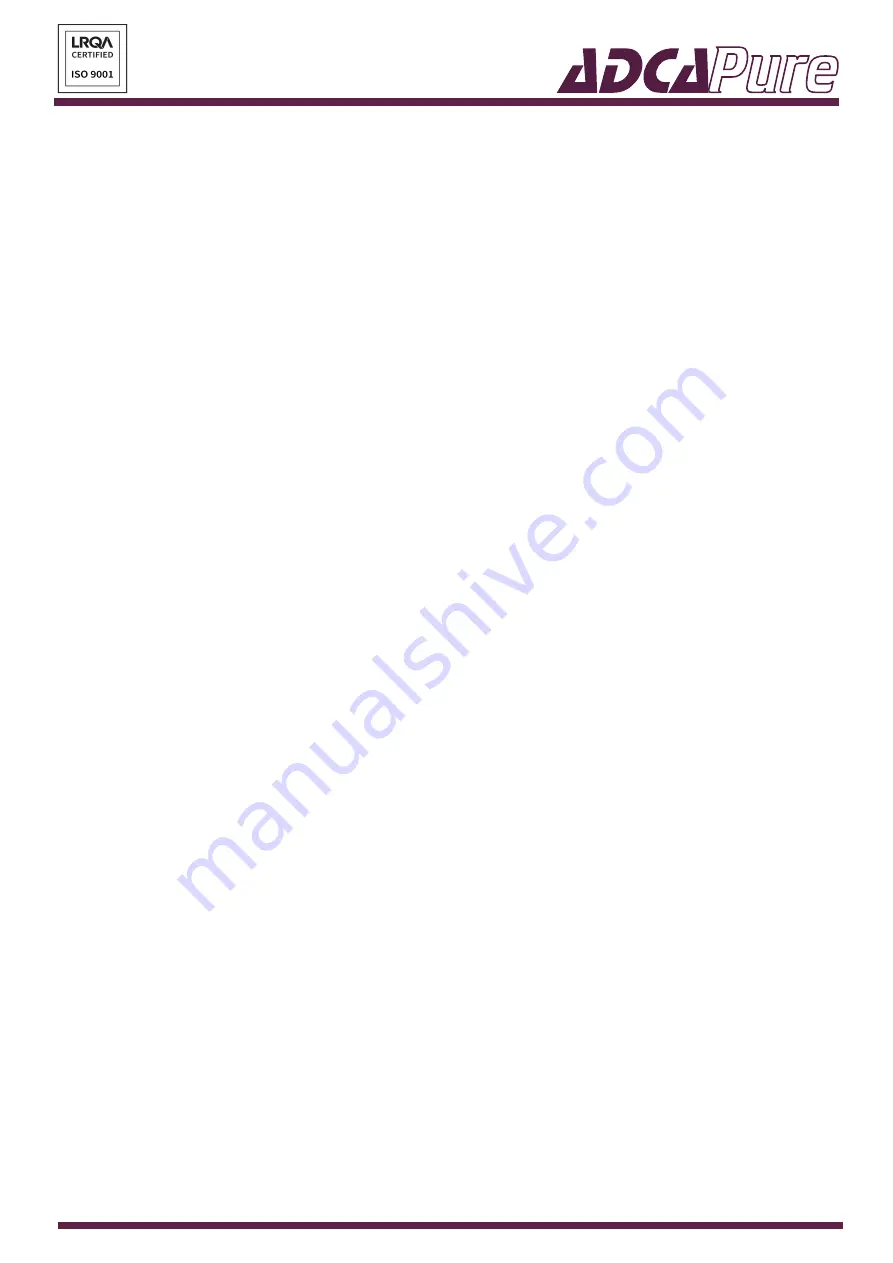
VAL
S
TEAM
ADCA
Produced in accordance with Sound Engineering Practices of the European PED - Pressure Equipment Directive.
IMI PS130.08 E 00.22
14
4.2. Installation procedure
1.
Remove plastic film and other packaging, as well as the protective covers which
are placed on clamps or ETO connections. Make sure the regulator is free from
foreign matter.
2.
Handle the regulator carefully to prevent damage to its surface finish.
3. The regulator recommended installation position is horizontal with the adjustment
knob pointing upwards. Other installation positions may increase wear and shorten
its service lifetime.
4. The regulator has an arrow or inlet/outlet designations, be sure that it is installed in
the appropriate direction according to fluid flow.
5. When a clamp ferrule version is being installed, use appropriate gaskets. Sanitary
clamps must respect the system operating limit conditions.
6. When an ETO version is being installed, the welding should be carried out by
qualified personnel following an appropriate orbital welding procedure.
7. For dome-loaded regulators, connect the control pressure line to the dome chamber
threaded port using suitable fittings and tubing.
5. START-UP
Before performing the start-up procedure, refer to section 1 – Safety information.
The start-up procedure must be followed every time the product is put back into service.
5.1. Preparation for start-up
Before starting up, make sure the following conditions are met:
• All works on the system have been completed.
• All the necessary safety devices have been installed.
• When required, warning notices are used to alert others that the system is starting
up.
• The product is correctly installed – see section 4 – Installation.
• Referring to these Installation and Maintenance Instructions (IMI), Information Sheet
(IS) and nameplate, check that the product is suitable for the intended installation:
temperature, medium, pressure, temperature, etc. – see section 1.2 – Intended
use.
•
A safety check was performed by qualified personnel. Checking for leaks, structural
damage and integrity of system components.
• The adjustment spring is completely relaxed. If not, release tension by turning the
adjustment knob (26) counterclockwise.