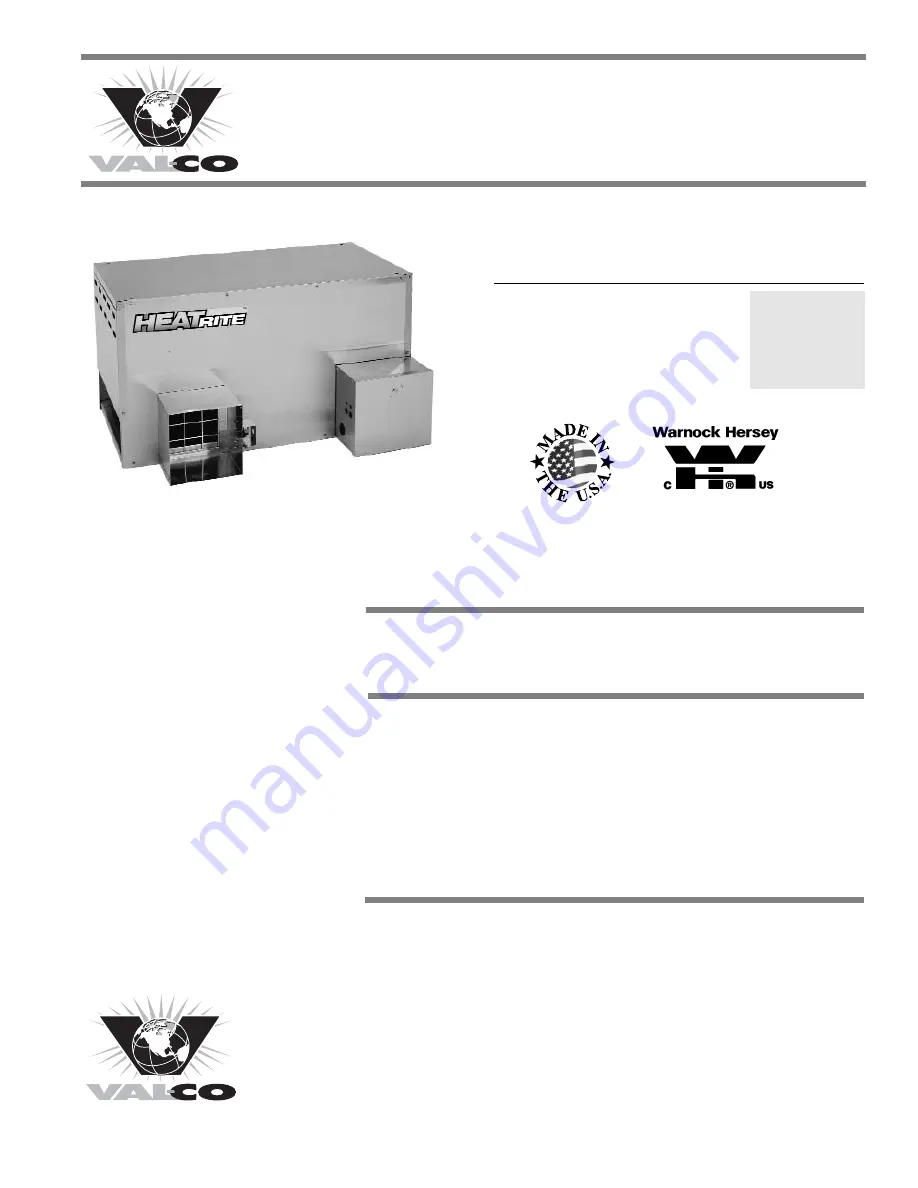
Congratulations!
You have purchased the finest agricultural building heater available.
Your new VAL-CO heater incorporates the benefits from the most experienced
manufacturer of heating products using state-of-the-art technology.
We, at VAL-CO,
thank you
for your confidence in our products and
welcome any suggestions or comments you may have......call us,
at 419-678-8731.
Owner's Manual and Instructions
Agricultural Animal Confinement Building Heaters
F150-81512-A
IGNITION OUTPUT
MODEL
TYPE
(BTUH)
60,000
Heat Rite
Pilot
225,000
Available in
either L.P. Vapor
Withdrawal or
Natural Gas
Configurations.
210 East Main Street, P.O. Box 117, Coldwater, OH 45828 USA
■
(419) 678-8731