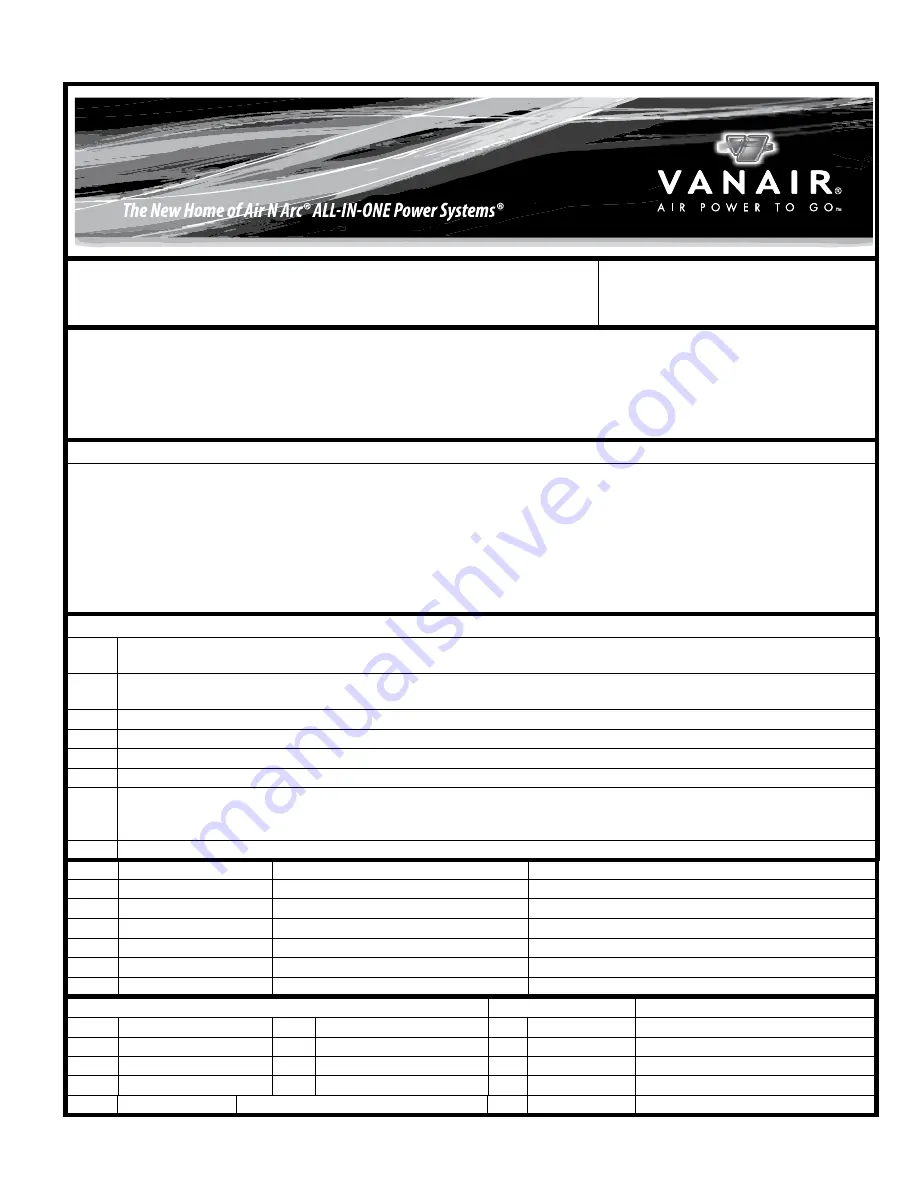
RETURN MATERIAL AUTHORIZATION FORM
Ph. 219-879-5100
Fax. 219-879-5335
Return
Material
Authorization
10896 W. 300 N.
Michigan City, IN 46360
S / N: 30 _____________________
Customer: ____________________________
Date:____________________________
AnA S/N:_____________________
RMA#: ____________________________
Contact:____________________________
Email:_____________________________________________________________
Phone : ___________________________
Fax : ________________________
Address : __________________________________________________________________
Tech : _______________________
Dealer : ________________ PO# : ___________________________________________
GENERAL INFORMATION
All returns are sent back for warranty consideration and are subject to factory inspection and analysis. Vanair® is not
responsible for shipping damage due to insufficient or improper packaging methods. Failure to identify returned goods
with the assigned RMA number on the outside of the shipping package will delay processing or result in the shipment
being returned, freight collect. To receive warranty parts, a credit card or Purchase Order must be given to the service
technician. Once the disposition of the part is determined, (I.E. manufacturing defect or other) Vanair will credit your
account if covered by warranty. You can also contact the Service Department by email at [email protected] if you
have any questions.
Return parts to the address listed above.
INSTRUCTIONS TO CUSTOMERS
1
Product must be returned within 30 days from the day the RMA is issued. The RMA is void thereafter and any parts received
after this time frame will be returned freight collect or not accepted.
2
The RMA number must be placed on the outside of the shipping package. Do not write the RMA number on the component
with permanent marker, this damages the component. Please use a tag.
3
Components (including generators) must be returned completely assembled with no loose parts or they will not be accepted.
4
A copy of the form must be included with all paperwork.
5
No product will be accepted freight collect unless prior arrangements have been made.
6
We will not accept any parts returned on an invoice. They will be returned freight collect.
7
Any invoice issued for labor claims must include the RMA number assigned on this form, the 30-XXXXX number for the unit,
and be invoiced for any labor claims within 30 days of the work completion. The allowable Vanair labor rate is $65.00 per hour
for all authorized work done in the United States.
8
All warranty claims must be pre-approved by Vanair or they will not be accepted.
Qty.
Part #
Description
Reason for return
Final Disposition of Goods
Notifications
Additional Notes
No Credit
Return to Customer
Quality Control
Return to Stock
Issue Credit for Parts
Operations
Scrap Goods
Issue Credit for Freight
Purchasing
Ret to Vendor
Accounting
Part Invoice #:
Shipping