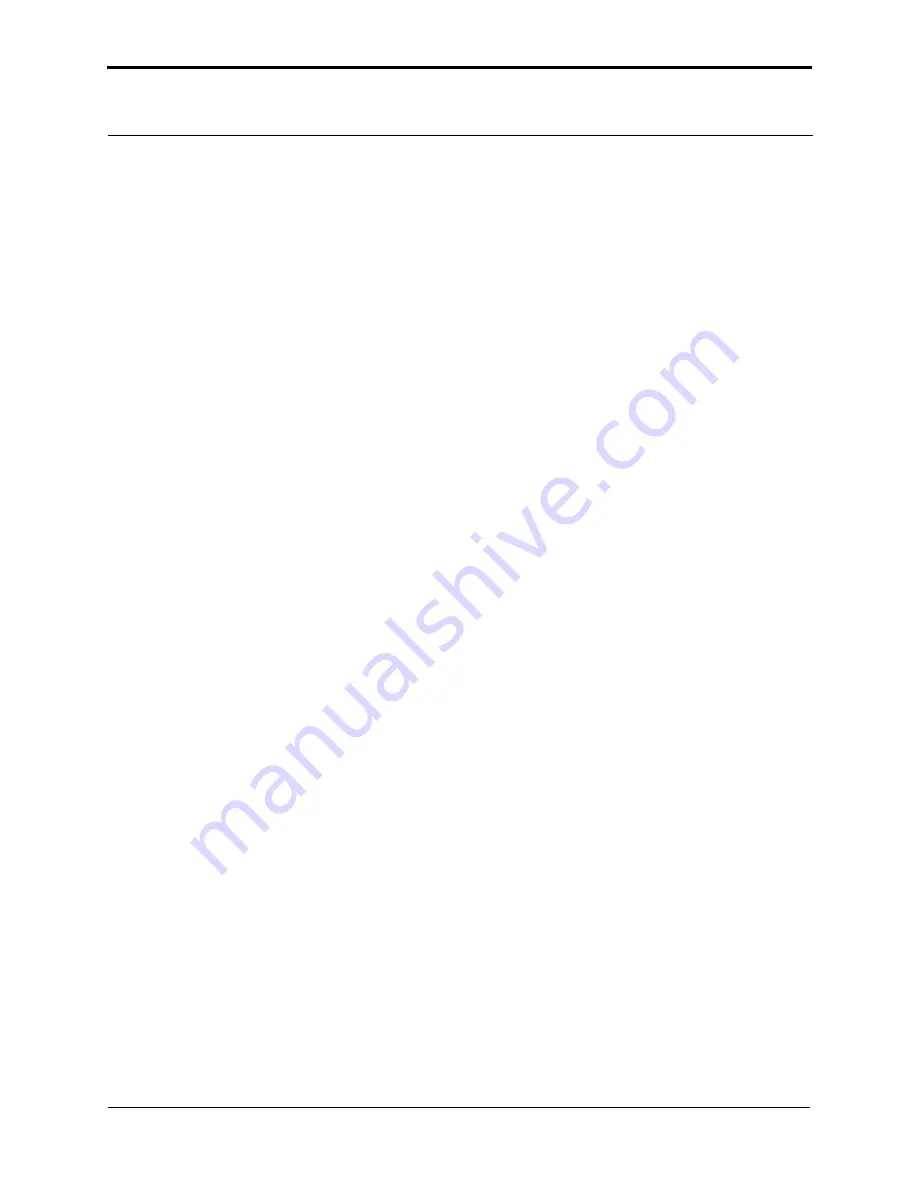
Scanning Tunneling Microscopy (STM)
Introduction
176
Dimension 3100 Manual
Rev. D
11.1 Introduction
STM relies on “tunneling current” between the probe and the sample to sense the topography of the
sample. The STM probe, a sharp metal tip (in the best case, atomically sharp), is positioned a few
atomic diameters above a conducting sample which is electrically biased with respect to the tip. At
a distance under 1 nanometer (0.001µm), a tunneling current will flow from sample to tip. In
operation, the bias voltages typically range from 10 to 1000mV while the tunneling currents vary
from 0.2 to 10nA. The tunneling current changes exponentially with the tip-sample separation,
typically decreasing by a factor of 2 as the separation is increased by 0.2nm. The exponential
relationship between the tip separation and the tunneling current makes the tunneling current an
excellent parameter for sensing the tip-to-sample separation. In essence, a reproduction of the
sample surface is produced by scanning the tip over the sample surface and sensing the tunneling
current.
11.1.1 Overview of STM
The STM option is generally employed under the following conditions:
•
For samples having deeply relieved features, where AFM probes may not be able to
penetrate, and/or where feature verticality is very close to 90 degrees.
•
On polished samples, where it is necessary to image different layers having similar
topography but different electrical conductivities.
•
Under conditions where contact with the sample surface is prohibited.
STM relies on a precise scanning technique to produce very high-resolution, three-dimensional
images of sample surfaces. The STM scans the tip over the sample surface in a raster pattern while
sensing and outputting the tunneling current to the NanoScope control station. The digital signal
processor (DSP) in the workstation controls the Z position of the piezo based on the tunneling
current error signal. The STM operates in both the “constant height” and “constant current” data
modes, depending on a parameter selection in the STM Control Panel. The DSP always adjusts the
height of the tip based on the tunneling current error signal, but if the feedback gains are low, the
piezo remains at a nearly “constant height” and tunneling current data is collected. With the gains
high, the piezo height changes to keep the tunneling current nearly constant, and the change in
piezo height is collected by the system. The exponential relationship between the tip separation and
the tunneling current allows the tip height to be controlled very well. For example, if the tunneling
current stays within 20 percent of the setpoint value (the current to be maintained by the feedback
system), the variation in the tip-sample separation is less than 0.02nm.
The STM tip is held using a dedicated STM tip holder which plugs into the end of the Dimension
head’s tube (see
Summary of Contents for Dimension 3100
Page 12: ...xii Dimension 3100 Manual Rev D ...
Page 20: ...List of Figures xx Dimension 3100 Manual Rev D ...
Page 72: ......
Page 106: ......
Page 118: ......
Page 214: ...Scanning Tunneling Microscopy STM Etching Tungsten Tips 194 Dimension 3100 Manual Rev D ...
Page 222: ......
Page 266: ......
Page 274: ......