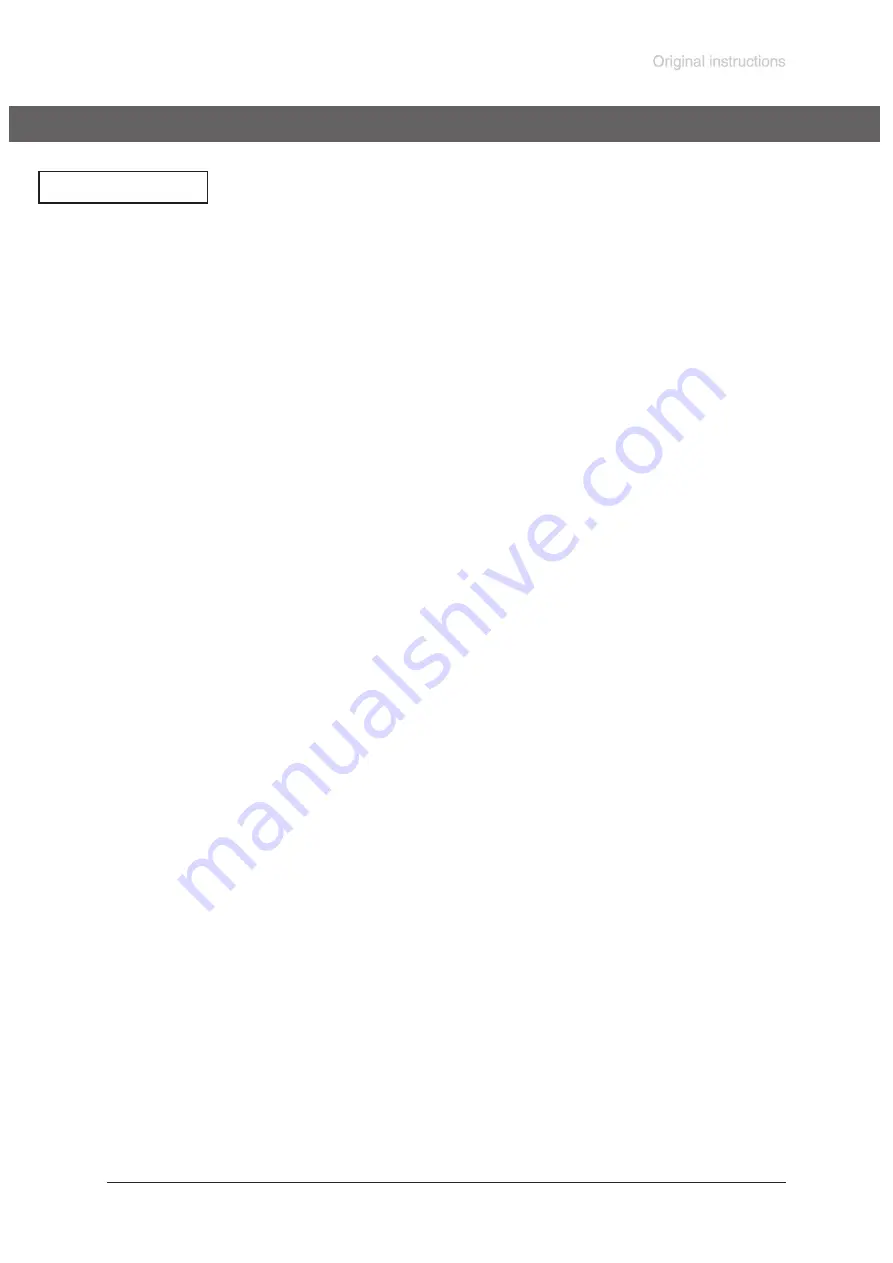
Documents are only to be used and distributed completely and unchanged. It is strictly the users´ responsibility to check carefully
the validity of this document with respect to his product. Manual-no.: 999069 / 28/04/2016
Every employer (user) is held responsible for the health and safety of his employ-
ees. This also applies to service personnel performing repair, maintenance, return
or calibration.
The
health and safety clearance form
informs the contractor about any possible
contamination of the device and forms the basis for the risk assessment.
In case of devices which have been in contact with biological substances of
risk level 2 contact the VACUUBRAND service absolutely before dispatching
the device. These devices have to be completely disassembled and decon-
taminated by the user prior to shipment. Do not return devices which have
been in contact biological substances of risk level 3 or 4.
These devices cannot
be checked, maintained or repaired. Also decontaminated devices must not returned
to VACUUBRAND due to a residual risk.
The same conditions apply to on-site work.
No repair, maintenance, return or calibration is possible unless the correctly
completed health and safety clearance form is returned. Devices sent are re-
jected if applicable.
Send a completed copy of the
health and safety clearance
form
to us in advance. The declaration must arrive before the equipment. Enclose a
second completed copy with the product.
Remove all components from the device that are no original VACUUBRAND compo-
nents. VACUUBRAND will not be responsible for lost or damaged components that
are no original components.
Drain the device completely of fluids and residues. Decontaminate the device.
Close all openings airtight especially if using substances hazardous to health.
To expedite repair and to reduce costs, please enclose a detailed description of the
problem and the product’s operating conditions with every product returned.
If you do not wish a repair on the basis of our
quotation
, the device may be returned
to you disassembled and at your expense.
In many cases, the components must be cleaned in the factory prior to repair.
For cleaning we use an environmentally friendly water based process. Unfortunately
the combined attack of elevated temperature, cleaning agent, ultrasonic treatment
and mechanical stress (from pressurised water) may result in damage to the paint.
Please mark in the health and safety clearance form if you wish a repaint at your
expense just in case such a damage should occur. We will also replace parts for cos-
metic reasons at your request and at your expense.
Before returning the device
Pack the device properly, if necessary, please order original packaging materials at
your costs.
Mark the package completely
Enclose the completed health and safety clearance form.
Notify the carrier of any possible contamination if required.
Scrapping and waste disposal
Dispose of the equipment and any components removed from it safely in accordance
with all local and national safety and environmental requirements. Particular care
must be taken with components and waste oil which have been contaminated with
dangerous substances from your processes. Do not incinerate fluoroelastomer seals
and O-rings. You may authorize us to dispose of the equipment
at
your expense.
Otherwise we return the device at your expense.
Repair - Maintenance - Return - Calibration
IMPORTANT