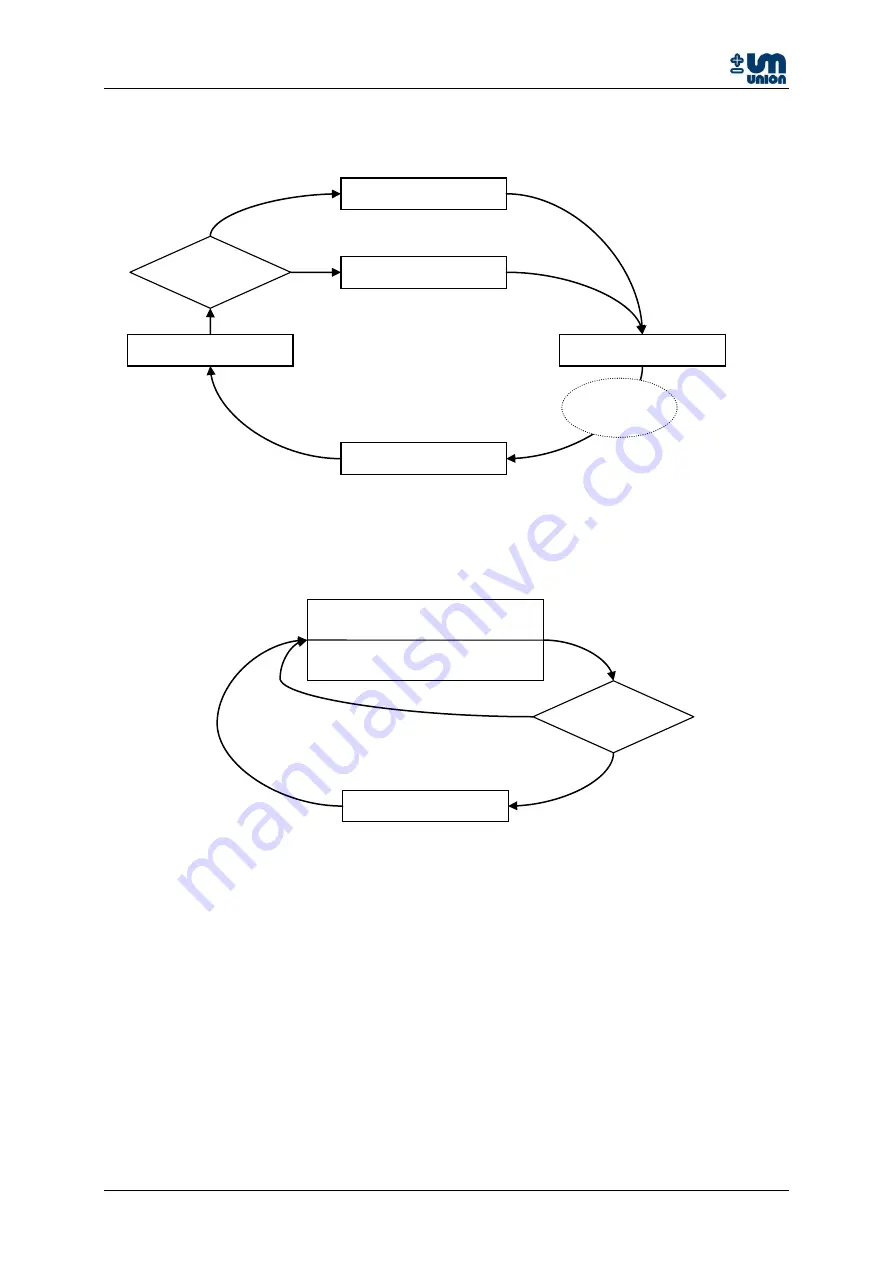
UNION Instruments GmbH
INCA Analyzer Series
– Instruction Manual
General description
Page 11 of 59
3.1.2
Diagrams of the phase transition
Figure 3-1: Phase transition in standard analyzer
Figure 3-2: Phase transition in continuously measuring analyzer
Purge gas
Condensate drain
Change channel
Measurement
Calibration
Check for
Autocalib.
Yes
No
Purge gas
calibration
Measure continuous channels:
(e.g. CO
2
, CH
4
, etc)
Discontinuous channels every 15 minutes:
(e.g. H
2
, H
2
S, O
2
)
Calibration
Check for
Autocalib
Yes
No