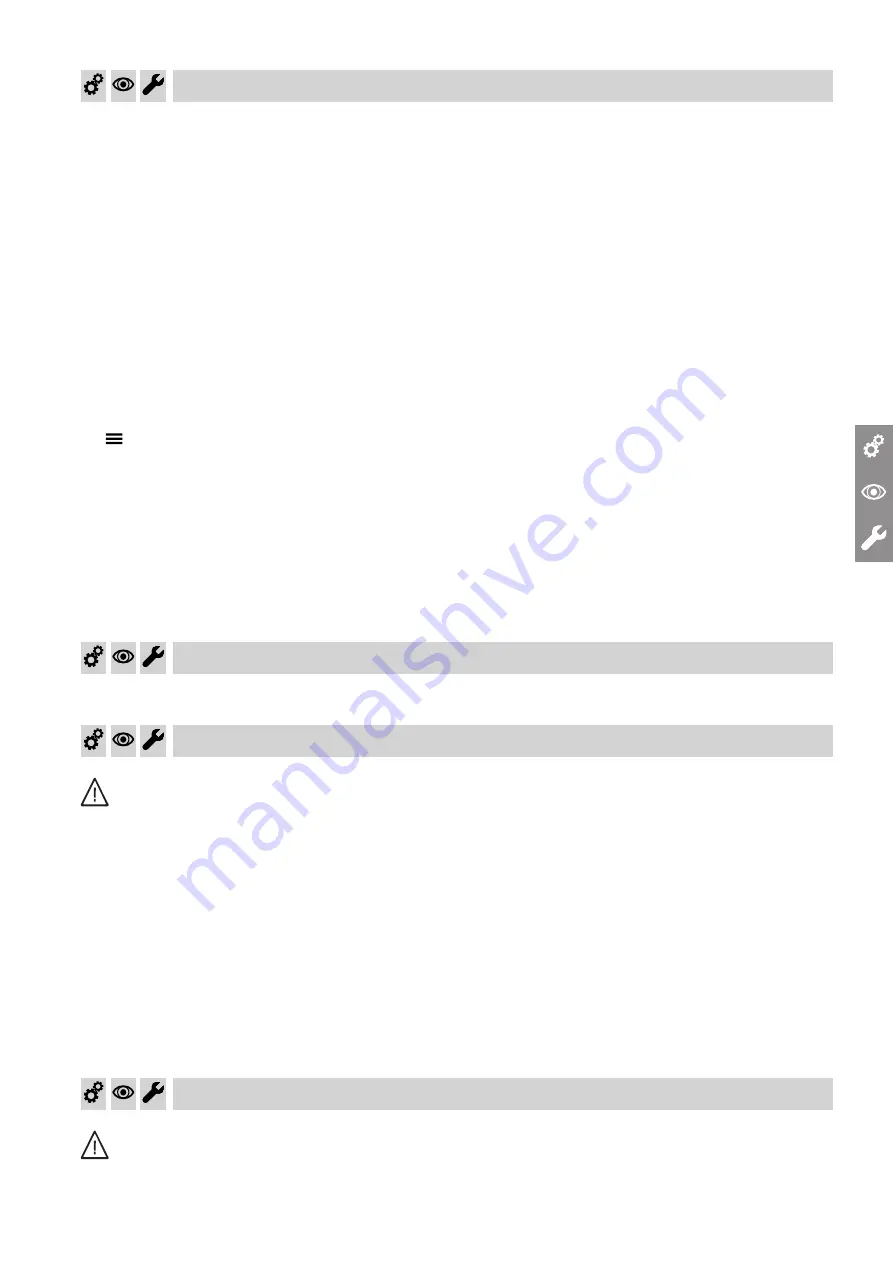
47
Note
The expansion vessel can lose some of its charge
pressure over time. When the boiler heats up, the
pressure rises to 2 or 3 bar (0.2 or 0.3 MPa). The
safety valve may also respond and discharge the
excess pressure.
Therefore check the expansion vessel pre-charge
pressure annually.
Check whether the installed expansion vessel is ade-
quate for the system water volume.
Carry out this test on a cold system.
1.
Drain the system until "0" is shown on the display.
Note
For pressure indicator on home screen, press
repeatedly until the pressure gauge symbol
appears.
2.
If the pre-charge pressure of the expansion vessel
is lower than the static system pressure: Top up
with nitrogen at the valve of the diaphragm expan-
sion vessel until the pre-charge pressure is 0.1 to
0.2 bar (10 to 20 kPa) higher than the static system
pressure.
3.
Top up with water until the charge pressure of the
cooled system is at least 1.0 bar (0.1 MPa), and is
0.1 to 0.2 bar (10 to 20 kPa) higher than the pre-
charge pressure of the expansion vessel.
Permiss. operating pressure: 3 bar (0.3 MPa)
Note
The expansion vessel is supplied from the factory
with a pre-charge pressure of 0.7 bar.
Do not allow the pre-charge pressure to fall below
this value (boiling noises). This also applies to sin-
gle floor heating systems or attic heating centres
(no static pressure).
Top up with water until the charge pressure is 0.1
to 0.2 bar above the pre-charge pressure.
Checking the safety valve function
Checking the electrical connections for firm seating
Danger
Contact with live components can lead to seri-
ous injury from electric current. Some compo-
nents on PCBs remain live even after the power
supply has been switched off.
■
Do not touch
the wiring chambers (control
unit and mains connections).
■
When working on the appliance, isolate the
system from the power supply, e.g. at a sepa-
rate MCB/fuse or a mains isolator. Check the
system is no longer live and safeguard against
reconnection.
■
Prior to working on the appliance, wait at
least 4 min until the voltage has completely
dropped out.
Checking all gas equipment for leaks at operating pressure
Danger
Escaping gas leads to a risk of explosion.
Check gas equipment (including inside the appli-
ance) for leaks.
Commissioning, inspection, maintenance
Checking the expansion vessel and system pressure
6179762