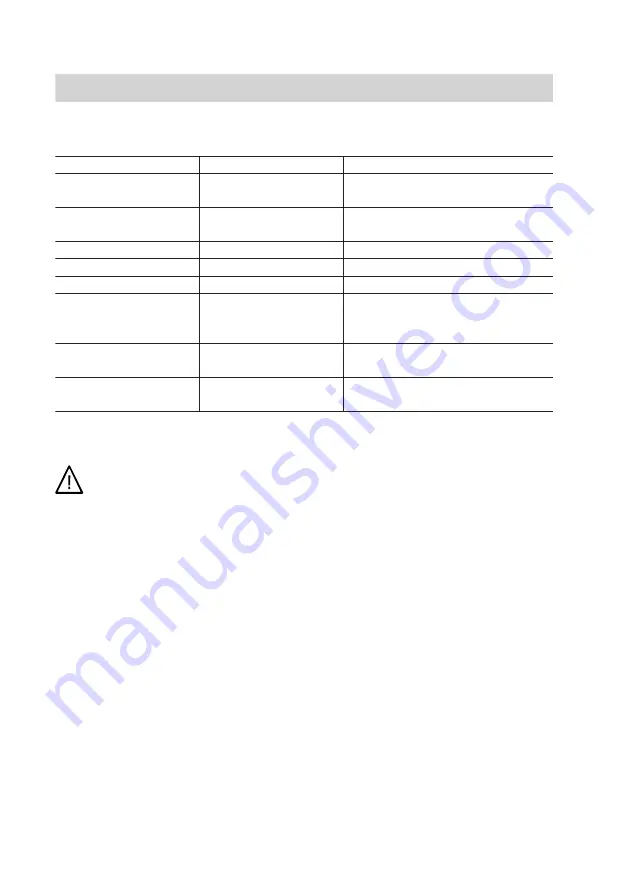
32
Required codes
Group
Code
Function
"Source type"
"3750:Solid fuel boil-
er"
Solid fuel boiler (only for display
purposes)
"System scheme"
"5700:4"
System scheme 4 as standard
function
"HC1"
"5710:On"
Heating circuit 1 installed
"HC2"
"5715:On"
Heating circuit 2 installed
"HC3"
"5721:On"
Heating circuit 3 installed
"Relay output QX2"
"5891:DHW ctrl elem
Q3"
DHW control element Q3, for lifting
the block on the auxiliary burner for
DHW heating
"Sensor input BX6"
"5935:Buffer sensor
B42"
Buffer cylinder sensor B42 fitted
"Function input EX2" "5982:Auxiliary
burner block"
Block on auxiliary burner during
changeover to solid fuel mode
Preparations for boiler installation
Danger
The product contains ceramic
fibres. If handled incorrectly, fibre
dust may be released.
Observe the stipulations of the
Technical Guidelines for the Han-
dling of Hazardous Materials
(TRGS) 521 [or local regula-
tions].
!
Please note
To prevent equipment damage,
install all pipework free of load
and torque stresses.
Preparing for installation
Preparing for installation
(cont.)
5618 294 GB
Summary of Contents for C3HA
Page 39: ...39 2 2x 1 Installation sequence Removing the front panel 5618 294 GB Installation ...
Page 42: ...42 1 2 Installation sequence Removing the transport brackets 5618 294 GB ...
Page 151: ...151 Checking and replacing resistors B C A Troubleshooting Repairs cont 5618 294 GB Service ...
Page 181: ...181 Parts lists Control unit assembly cont 5618 294 GB Service ...
Page 183: ...183 Parts lists Miscellaneous assembly cont 5618 294 GB Service ...
Page 191: ...191 5618 294 GB ...