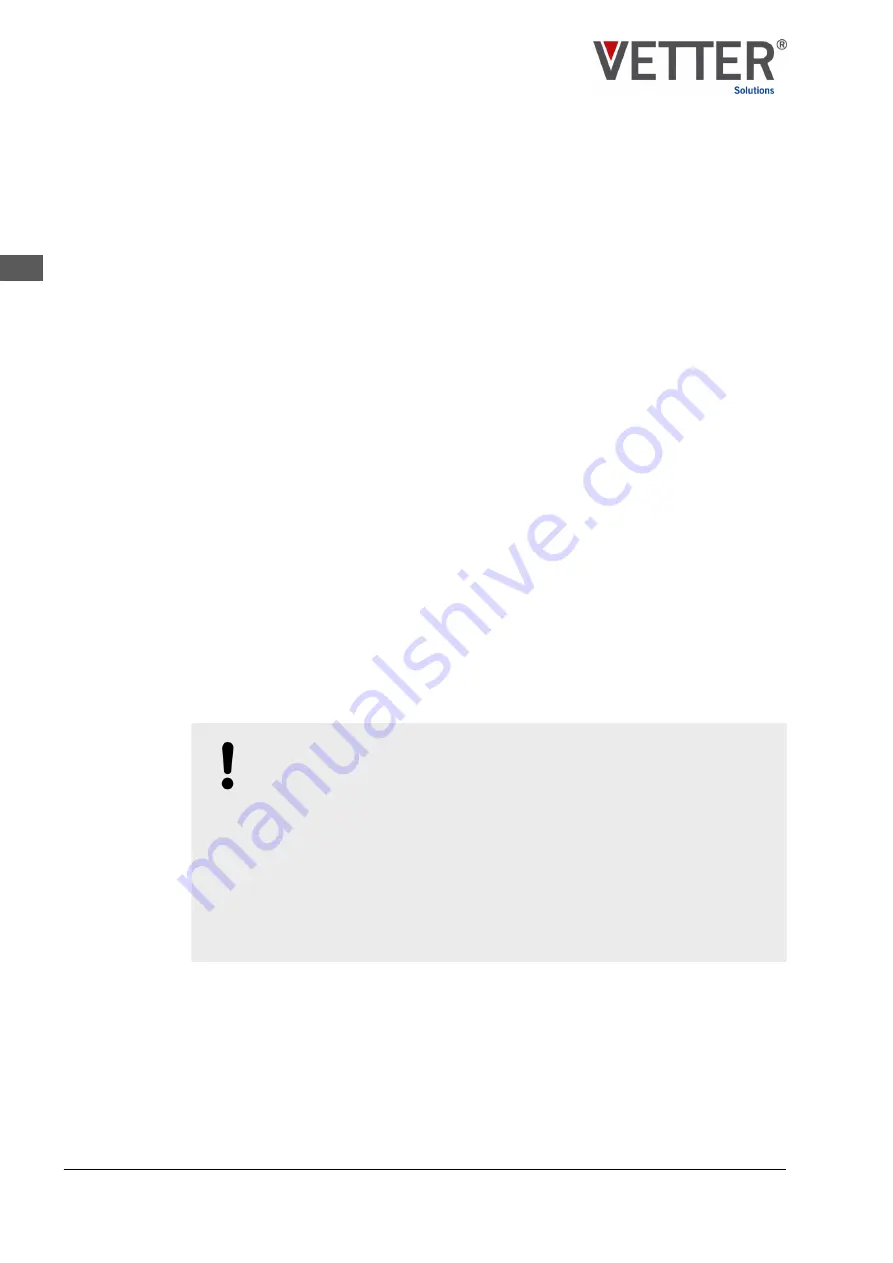
n
Check the equipotential bonding for functionality:
– The M6 screw connection must be in place and securely tightened.
– The cable connection to the industrial truck must be intact.
– Check the vertical resistance and ensure that the electrical resistance between the
industrial truck and fork arms is below 10
6
ohm.
n
Perform a daily visual inspection to determine if there is any corrosion on parts. The
gap-forming surfaces of the pressurised enclosure must not be corroded. Remove cor-
rosion immediately using non-abrasive measures (e.g. pickling) or replace corroded
parts.
n
Perform a daily visual inspection to identify any details and damage that would indicate
a failure of the pressurised enclosure.
– The gap-forming surfaces of the pressurised enclosure must not be damaged. The
repair of damaged gap-forming surfaces on covers or on the fork arm is not per-
mitted. Damaged parts are to be replaced immediately with original spare parts
from the manufacturer. Contact the manufacturer accordingly in this regard
Chapter 6.2.9 “Spare parts” on page 47
.
– The polycarbonate sheets, all stainless steel covers, including their screw connec-
tions, and seals must be seated securely and free of damage.
n
Safety markings must be complete and legible.
6.2.2
Checking the fork arms and suspension system
Personnel:
n
Service specialist
Protective equipment:
n
Industrial safety helmet
n
Protective clothing
n
Protective gloves
n
Safety shoes
NOTICE!
Risk of injury due to irregular checking!
The load capacity of the fork arms is impaired if the fork arms are dam-
aged. Use thereof can (e.g. in the event of material breakage due to
micro cracks) can cause serious accidents.
– Have the Smart
Fork
®
checked by a service specialist or the manufac-
turer at least once a year (more frequently for heavy usage or multiple-
shift operation).
– Carry out the test based on the currently applicable standard (e.g. ISO
5057, UVV test as per DGUV regulation 68). The service specialist will
specify the scope of the test and the test interval.
Maintenance
Maintenance activities > Checking the fork arms and suspension system
SmartFork
®
FrontCam ATEX for use in the Ex zone - BVS 20 ATEX E 108 X
40
EN