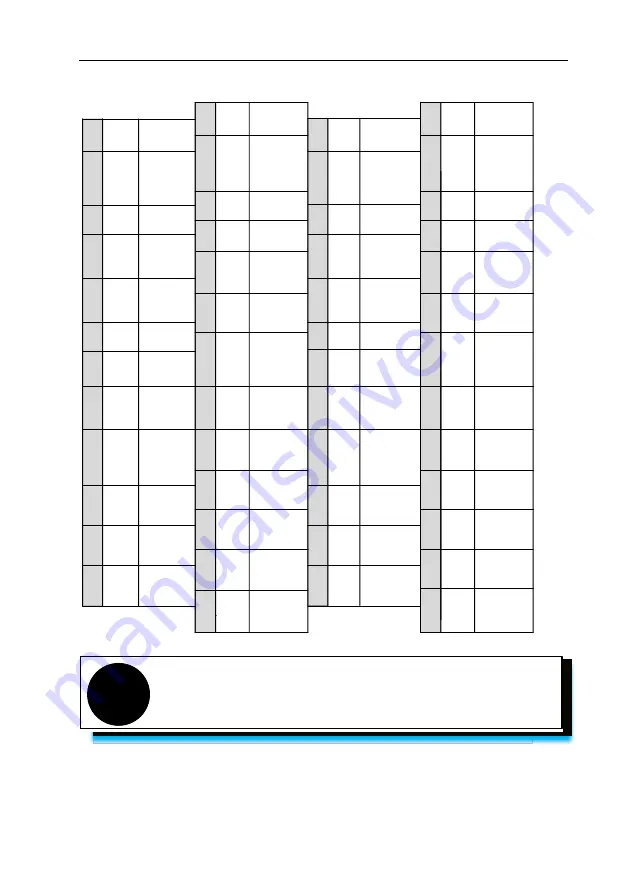
3 Wiring and Connections
36 SD780 Series Servo Technical Manual
3.7 Definition of CN1 Terminal
2
SG
Signal
ground
4
SEN
Requirement
input of
encoder
absolute data
(SEN)
6
SG
Signal ground
Signal ground
3
PL1
OC power
output of
command
pulse
5
V - REF
Speed
command
input
1
SG
8
/ PULS
Pulse
command
input
7
PULS
Pulse
command
input
10
SG
Signal
ground
9
T - REF
Torque
command
input
27
/SO 2 +
(TGON+)
General sequence
control output 2
29
/SO 3 +
( S -
RDY +)
General sequence
control output 3
31
ALM+
Servo alarm
output
33
PAO
A phase of
encoder
pulse division output
35
PBO
B phase of
encoder pulse
division output
26
/SO 1 -
(V-CMP-)
General sequence
control output 2
28
/SO 2 -
(TGON-)
30
/SO 3 -
(S - RDY-)
32
ALM -
Servo alarm
output
34
/PAO
A phase of
encoder pulse
division output
11
SIGN
Sign
command
input
36
/PBO
B phase of
encoder pulse
division output
12
/SIGN
Sign
command
input
37
STO
Safe torque limit
13
PL2
OC power
output of
command
pulse
14
/CLR
Clearance
input of
position
deviation
39
/SI 9
General
sequence
control input 9
/SI 8
38
General
sequence
control input 8
16
OCP
OC power
input of
command
pulse
CLR
Clearance
input of
position
deviation
15
41
/SI 3
( P -
CON )
General
sequence
control input 3
40
/SI 0
(/ S - ON )
General
sequence
control input 0
18
PL3
OC power
output of
command
pulse
17
OCS
OC input of
pulse
direction
43
/SI 2
( N - OT )
General
sequence
control input 2
42
/SI 1
( P - OT )
General
sequence
control input 1
20
/ PCO
C phase of
encoder
pulse division
output
19
PCO
C phase of
encoder
pulse division
output
44
/SI 4
(/ ALM -
RTS )
General
sequence
control input 4
22
BAT -
Battery( -) of
absolute
encoder
21
BAT +
Battery (+) of
absolute
encoder
45
/SI 5
(/P -CL )
General
sequence
control input 5
46
/SI 6
(/ N - CL )
General
sequence
control input 6
47 + 24 VIN
Power input of
sequence
control input signal
48
PSO
Position output
of absolute
encoder
24
OCS
OC input of
pulse
clearance
23
OCZ
OC output of
Z phase
pulse division
49
/PSO
Position
output of
absolute
encoder
25
/SO 1 +
( V -
CMP +)
General
sequence
control output 1
50
TH
Overheat
protection
input of linear
motor
Cautions
!
When tightening the screw of CN1 terminal, the torque shall not be greater than 0.2N. M, otherwise, the
screw will slide.