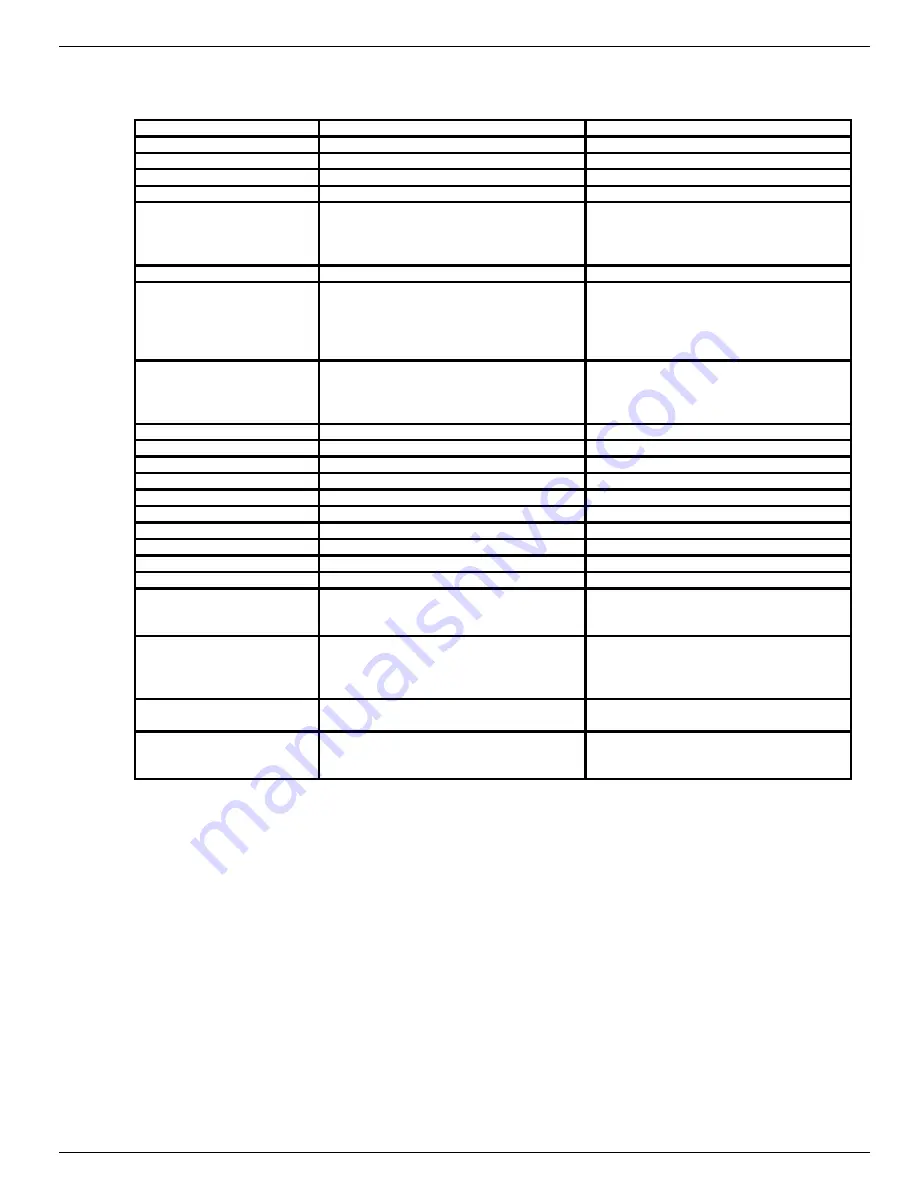
Specifications
TL38 Service & Parts
Page 15
S
PECIFICATIONS
*Specifications are subject to change without notice. Hot weather or heavy use may affect performance.
Refer to the Service Manual for complete parts and service information.
This machine meets or exceeds all applicable CE and GS machinery directive requirements.
