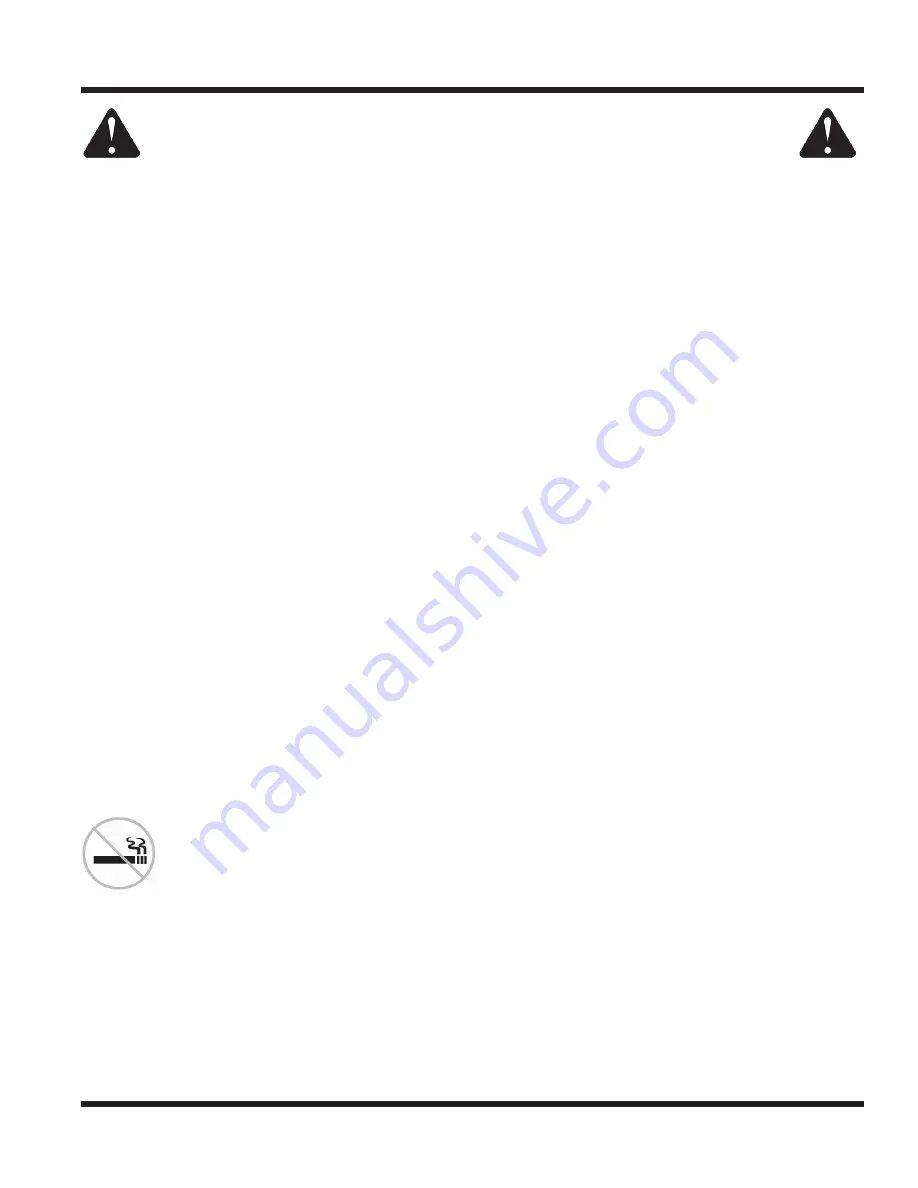
SAFETY
Safety - 11
General Safety Procedures
for Ventrac Power Units, Attachments, & Accessories
Maintenance
• Keep all safety decals legible. Remove all grease dirt, and debris from safety decals and instructional labels.
• If any decals are faded, illegible, or missing, contact your dealer promptly for replacements.
•
When new components are installed, be sure that current safety decals are affixed to the replacement
components.
• If any component requires replacement, use only original Ventrac replacement parts.
•
Always turn the battery disconnect to the Off position or disconnect the battery before performing any
repairs. Disconnect the negative terminal first and the positive terminal last. Reconnect the positive
terminal first and the negative terminal last.
• Keep all bolts, nuts, screws, and other fasteners properly tightened.
•
Always lower the attachment to the ground, engage parking brake, shut off engine, and remove the
ignition key. Make sure all moving parts have come to a complete stop before cleaning, inspection,
adjusting or repairing.
• If the power unit, attachment, or accessory requires repairs or adjustments not instructed in the operator’s
manual, the power unit, attachment, or accessory must be taken to an authorized Ventrac dealer for service.
• Never perform maintenance on the power unit and/or attachment if someone is in the operator’s station.
• Always use protective glasses when handling the battery.
• Check all fuel lines for tightness and wear on a regular basis. Tighten or repair them as needed.
•
To reduce the hazard of fire, keep the battery compartment, engine, and muffler areas free of grass,
leaves, and excessive grease.
•
Do not touch the engine, the muffler, or other exhaust components while the engine is running or imme
-
diately after stopping the engine. These areas may be hot enough to cause a burn.
•
Allow the engine to cool before storing and do not store near an open flame.
•
Do not change the engine governor settings or over-speed the engine. Operating engine at excessive
speed may increase the hazard of personal injury.
• Springs may contain stored energy. Use caution when disengaging or removing springs and/or spring
loaded components.
• An obstruction or blockage in a drive system or moving/rotating parts may cause a buildup of stored
energy. When the obstruction or blockage is removed, the drive system or moving/rotating parts may
move suddenly. Do not attempt to remove an obstruction or blockage with your hands. Keep hands,
feet, and clothing away from all power-driven parts.
•
Dispose of all fluids in accordance with local laws.
Fuel Safety
•
To avoid personal injury or property damage, use extreme care in handling gasoline. Gaso
-
line is extremely flammable and the vapors are explosive.
•
Do not refuel machine while smoking or at a location near flames or sparks.
• Always refuel the machine outdoors.
• Do not store machine or fuel container indoors where fumes or fuel can reach an open
flame, spark, or pilot light.
• Only store fuel in an approved container. Keep out of reach of children.
•
Never fill containers inside a vehicle or on a truck or trailer bed with a plastic liner. Always place containers
on the ground away from your vehicle before filling.
• Remove machine from the truck or trailer and refuel it on the ground. If this is not possible, refuel the
machine using a portable container, rather than from a fuel dispenser nozzle.
• Never remove fuel cap or add fuel with the engine running. Allow engine to cool before refueling.
• Never remove fuel cap while on a slope. Only remove when parked on a level surface.
• Replace all fuel tank and container caps securely.