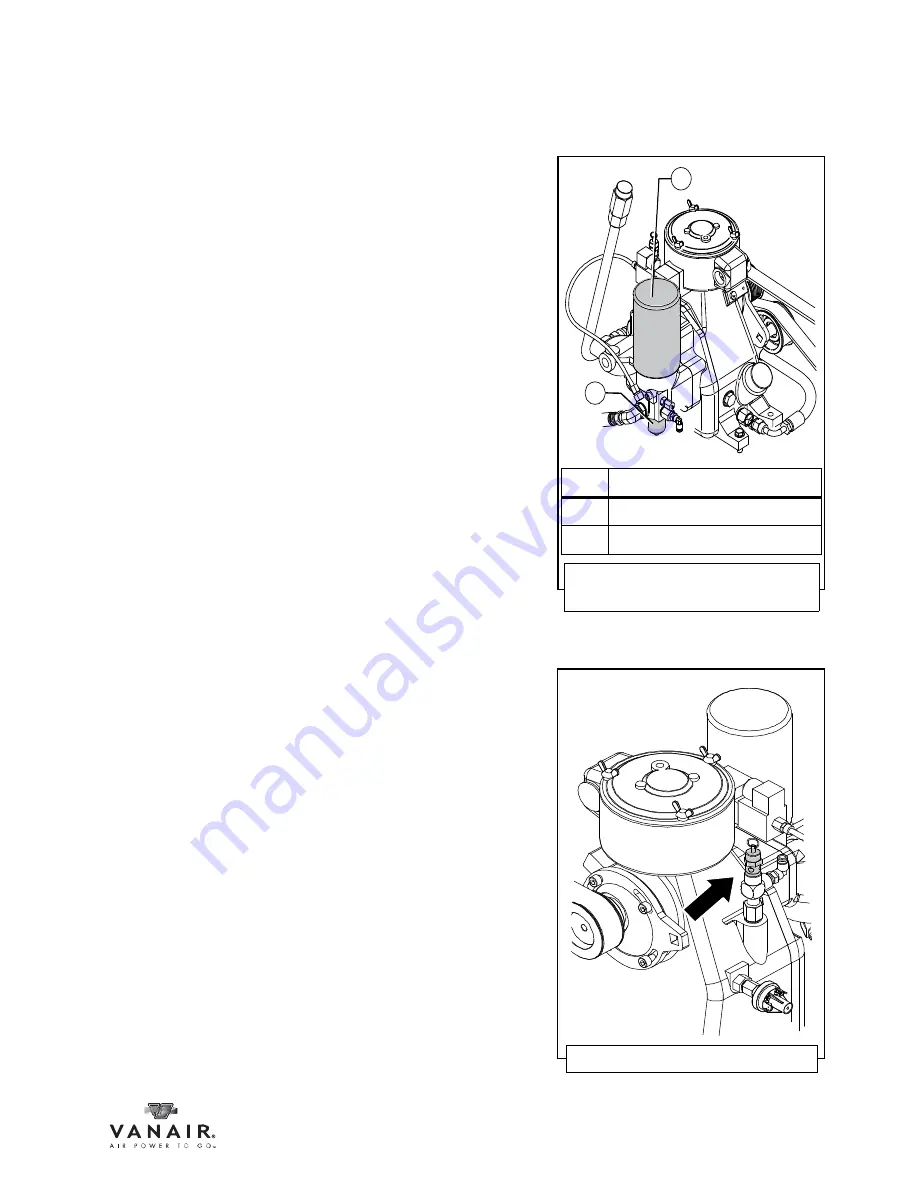
AIR N ARC
®
300 SERIES ALL-IN-ONE POWER SYSTEM
®
SECTION 2: DESCRIPTION
090010-OP_r0
PAGE - 23
KEY
DESCRIPTION
A
AIR/OIL COALESCER
B
MINIMUM PRESSURE CHECK
Figure 2-4: Spin-on Air/Oil Coalescer
& Minimum Pressure/Check Valve
A
B
assembly. The coalescer element recovers the finer
particles of residual oil that remain in the air after primary
separation occurs. The oil that is collected in this element
is “scavenged” back to the compressor unit for re-use.
This element will need to be replaced from time to time
as part of normal maintenance.
For routine maintenance
of the spin-on air/oil coalescer consult
Sections 6.2
and
6.3
for schedule intervals, and
Section 6.5.6
for the
specific coalescer maintenance procedure.
2.2.5 MINIMUM PRESSURE/CHECK VALVE
See
Figure 2-4
.
This combination valve is located on
the underside of the filter support housing and serves two
functions. First, the minimum pressure valve maintains a
pressure of approximately 65 psig in the compressor to
ensure oil injection during load conditions and also to
maintain effective oil separation. Once this internal
pressure is exceeded, it will allow air to pass downstream
to the service outlet. The discharge check valve prevents
air in the service line from venting down through the
compressor during unload (when the compressor
automatically relieves to 40 psig during non-use of the
service air) and during shutdown.
2.2.6 PRESSURE RELIEF VALVE
See
Figure 2-5
.
The pressure relief valve is the last
safety device that will be activated. It is a spring-backed
normally closed valve that will vent excess pressures to
the atmosphere when excessive pressures are reached.
The Air N Arc 300 Series Power System is equipped with
a 200 psig relief valve. As the pressure begins to
approach 200 psig, it will crack open to slowly relieve
pressure. If pressure continues building through this
venting, it will be fully open at 200 psig. Both air and oil
will be expelled from this valve.
2.2.7 ADJUSTABLE PRESSURE SWITCH
See
Figure 2-6
.
The adjustable pressure switch is
mounted on the side of the battery support bracket and is
plumbed into pressure on the upstream side of the
minimum pressure valve. The purpose of the switch is to
provide a control for the inlet valve control solenoid,
much like a pneumatic regulator valve. When the
pressure in the service line drops below the set limit, it
reactivates the inlet valve control solenoid, allowing the
inlet valve to suck in more air. The pressure switch has
both a high and low pressure setting.
Although the pressure cut-in and cut-out pressures are
pre-set at the factory, they may be manually adjusted.
Figure 2-5: Pressure Relief Valve