ITEM
MANUAL OUTRIGGERS
HYDRAULIC OUTRIGGERS
Duty Cycle
30% of 8 hour cycle
30% of 8 hour cycle
Platform Size
0.7m x 1.3m[2.3ft x 4.3ft] (inside guardrails)
0.7m x 1.3m [2.3ft x 4.3ft] (inside guardrails)
Max. Platform Capacity
215kg [473lbs]
215kg [473lbs]
Max. # of Occupants
2 People
2 People
Height
Maximum Working Height
13.45m [44.1ft]
13.49m [44.3ft]
Maximum Platform Height
11.45m [38ft]
11.49m [38ft]
Min. Platform Height
0.65m [2.1ft]
0.65m [2.1ft]
Max. Working Outreach
6m [19.7ft]
6m [19.7ft]
Travelling Dimensions:
Length
6.08m [19.9ft]
6.08m [19.9ft]
Width
1.53m [5.0ft]
1.53m [5.0ft]
Height
2.00m [6.6ft]
2.00m [6.6ft]
Outrigger Spread
(front-rear x side-side)
(front-rear x side-side)
Max. Clearance
3.40m x 3.42m [11.2ft x 11.2ft]
3.39m x 3.45m [11.1ft x 11.3ft] *
3.46m x 3.56m [11.4ft x 11.7ft]**
Min. Effective Clearance
3.25m x 3.27m [10.7ft x 10.7ft]
3.16m x 3.22m [10.4ft x 10.6ft]*
3.24m x 3.33m [10.6ft x 10.9ft]**
Rotation
370 degrees non-continuous
370 degrees non-continuous
Gross Weight
1468kg [3,237lbs]
1468kg [3,237lbs]
Maximum Towable Speed
83km/h [50mph]***
83km/h [50mph]***
Power Source
24V DC 4HP, 4 X 6V 220Ah Batteries
24V DC 4HP, 4 X 6V 220Ah Batteries
System Voltage
24V DC
24V DC
Battery Charger
24V 25A 220/110VAC 50/60 Hz
24V 25A 220/110VAC 50/60 Hz
Hydraulic TankCapacity
15 Litres [3.9 Gallons US]
15 Litres [3.9 Gallons US]
Max. Hydraulic Pressure
155 Bar [2,250psi]
155 Bar [2,250psi]
Hydraulic Oil
ISO #46
ISO #46
Lift System
2 Double Acting Lift Cylinders With
2 Double Acting Lift Cylinders With
Lock Valves And Manual
Lock Valves And Manual
Emergency Lowering Facility.
Emergency Lowering Facility.
1 Double Acting Lift (Jib) Cylinder
1 Double Acting Lift (Jib) Cylinder
Control System
One handed Proportional Joystick
One handed Proportional Joystick
Operating Energy Efficient Motor
Operating Energy Efficient Motor
Control System.
Control System.
Tyres
185 R13 6PLY
185 R13 6PLY
Brake System
Automatic Reverse & Overrun Brakes
Automatic Reverse & Overrun Brakes
Handbrake
Handbrake
Maximum Continuous Sound
Pressure Level At Operation
Stations
74.6 dB(A)
74.6 dB(A
* Outriggers Deployed at full height = Minimum footprint
** Outriggers Deployed at min. height = Maximum footprint
*** Subject to local regulations
Summary of Contents for TL38
Page 1: ...ERVICE PARTS MANUAL POWERED ACCESS WORK PLATFORM TL38 ...
Page 2: ......
Page 4: ......
Page 51: ...Page 3 28 Maintenance 3 17 Torque Specifications TL38 Service Parts NOTES ...
Page 59: ...Page 5 2 Schematics 5 1 Introduction TL38 Service Parts ...
Page 60: ...Page 5 3 Schematics 5 1 Introduction TL38 Service Parts ...
Page 61: ...Page 5 4 Schematics 5 1 Introduction TL38 Service Parts ...
Page 62: ...Page 5 5 Schematics 5 1 Introduction TL38 Service Parts ...
Page 63: ...Page 5 6 Schematics 5 1 Introduction TL38 Service Parts Notes ...
Page 66: ...Page 6 3 Illustrated Parts Breakdown General Assembly TL38 Service Parts ...
Page 70: ...Page 6 7 Illustrated Parts Breakdown Booms Posts Assembly TL38 Service Parts ...
Page 72: ...Page 6 9 Illustrated Parts Breakdown Platform Assembly TL38 Service Parts ...
Page 84: ...Page 6 21 Illustrated Parts Breakdown Outrigger Cylinder Assembly TL38 Service Parts NOTES ...
Page 86: ...Page 6 23 Illustrated Parts Breakdown Electrical Assembly TL38 Service Parts ...
Page 92: ...Page 6 29 Illustrated Parts Breakdown Decal Assembly TL38 Service Parts ...
Page 94: ...Page 6 31 Illustrated Parts Breakdown Decal Assembly TL38 Service Parts ...
Page 95: ...Page 6 32 Illustrated Parts Breakdown Decal Assembly TL38 Service Parts NOTES ...