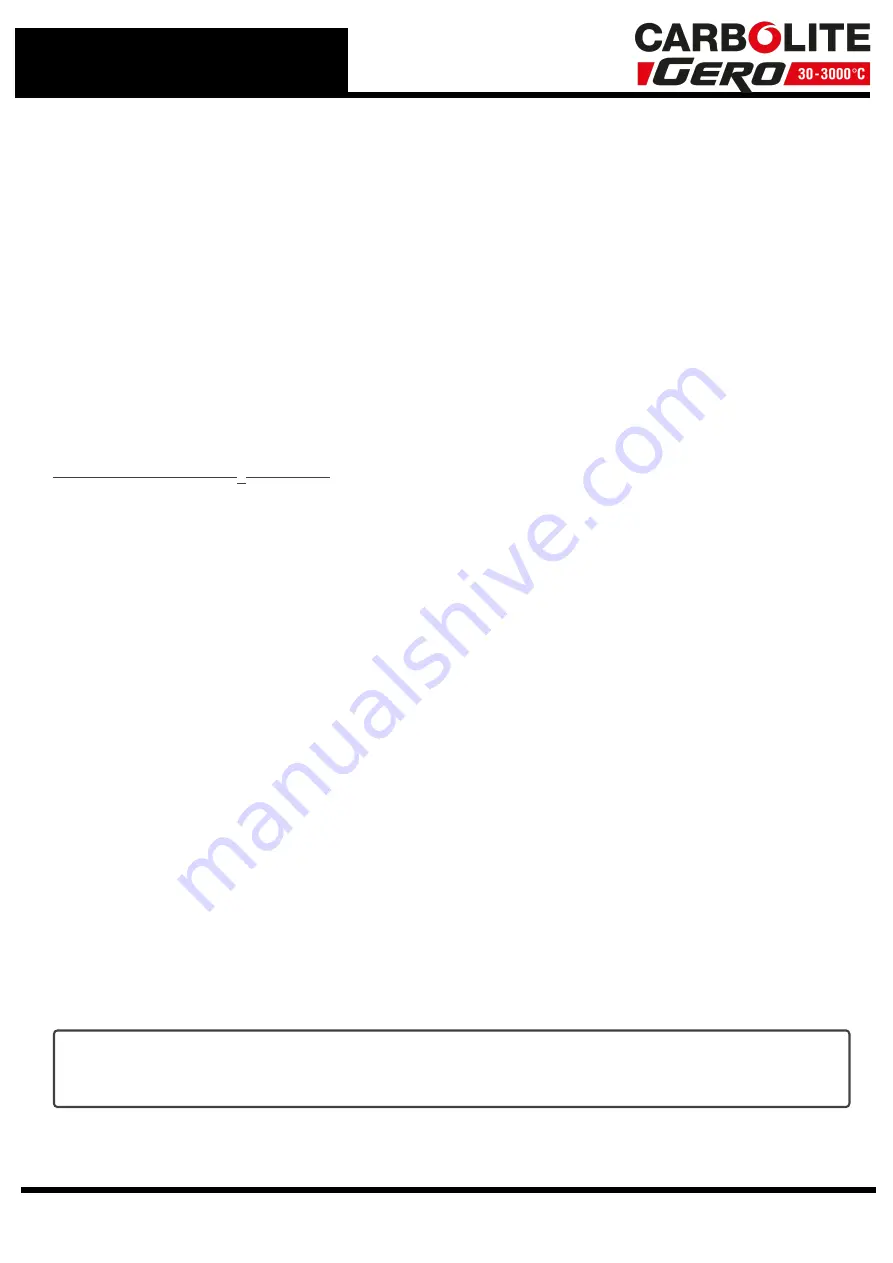
3.8
Gas Connections
3.8.1
Furnaces for CO/ CO
2
and Air Test Gases with N
2
Purge Gas
See below if a mixer box for separate CO & CO
2
inputs is supplied.
Note
: The gas supply pressure required is 4 psi (0.276 bar) and must not exceed this.
There are three gas connections on the side of the furnace, CO/ CO
2
pre mixed
'reducing' atmosphere gas, Air 'oxidising' gas and N
2
'Purge' gas. See fig 11a. It is
recommended that the gases are supplied to the furnace via separate isolation valves
that can be quickly switched off in the event of an emergency or potential hazard
without danger to the operator. See section 1.2.
