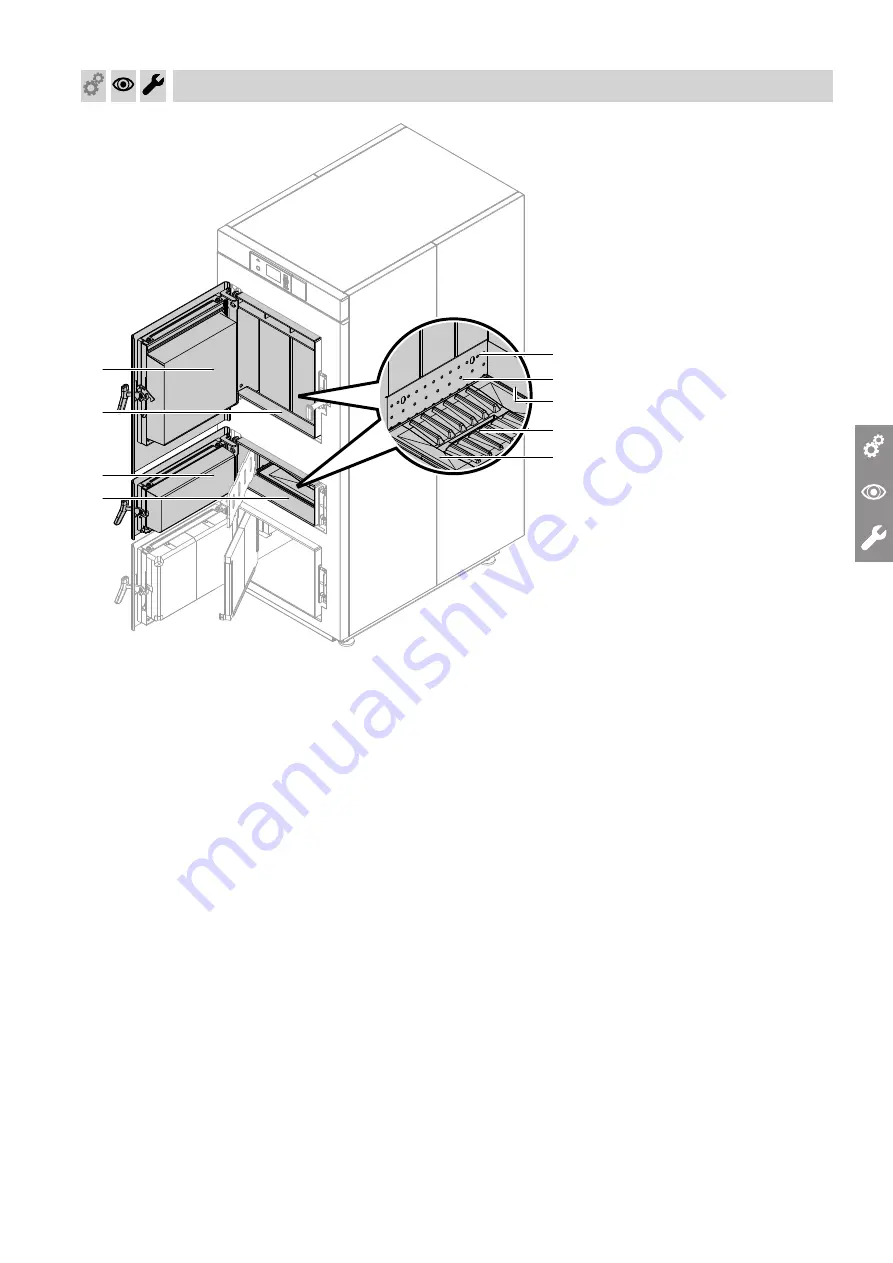
35
G
G
F
F
B
A
C
D
E
Fig. 22
1.
Use a scraper or spatula to remove dry and flaking
deposits (ash, carbon and tar) from the walls and
from the front and rear corners.
Note
■
Small surface cracks in moulded refractory con-
crete parts are normal. Such cracks have no
bearing on the function or service life of the
parts.
■
Shiny black deposits on the interior walls of the
hopper are normal. Deposits need not be
removed.
2.
Check primary air vents
A
in side elements
B
for
unrestricted flow. Clean with a vacuum cleaner if
required.
3.
Clean nozzle slot
C
in base element
D
.
4.
Use a scraper or spatula to remove dry and flaking
deposits (ash, carbon and tar) from the hopper
walls
E
, door frame
F
and the inside of hopper
door
G
.
Commissioning, inspection, maintenance
Hopper cleaning (if required)
5777 985 GB