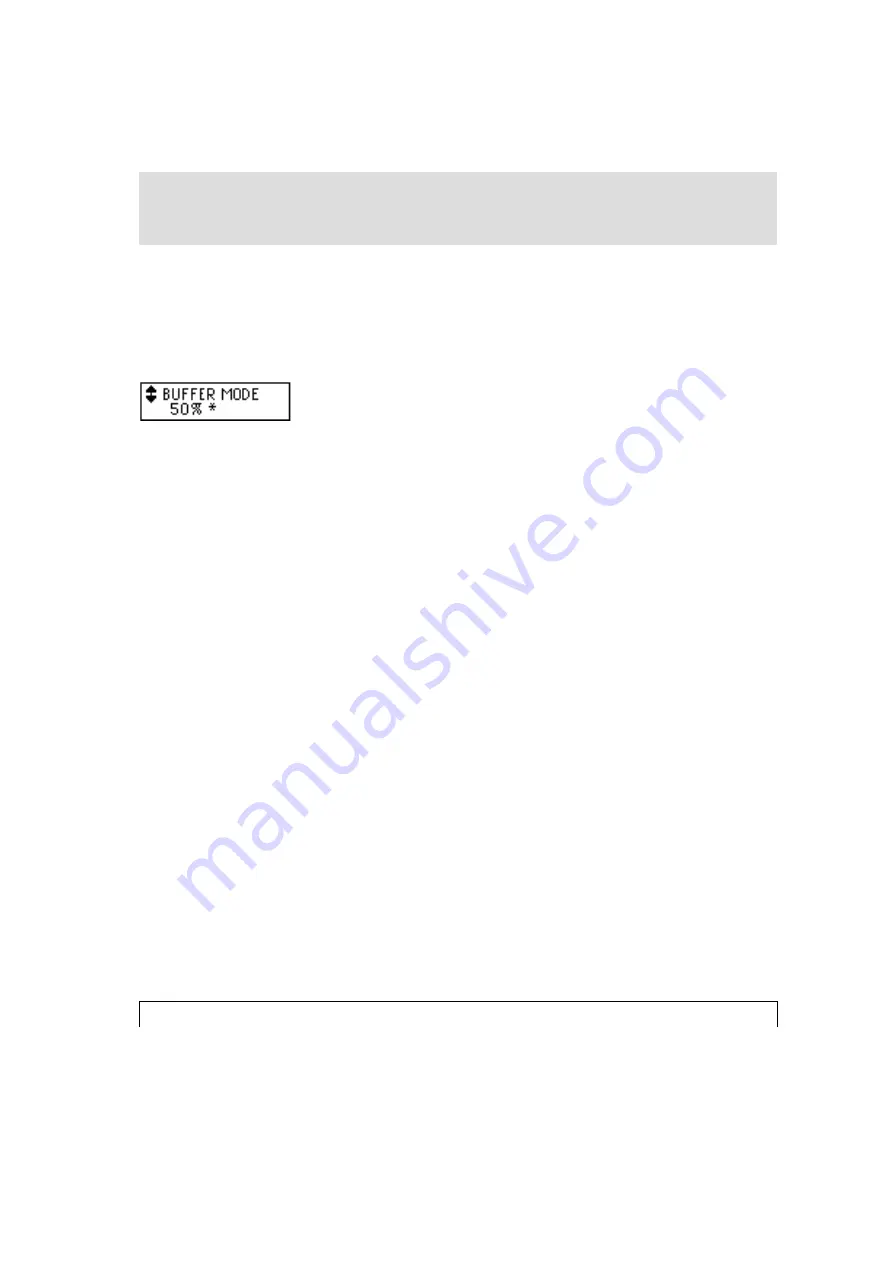
Ultre 5400 - User Manual
5-9
Changing Default Settings - 5
■
Buffer Mode
The Ultre 5400 Imagesetter is configured with a large buffer memory (16 to
32MB). This function is used to determine the minimum amount of data that
will be buffered before imaging begins.
The value can be varied to eliminate delays in imaging jobs. Setting the value
low will initiate imaging more quickly but if it is set too low the job may abort
if the RIP is not able to maintain the necessary data transfer rate on complex
jobs.
1. Depress Menu Button and the UP or DOWN Arrow Buttons until the BUFFER
MODE function is displayed.
2. Depress either the LEFT Arrow Button or the RIGHT Arrow Button until the
desired buffer fill percentage is displayed on the LCD.
3. Depress the Enter Button. Depress the Menu Button to return to the Machine
Status Display.
■
Program Revision
This message displays the current revision of the machine firmware