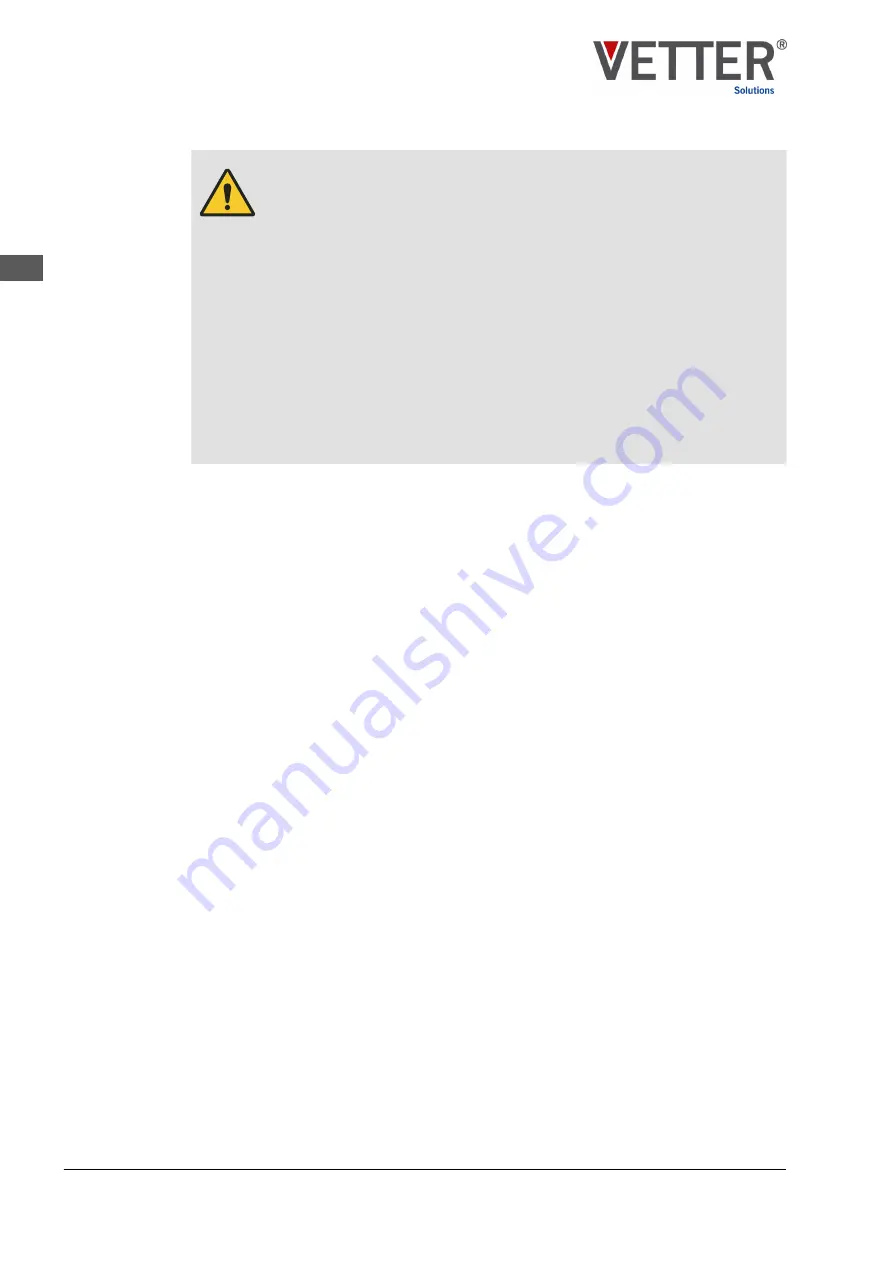
WARNING!
Incorrect use of the assistance systems!
Incorrect use of the Smart
Fork
®
Front
Cam
can lead to life-threatening
situations (e.g. harm to persons) and serious injuries.
– Never use the assistance system as the sole image source for
assessing danger zones. If in doubt, personally ensure that there are
no people or obstacles in the danger zone of the industrial truck.
– Never use the assistance system if the flameproof enclosure is dam-
aged.
– Never use the assistance system in insufficiently illuminated areas or if
visibility is reduced due to mist or dusts.
– Never use the assistance system at temperatures outside the tem-
perature range of -20 °C to +50 °C.
– Never use the assistance system if the polycarbonate lens is dirty,
greasy or covered in ice.
2.4
Operator obligations
The operator is the person who operates the Smart
Fork
®
on an industrial truck for indus-
trial or commercial purposes, or who delegates use to a third party and bears the legal
product responsibility during operation for the protection of personnel or third parties.
The Smart
Fork
®
is used in the commercial sector. The operator of the Smart
Fork
®
is
therefore subject to the legal requirements for occupational safety.
In particular, the following applies:
n
The operator must be aware of the applicable health and safety regulations and in a
risk assessment must determine any additional dangers that could arise from the par-
ticular working conditions at the operation site of the Smart
Fork
®
. These must be out-
lined in the form of operating instructions for operation of the Smart
Fork
®
.
n
The operator must ensure over the entire operating time that the operating instructions
created by him/her correspond to the current state of the rules and regulations, and
adjust them if necessary.
n
The operator must clearly regulate and specify the responsibilities for assembly, opera-
tion, troubleshooting, maintenance and cleaning.
n
The operator must ensure that all persons that come into contact with the Smart
Fork
®
have read and understood this manual. In addition, he/she must regularly train per-
sonnel and inform them of any dangers.
n
The operator must provide personnel with the required protective equipment and
instruct them that wearing the required protective equipment is mandatory.
In addition, the operator is responsible for ensuring that the Smart
Fork
®
is always in a
technically perfect condition. The following therefore applies:
n
The operator of the overall system (industrial truck) must prevent excessive current
consumption (fault current) by means of suitable technical devices.
n
The operator must ensure that the maintenance intervals described in this manual are
adhered to.
Incorrect use
of the assis-
tance system
Operator
Operator obli-
gations
Safety
Operator obligations
SmartFork
®
FrontCam ATEX for use in the Ex zone - BVS 20 ATEX E 108 X
16
EN