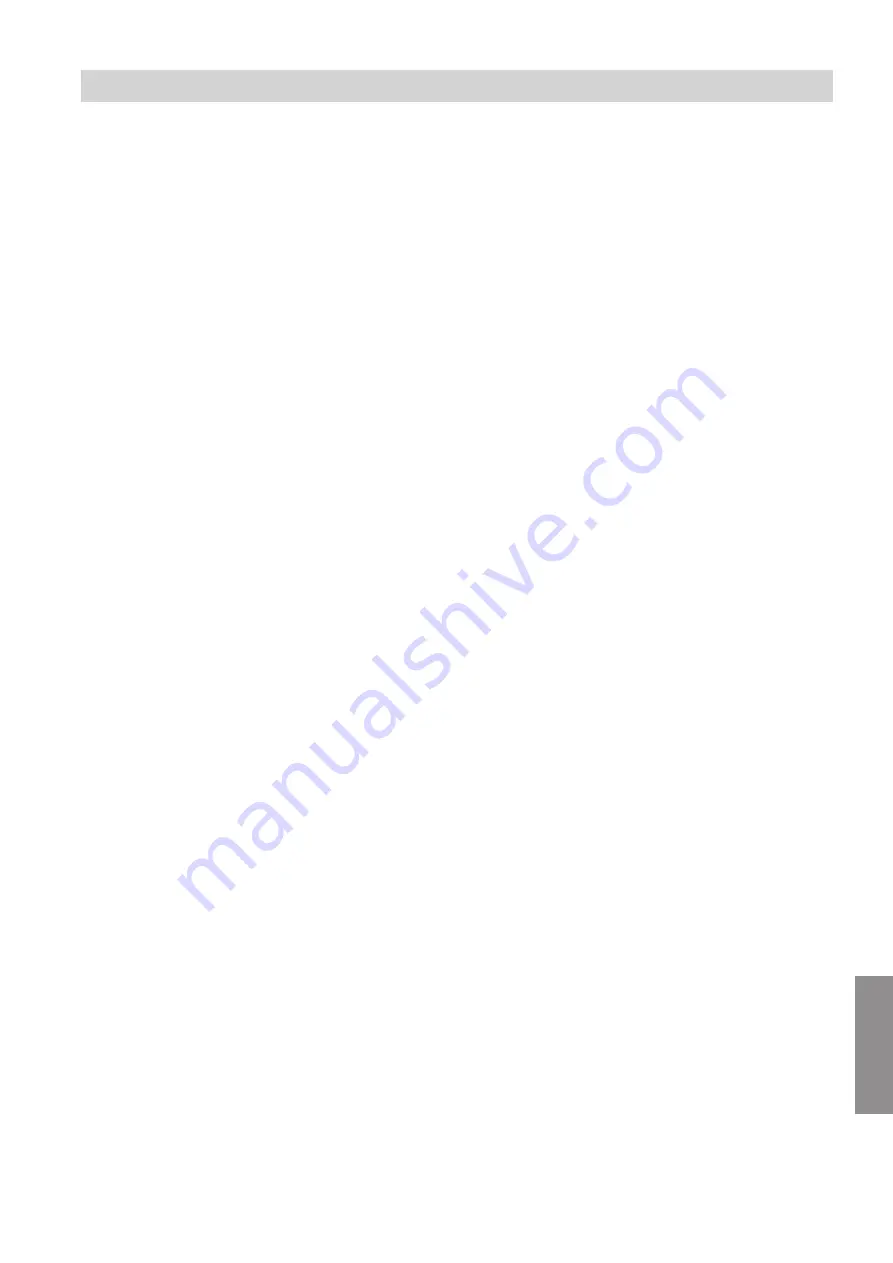
79
Once the appliance reaches the end of its service life,
or when replacing components, observe the statutory
regulations on dismantling, recovery and disposal.
Refrigerants may only be recovered and replaced by
professionals who are qualified and certified for this.
Used refrigerant must be recycled by correct and veri-
fied means.
The dismantling and disposal of components must be
carried out by type. The dismantling of refrigeration
systems may only be carried out by qualified professio-
nals. If permissible, components marked with the
"Green Dot" symbol can be disposed of via the dual
waste collection system [Germany]. Packaging
such as cardboard or foil should be disposed of via the
dual system or recycling trade.
The heat pump is filled with refrigerant R134a. The
refrigerant is a fluorocarbon and has a global warming
potential (GWP) of 1430.
Final decommissioning
Dismantling/disposal
5855865
Appendix
Summary of Contents for BW 352.B027
Page 83: ...83 5855865...