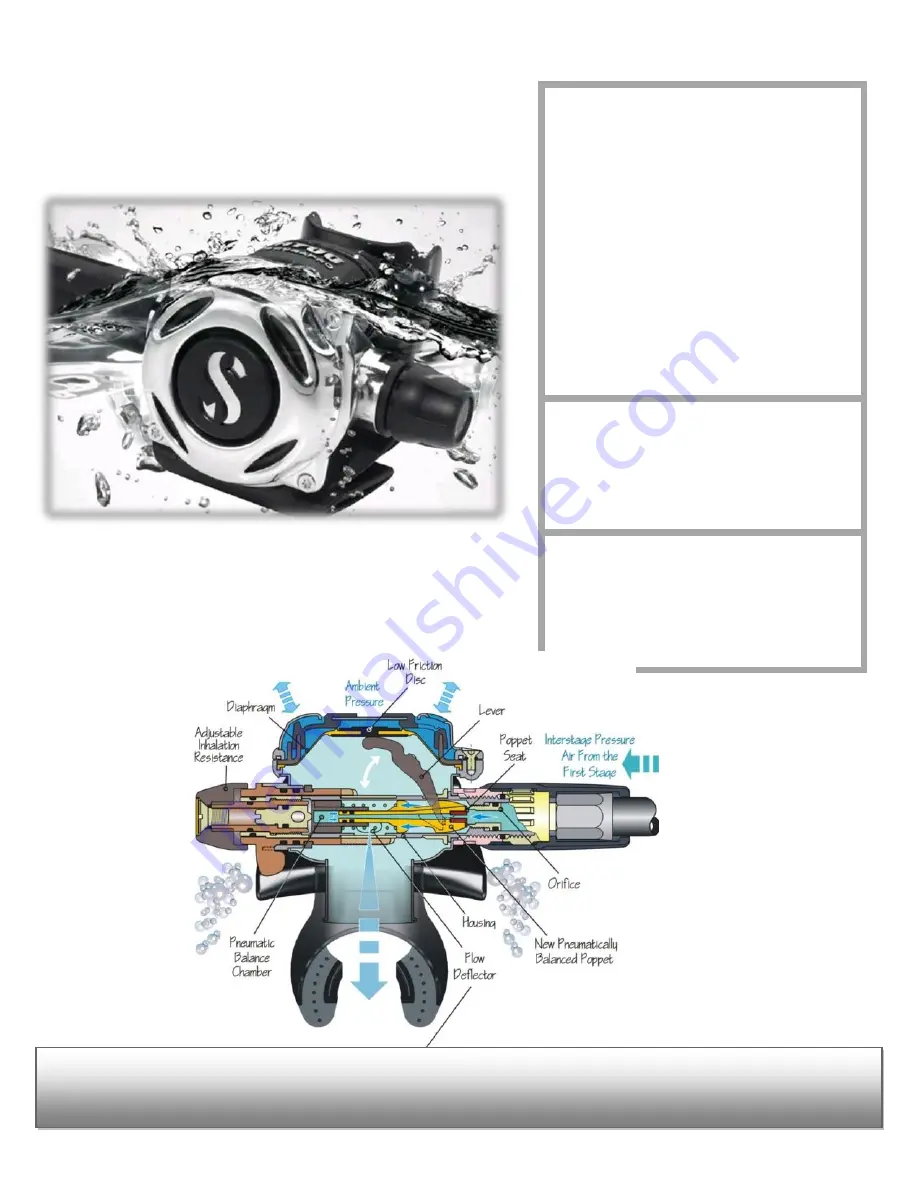
A700 Step-
by-step
maintenance
procedures.
Refer to schematic for
part identification.
Rene' Dupre' - Technical Training
Manager
–
8/2009 Copyright,
Modified 7/2010
Important note
: The following information is not designed to be a complete training guide for servicing the listed SCUBAPRO
regulators. All SCUBAPRO technicians are required to attend an annual service training program to insure safe handling and
servicing of SCUBAPRO products. All SCUBAPRO technicians must be employed by an authorized SCUBAPRO facility.