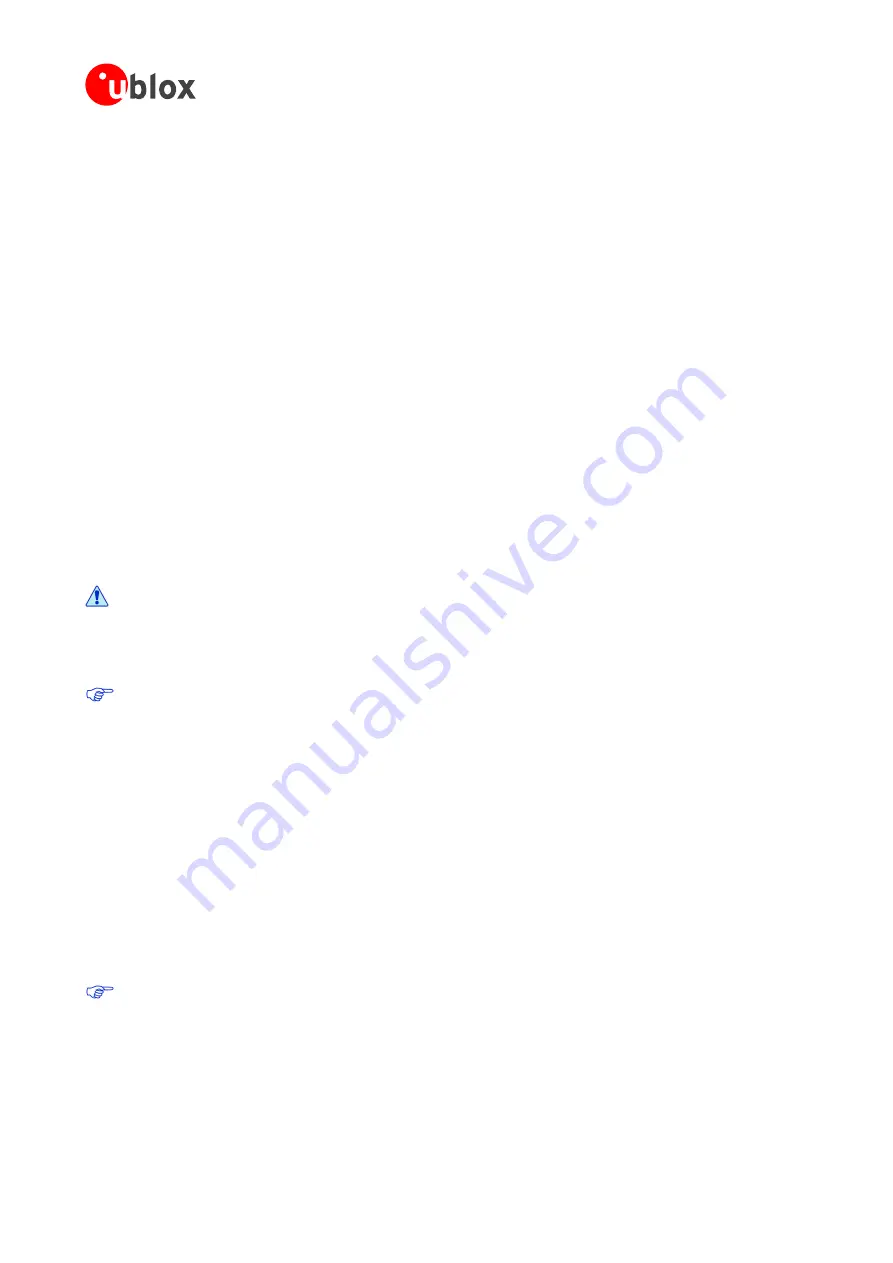
TIM-5H
-
Hardware
Integration
Manual
Product
Handling
GPS.G5-MS5-07015-A-1
u-blox
proprietary
Page 32
your position is our focus
3.3 Processing
3.3.1 Moisture Preconditioning
Both
encapsulant
and
substrate
materials
absorb
moisture.
JEDEC
specification
J-STD-020
must
be
observed
to
prevent
cracking
and
delamination
associated
with
the
"popcorn"
effect
during
solder
reflow.
The
popcorn
effect
can
be
described
as
miniature
explosions
of
evaporating
moisture.
Baking
before
processing
is
required
in
following
cases:
•
Humidity
indicator
card:
At
least
one
circular
indicator
is
no
longer
blue
•
Floor
life
or
environmental
requirements
after
opening
the
seal
is
opened
has
been
exceeded,
e.g.
exposure
to
excessive
seasonal
humidity.
Recommended baking procedure:
Duration:
48
hours
Temperature:
125°C
Humidity:
Below
5%.
Desiccant
must
be
placed
into
the
oven
to
keep
humidity
low.
Oven:
Convection
flow
oven.
Also
put
desiccant
pack
into
the
oven
for
dehydration.
After
work:
Put
the
baked
components
with
desiccant
and
moisture
indicator
into
a
humidity
proof
bag
and
use
a
vacuum
hot
barrier
sealing
machine
for
sealing
if
not
processed
within
specified
floor
time.
Storage
in
a
nitrogen
cabinet
or
dry
box
is
also
a
possible
approach
to
prevent
moisture
intake.
Do not attempt to bake TIM-5H modules contained in tape and rolled up in reels. If necessary,
bake the TIM-5H modules quickly at 125°C for 48 hours, remove them from the belt and place
them individually onto the oven tray.
A
repeated
baking
process
will
reduce
the
wetting
effectiveness
of
the
pad
contacts.
This
applies
to
all
SMT
devices.
3.3.2 Soldering Paste
Use
of
"No
Clean"
soldering
paste
is
strongly
recommended,
as
it
does
not
require
cleaning
after
the
soldering
process
has
taken
place.
The
paste
listed
in
the
example
below
meets
these
criteria.
Soldering
Paste:
LFSOLDER
TLF-206-93F
(Tamura
Kaken
(UK)
Ltd.)
Alloy
specification:
Sn
95.5/
Ag
3.9/
Cu
0.6
(95.5%
Zinc/
0.6
%
Silver/
0.6%
Copper)
Melting
Temperature:
216
-
221°C
Stencil
Thickness:
150
μ
m
for
base
boards
The
final
choice
of
the
soldering
paste
depends
on
the
approved
manufacturing
procedures.
The
paste-mask
geometry
for
applying
soldering
paste
should
meet
the
recommendations
in
section
The
quality
of
the
solder
joints
on
the
connectors
(’half
vias’)
should
meet
the
appropriate
IPC
specification.