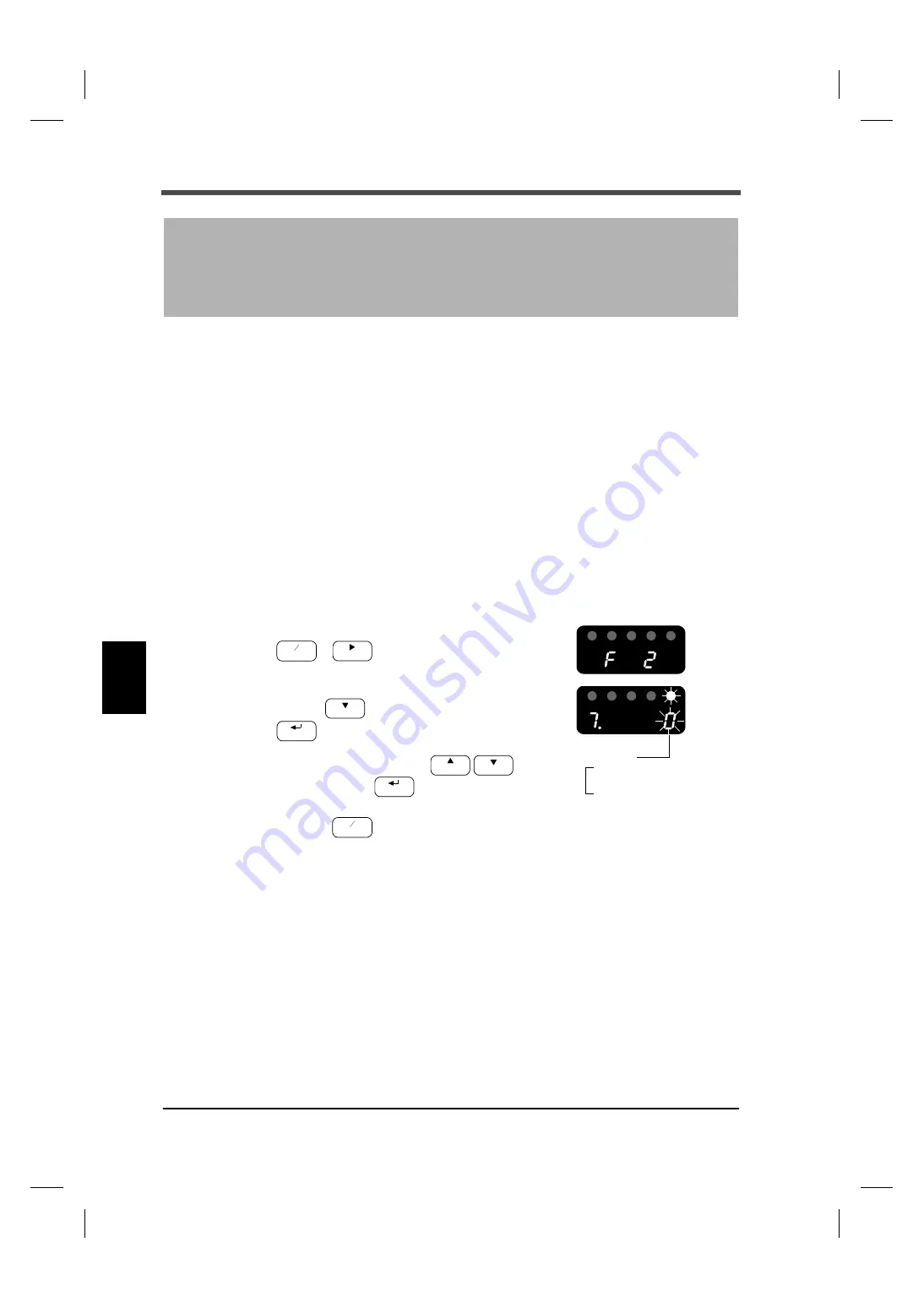
52
7
Settings and Operations Related to Hold
52
Se
tting
s an
d Op
er
ations Related
to
Hold
Chapter
7
7-1.
Hold mode
F325 has a peak hold function that maintains and displays a peak value (maximum value) of input
signals and a sample hold function that maintains and displays an arbitrary point.
When hold fix section is set as 1: ON, detection section and fix section can be distinguished.
* Peak hold can be switched between analog and digital.
Refer to P.59 “7-2.Peak hold selection”.
* Hold value display renewal timing can be changed.
Refer to P.60 “7-4.Renewal timing of hold value”.
* Prohibition time for preventing chattering of HOLD signals can be set.
Refer to P.61 “7-5.Hold detection wait”.
■
Hold mode setting method
1.
Select setting mode 2.
→
2.
Select "hold mode".
Press the
key seven times.
Set the hold mode using the
keys, and
confirm it with the
key.
3.
Press the
key to return to the indicated value display.
7
Settings and Operations
Related to Hold
FNC
+
-
ZERO
1: Peak hold
0: Sample hold
Hold mode
CAL
HOLD
GAIN
CAL
HOLD
FNC
+
-