The 'Purge' gas line is pre-set to allow a flow of N
2
into the work tube equal to 6 litre/
minute, the 'oxidising' and 'reducing' atmosphere gases have adjustable flow via the
flow meters on the front of the furnace. See fig 11a. The gas supply fittings are 6 mm x
1/8" BSP adaptors suitable for connecting 6 mm copper tube.
Separate CO and CO
2
supplies.
If a mixer box is supplied, separate input connections of CO and CO
2
may be made to
the lower connections at the back of the box. A pipe from the upper connection is to
be taken to the CO/ CO
2
inlet on the furnace.
The box is fitted with two flow-meters which may be adjusted to ensure that equal
mixtures of CO and CO
2
are supplied. The box also contains two non-return valves to
ensure that neither gas can flow back out of either inlet connection.
3.8.2
Furnaces for H
2
and CO
2
Test Gases with CO
2
Purge Gas.
Note
: The gas supply pressure required is 4 psi (0.276 bar) and must not exceed this.
There are three gas connections on the side of the furnace, CO
2
'oxidising' atmosphere
gas, H
2
(mixed with CO
2
in the work tube) 'reducing' atmosphere gas and CO
2
'Purge'
gas. See fig 11a. It is recommended that the gases are supplied to the furnace via
separate isolation valves that can be quickly switched off in the event of an emergency
or potential hazard without danger to the operator. See section 1.3.
The 'Purge' gas line is pre-set to allow a flow of CO
2
into the work tube equal to 6 litre/
minute, the 'oxidising' and 'reducing' atmosphere gases have adjustable flow via the
flow meters on the front of the furnace. See fig 11a. The gas supply fittings are 6 mm x
1/8" BSP adaptors suitable for connecting 6 mm copper tube.
3.9
Camera Mounting and Connections
Fit the camera mounting bracket onto the door arm as shown in fig 5c and 5d. Note that
the camera shown in fig 5c and 5d is not fitted for this operation.
Note: Depending on the age of your furnace, it will have one of two camera mount
fittings. Older models will have the type 1 fitting, while newer models will have the
type 2 fitting.
18
Summary of Contents for CARBOLITE GERO CAF G5
Page 63: ...Fig 3 Front Tube Seal Assembly Fig 4 Door Arm Assembly 63 ...
Page 64: ...Fig 5a Camera Mounting Bracket Fig 5b Lens and Camera Assembly 64 ...
Page 65: ...Fig 5c Sliding the Camera Mounting Bracket Assembly onto the Door Arm 65 ...
Page 66: ...Fig 5d Securing the Camera Mounting Bracket Assembly to the Door Arm 66 ...
Page 67: ...Fig 5e Mounting the Lens and Camera Assembly 67 ...
Page 68: ...Fig 5f Lens and Camera Assembly in Position 68 ...
Page 69: ...Fig 6a Rear View of the Standard CAF G5 Furnace Showing Brick Box Assembly 69 ...
Page 71: ...Fig 7 Front Tube Seal Position 71 ...
Page 72: ...Fig 8 Tube End Seal Assembly Tightening Sequence Fig 9 Work Tube Front Support 72 ...
Page 73: ...Fig 10 Fitting the Door Arm Assembly Fig 10a Adjusting the Door Arm Assembly 73 ...
Page 74: ...Fig 11a Furnace Case and Controls 74 ...
Page 75: ...Fig 11b Gas Inlet Pipe Fig 12 Positioning the Furnace 75 ...
Page 77: ...Fig 13c Loading Samples into the Work Tube 77 ...
Page 78: ...Fig 16 File Folder 78 ...
Page 79: ...Fig 17 Door Arm Assembly Exploded View 79 ...
Page 82: ...SST DT HT FT Fig 18 Report Sheet Page 2 Side View Plan View Fig 19 Formed Wire Sample 82 ...
Page 83: ...Fig 20 Sample Carrier Sample Tiles and Sample Positions 83 ...
Page 84: ...Fig 21a Coal and Coke Test Piece Mould Fig 21b Biomass Test Piece Mould and Hand Press 84 ...
Page 85: ...Fig 22 Sample Loading Tool Fig 23 Camera Ethernet Connection 85 ...
Page 86: ...Fig 24 LED Driver Connection 86 ...
Page 87: ...Notes Service Record Engineer Name Date Record of Work ...