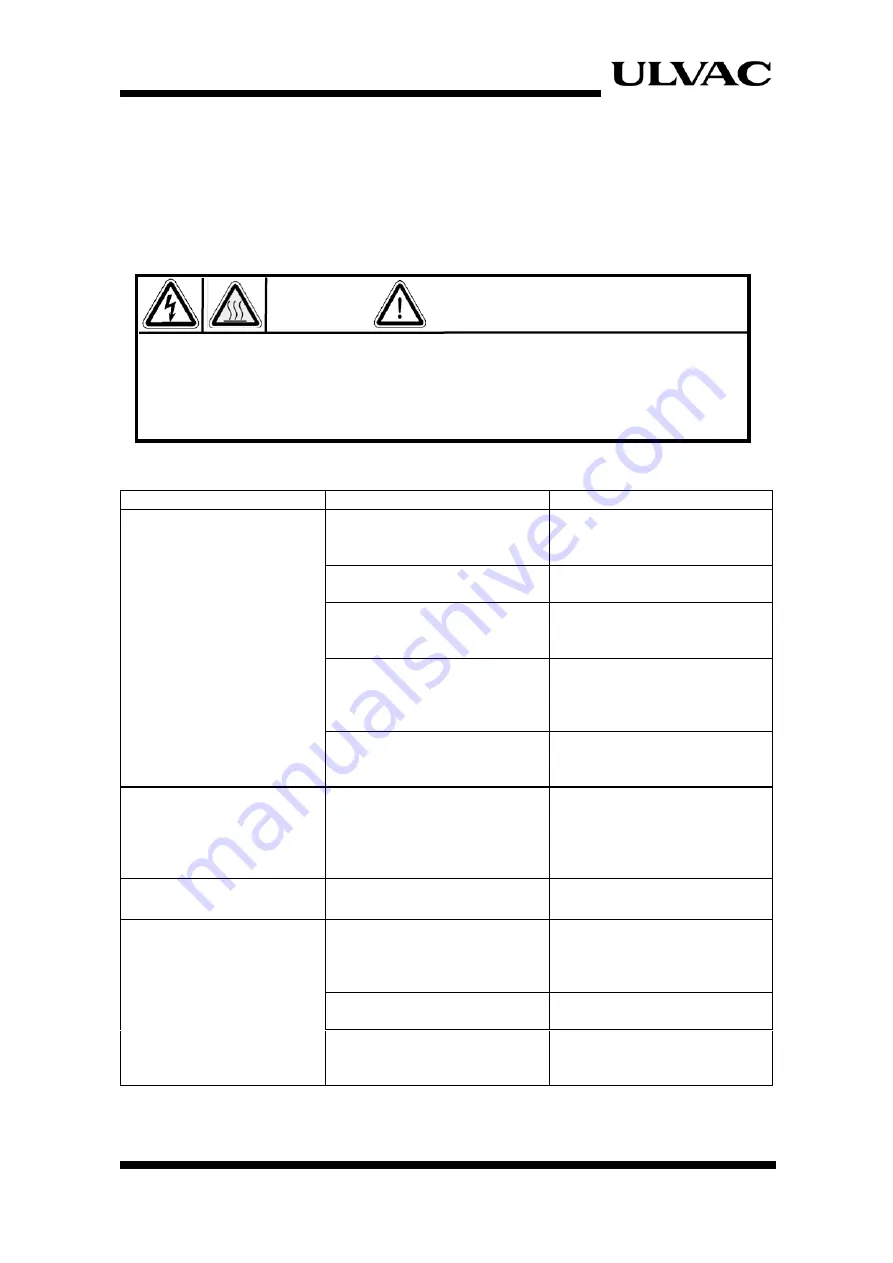
32
ULVAC CRYOGENICS INCORPORATED
13. Troubleshooting
When any failure or unusual phenomenon occurs in the equipment, at first perform
the fault diagnosis shown in the following table. When contacting us, it is
requested to check the lighting status of PLC lamp arranged to the electrical circuit
in advance.
Problem
Possible Cause
Corrective Action
(1) Equipment fails to
start by pressing the
RUN/STOP switch.
(The RUN/STOP
switch does not light)
The main power source
(breaker) is turned OFF.
Turn ON the main power
source.
The power cord is not
connected.
Connect the power cord
correctly.
The circuit breaker is turned
OFF.
Turn ON the circuit breaker.
The fuse is blown.
Replace fuse with new one.
If the fuse is blown
repeatedly, please contact
us.
The emergency stop button is
pressed.
Reset the emergency stop
switch by turning it to the
right, and restart.
(2) Equipment fails to
start even if the
RUN/STOP switch
lights up.
LN
2
level is not decreased to
the re-starting level.
When LN
2
level is decreased
to 75% or less, the
production starts
automatically.
(3) Power breaker trips.
Short-circuit or electric
leakages occur.
Please contact us.
(4) GN2 AL. lights on.
The RUN/STOP lamp
flickers at the same
time.
GN10i is suspended.
Check the electric wiring of
GN-10i, or
Suspend and resume EMP
and GN-10i.
IM-120 is suspended.
Check the dry air supply
pressure.
Nitrogen gas supply
decreases, or the pressure is
lowered temporarily.
Refer to “9-5-3. Corrective
action when GN2 AL. occurs”
and restart EMP 14A.
Ensure that main power is disconnected before inspecting the power source or
inside of the equipment. Some parts of the equipment may remain in high
temperature right after stopping operation. Use caution to avoid burn injury.
WARNING