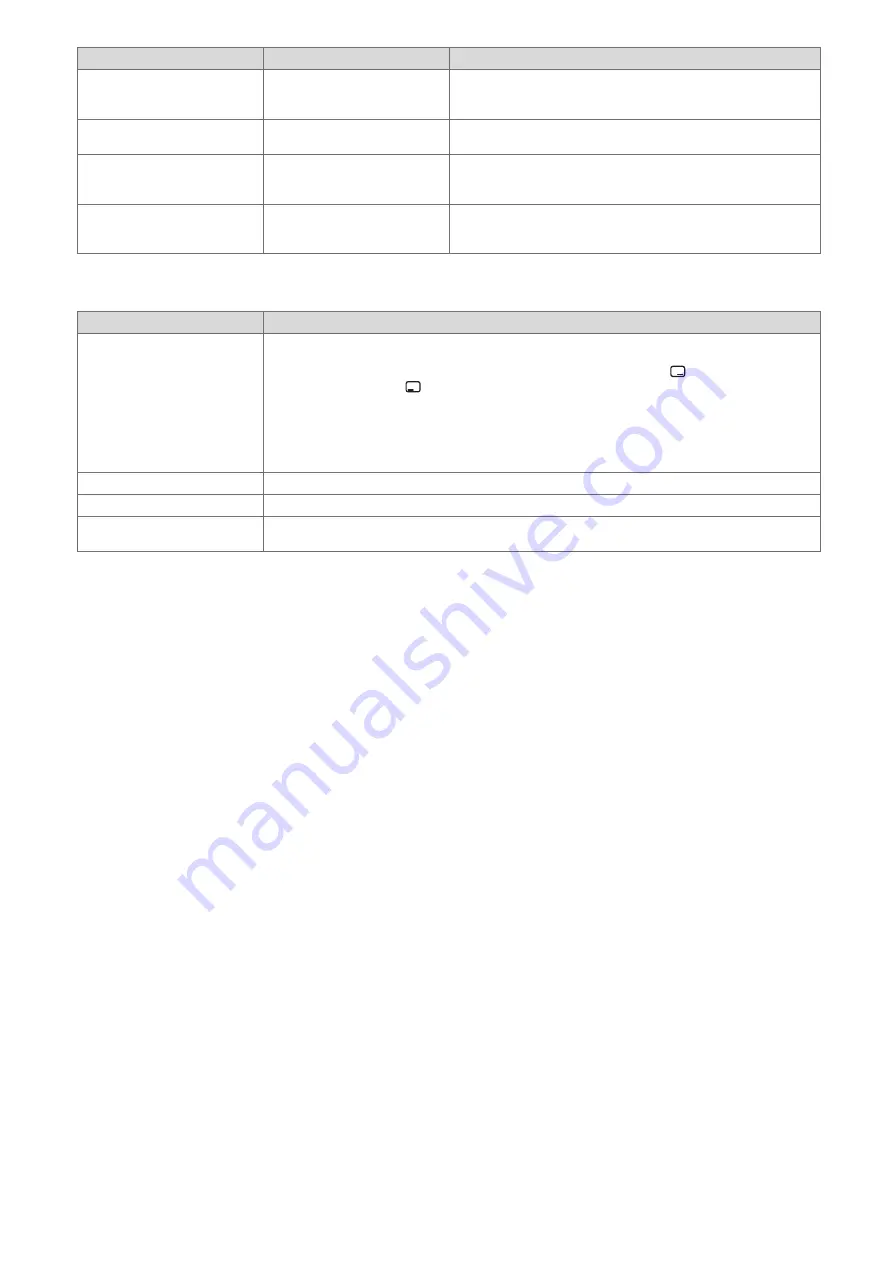
48
Installation and maintenance instructions ecoTEC pro 0020244995_04
Message
Possible cause
Measure
F.83
Fault: NTC temp. gradient
Temperature difference
between flow and return
temperature sensor is too small
▶
Check: Flow/return temperature sensor (function, correct
thermal connection), sufficient water volume.
F.84
Fault: NTC temp. diff. im-
plausible
Temperature difference is im-
plausible
▶
Check: Flow/return temperature sensor (correct thermal con-
nection, sensors are inverted).
F.85
Fault: NTCs fitted incor-
rectly
Flow/return temperat-
ure sensors returning
incorrect/implausible values
▶
Check: Flow/return temperature sensor (correct thermal con-
nection).
Communication fault
Communication fault between
the display and the PCB in the
electronics box
▶
Check: Cable/plug between the display and the PCB.
E
Check programmes
–
Overview
Check programme
Meaning
P.00 Purging
The internal pump is cyclically actuated. The heating circuit and the domestic hot water circuit are ad-
aptively purged by automatically switching the circuits using the automatic air vent (the automatic air
vent's cap must be loose). The active circuit is shown in the display. Press
once to start purging
the heating circuit. Press
once to end the purge programme. Note: The purge programme runs for
7.5 min per circuit and then terminates. Purging the heating circuit: Prioritising diverter valve in heat-
ing position, actuation of internal pump for 9 cycles: 30 sec. on, 20 sec. off. Display: Active heating
circuit. Purging the domestic hot water circuit: After the above-mentioned cycles have run or the right-
hand selection button has been pressed again: Prioritising diverter valve in the domestic hot water
position, actuation of the internal pump as above. Display: Active domestic hot water circuit.
P.01 Maximum load
After successful ignition, the product is operated at maximum heat input.
P.02 Minimum load
After successful ignition, the product is operated at minimum heat input.
P.06 Filling mode
The prioritising diverter valve is moved to the mid-position. The burner and pump are switched off (to
fill or drain the product).
Summary of Contents for ecoTEC pro VUW 6/5-3 Series
Page 1: ...en Installation and maintenance instructions ecoTEC pro VUW 6 5 3 0020244995_04 29 07 2020...
Page 57: ......
Page 58: ......
Page 59: ......