.
z
When working together, the loader digs the material and
the truck transports and unloads the material:
There are generally two loading and unloading ways:
z
Cross Load:
The loader faces the material, then it moves backward
after digging a full load and lets the auto-unload truck
move into the position between material and the loader. This method costs the minimum time and
can reduce the cycle time most effectively.
z
“V” Shape Load:
The auto-unload truck is fixed and forms almost a
60°angle with the backward direction of the loader.
After digging, the loader moves backward and turns
the designated degree and moves forward to the truck.
The smaller the loader work angle is, the more efficient
the work is.
(2)
Digging Operation
Digging Piled Soil or Blasted Rock
When digging piled soil or blasted rock, the loader should face
the material and do as follows:
z
If the bucket must be lowered while driving the machine
forward, stop the machine when the bucket is about 30cm
above from the ground, and then lower it slowly.