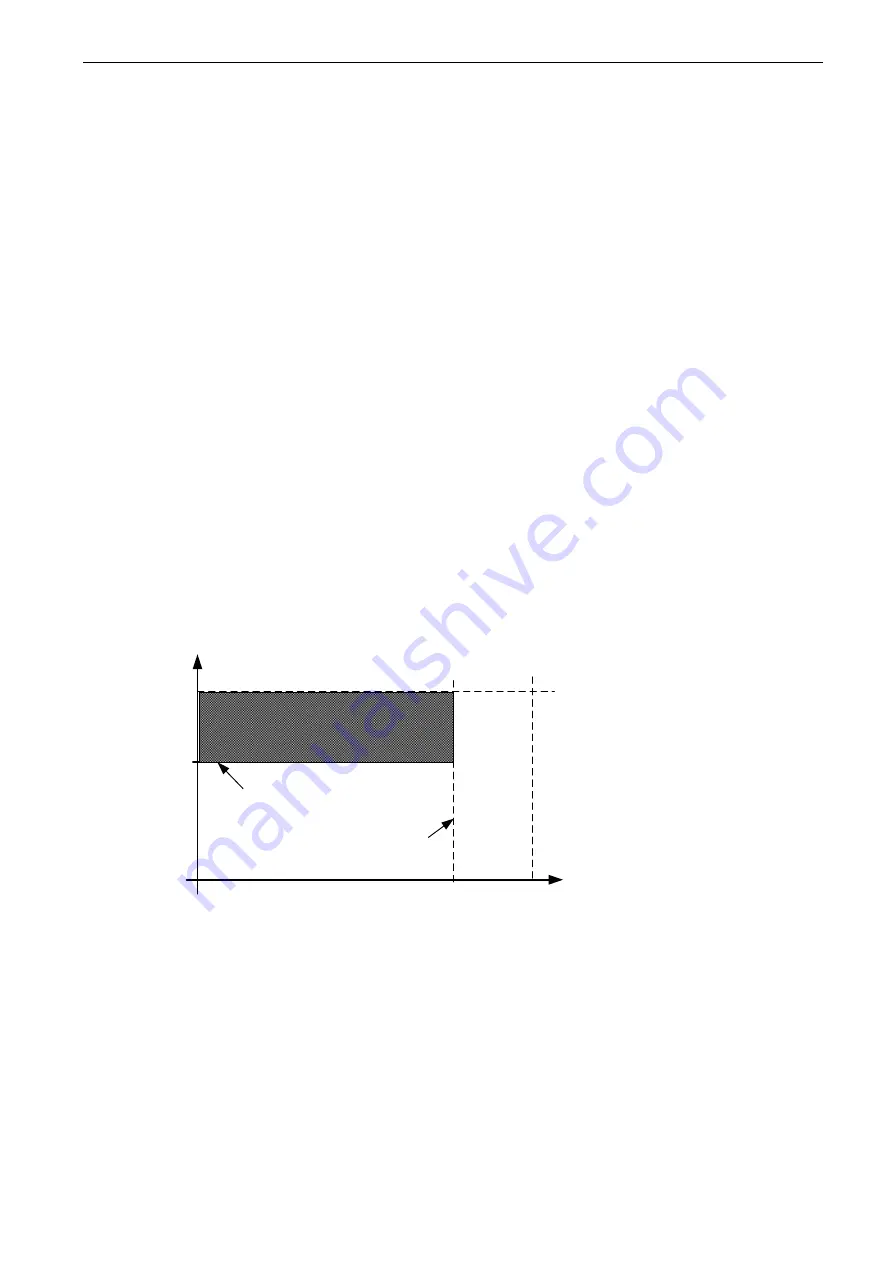
apfiff09 marine
VACON®
•
235
Local contacts: http://drives.danfoss.com/danfoss-drives/local-contacts/
Classified as Public
7.12.3
Stall protection
The motor stall protection protects the motor from short time overload situations such as one caused
by a stalled shaft. The reaction time of the stall protection can be set shorter than that of the motor
thermal protection. The stall state is defined with two parameters, Stall current and Stall frequency
limit. If the current is higher than the set limit and the output frequency is lower than the set limit, the
stall state is true. There is actually no real indication of the shaft rotation. Stall protection is a kind of
overcurrent protection.
P2.12.3.1 Stall protection
ID709
“Stall Protection”
0
= No response
1
= Warning
2
= Fault, stop mode after fault according to Stop Function
3
= Fault, stop mode after fault always by coasting
P2.12.3.2 Stall current limit
ID710
“Stall Current”
The current can be set to 0
…2*I
H
. For a stall stage to occur, the current must have
exceeded this limit. The software does not allow entering a greater value than 2*I
H
. If the
motor current limit is changed this parameter is automatically recalculated to the value
90% of motor current limit.
Note
: This limit must be set below the current limit in order for this function to operate.
P2.12.3.3 Stall frequency limit
ID712
“Stall Freq Lim”
The frequency can be set between 1-f
max
(Max Frequency).
For a stall state to occur, the output frequency must have remained below this limit for a
certain time. This function requires that the output frequency is 1 Hz below the frequency
reference before the stall time count is started.
Motor Current
Output Freq.
Stall Area
Stall Current
Limit
Stall Freq.
Limit
Summary of Contents for apfiff09 marine
Page 1: ...vacon nx ac drives apfiff09 marine application manual ...
Page 2: ......
Page 310: ......