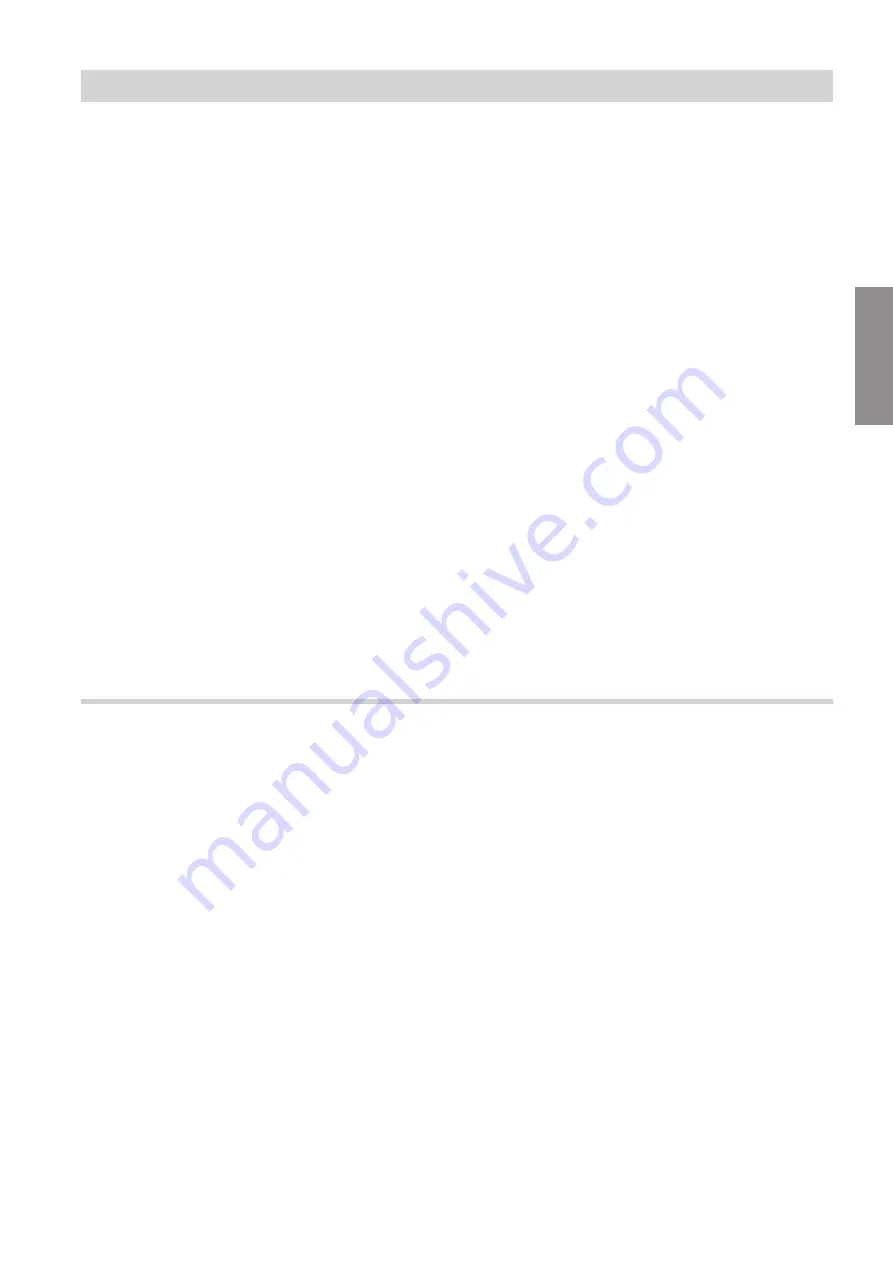
23
1.
Equip the primary circuit with an expansion vessel
and safety valve (to DIN 4757).
Note
■
The expansion vessel must be approved to
DIN 4807. The diaphragms of the expansion ves-
sel and safety valve must be suitable for the heat
transfer medium.
■
The blow-down and drain pipes should terminate
in a container. This container must be able to
hold the maximum possible expansion volume of
the heat transfer medium.
2.
Ensure adequate thermal and anti-vibration insula-
tion where pipes penetrate walls.
3.
Connect primary pipes to heat pump.
!
Please note
Mechanically loaded hydraulic connections
lead to leaks, vibration and appliance dam-
age.
Connect on-site lines so that they are free of
load and torque stress.
!
Please note
Leaking hydraulic connections lead to appli-
ance damage.
Ensure the diaphragm grommets at the hose
outlets are seated correctly. Seal hose out-
lets with sealing tape if necessary.
4.
Insulate pipes inside the building to prevent heat
and vapour diffusion.
5.
Charge the primary circuit with Viessmann heat
transfer medium and vent.
Note
Ensure frost protection down to
–
19 °C.
Viessmann heat transfer medium is a ready-mixed
ethylene glycol-based medium. It contains inhibi-
tors for corrosion protection. The heat transfer
medium can be used at temperatures down to
–
19 °C.
Note
Position of the hose diaphragm grommets: See
page 51.
Connecting the secondary circuit
1.
Equip the secondary circuit on site with an expan-
sion vessel and safety assembly (to DIN 4757).
Fit the safety assembly to the on-site line in the
heating water return.
2.
Connect the secondary lines to the heat pump
(
7
≥
28 mm).
!
Please note
Mechanically loaded hydraulic connections
lead to leaks, vibrations and appliance dam-
age.
Connect on-site lines so that they are free of
load and torque stress.
!
Please note
Leaking hydraulic connections lead to appli-
ance damage.
Ensure the diaphragm grommets at the hose
outlets are seated correctly. Seal hose out-
lets with sealing tape if necessary.
3.
Fill and vent secondary circuit.
4.
Thermally insulate pipes inside the building.
Note
■
Position of the hose diaphragm grommets: See
page 51.
■
In underfloor heating circuits, install a temperature
limiter on site to restrict the maximum temperature of
the underfloor heating system.
■
Ensure the minimum flow rate, e.g. by means of an
overflow valve: See "Specification" on page 123.
Installation sequence
Making the hydraulic connections
(cont.)
5516461
Installation
Summary of Contents for BW 301.B06
Page 69: ...69 Fig 49 Maintenance Opening the casing door 5516461 Maintenance...
Page 76: ...76 Maintenance Condensation and moisture in the heat pump cont 5516461 Maintenance...
Page 79: ...79 Parts lists type BWC 301 B Parts not shown type BWC 301 B cont 5516461 Components...
Page 88: ...88 Parts lists type BWC 301 B Hydraulics type BWC 301 B cont 5516461 Components...
Page 91: ...91 Parts lists type BW 301 B Parts not shown type BW 301 B cont 5516461 Components...
Page 100: ...100 Parts lists type BW 301 B Hydraulics type BW 301 B cont 5516461 Components...
Page 103: ...103 Parts lists type BWS 301 B Parts not shown type BWS 301 B cont 5516461 Components...