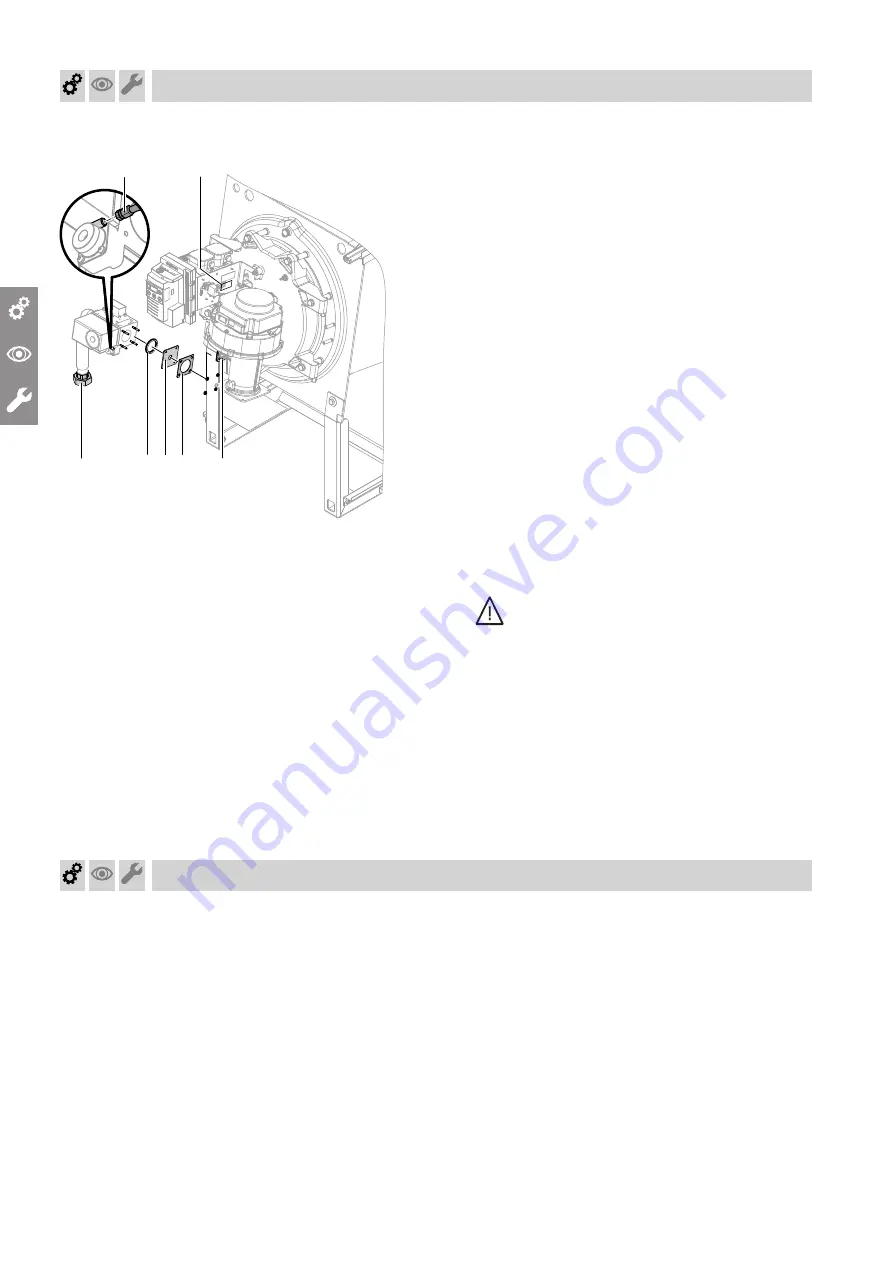
12
Conversion with 115 to 311 kW rated heating output
F
A
BCD
E
G
Fig. 3
0
1.
Close the gas shut-off valve.
0
2.
Switch off the system ON/OFF switch at the user
interface of the control unit.
0
3.
Switch OFF the mains isolator (outside the instal-
lation room) or isolate the mains power and
secure against unintentional reconnection.
0
4.
Undo fitting
A
.
0
5.
Disconnect control cable
G
from the gas train.
0
6.
Release the gas train from flange
E
.
0
7.
Remove restrictor
C
with rubber cork gasket
D
.
0
8.
Secure the gas train to flange
E
:
■
with O-ring
B
■
without restrictor
C
■
without rubber cork gasket
D
Torque for M 5 nuts: 1.5 Nm
0
9.
Secure fitting
A
with a new gasket.
10.
Plug control cable
G
into the gas train.
11.
Check control cables:
■
Connection and kink-free routing
■
Application and seating of retaining clips
12.
Where present for set gas type: Affix label "Set
to ..."
F
supplied over the existing label.
13.
Start the burner.
14.
Check for gas tightness.
Danger
Escaping gas leads to a risk of explosion.
Check gas routing components for leaks.
!
Please note
The use of leak detection spray can result in
faulty operation.
Leak detection spray must not come into
contact with electrical contacts.
Note
For control cable locations, see page 27.
Conversion to LPG P
Conversion to LPG P only with 186 to 311 kW rated
heating output
Commissioning, inspection, maintenance
Conversion to natural gas L
(cont.)
5831036