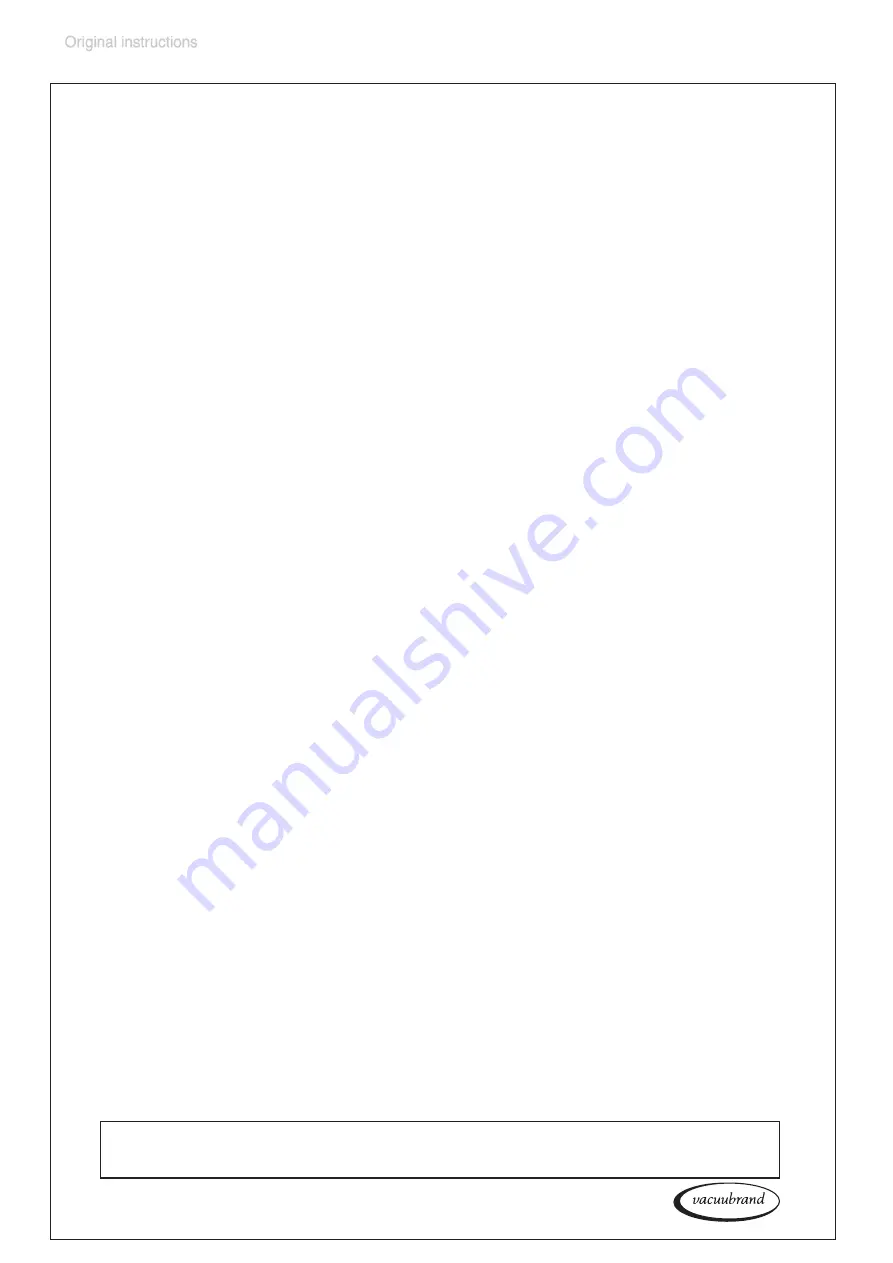
Health and safety clearance form
Health and safety clearance form
1. Device (Model): ..................................................................................................................................................
2. Serial no.: ...........................................................................................................................................................
3. Reason for return / malfunction: .........................................................................................................................
............................................................................................................................................................................
4. Has the device been used in a copper process step (e.g., semiconductor production):
☐
yes
☐
no
5. Substances (gases, liquids, solids, biological material, e. g. bacteria, viruses) in contact with the device /
which have been pumped:
............................................................................................................................................................................
............................................................................................................................................................................
............................................................................................................................................................................
............................................................................................................................................................................
6. Risk level of the used biological material:
☐
none
☐
1
☐
2*
☐
3**
☐
4**
* Contact the VACUUBRAND service absolutely before dispatching the device.
** Devices which have been in contact with biological substances of risk level 3 or 4 cannot be checked, main-
tained or repaired. Also decontaminated devices must not returned to VACUUBRAND due to a residual risk.
7. Radioactive contamination:
☐
yes
☐
no
8. Prior to return to the factory the device has been decontaminated:
☐
yes
☐
no
Description of the decontamination method and the test / verification procedure:
............................................................................................................................................................................
............................................................................................................................................................................
9. All parts of the device are free of hazardous, harmful substances:
☐
yes
☐
no
10. Protective measures required for service staff:
............................................................................................................................................................................
11. If the paint is damaged, we wish a repaint or a replacement of parts for reason of appearance
(repaint and replacement at customer’s expense):
☐
yes
☐
no
12. Legally binding declaration
We assure for the returned device that all substances, which have been in contact with the device are listed in
section 5 and that the information is complete and that we have not withheld any information. We declare that all
measures - where applicable - have been taken listed in section “Repair - Maintenance - Return - Calibration”.
By our signature below, we acknowledge that we accept liability for any damage caused by providing incom-
plete or incorrect information and that we shall indemnify VACUUBRAND from any claims as regards damages
from third parties. We are aware that as expressed in § 823 BGB (Public Law Code of Germany) we are directly
liable for injuries or damages suffered by third parties, particularly VACUUBRAND employees occupied with
handling/repairing the product. Shipping of the device must take place according to regulations.
Name: .................................................................. Signature: ...........................................................................
Job title: ................................................................... Company’s seal:
Date: ........................................................................
Release for repair grant by VACUUBRAND (date / signature)
:
...................................................................................................................
Protective measures:
☐ Protective gloves, safety goggles ☐ Hood ☐ External cleaning
VACUUBRAND GMBH + CO KG
Alfred-Zippe-Straße 4
97877 Wertheim - Germany
T +49 9342 808-5660 F +49 9342 808-5666
E-Mail: [email protected]
www.vacuubrand.com