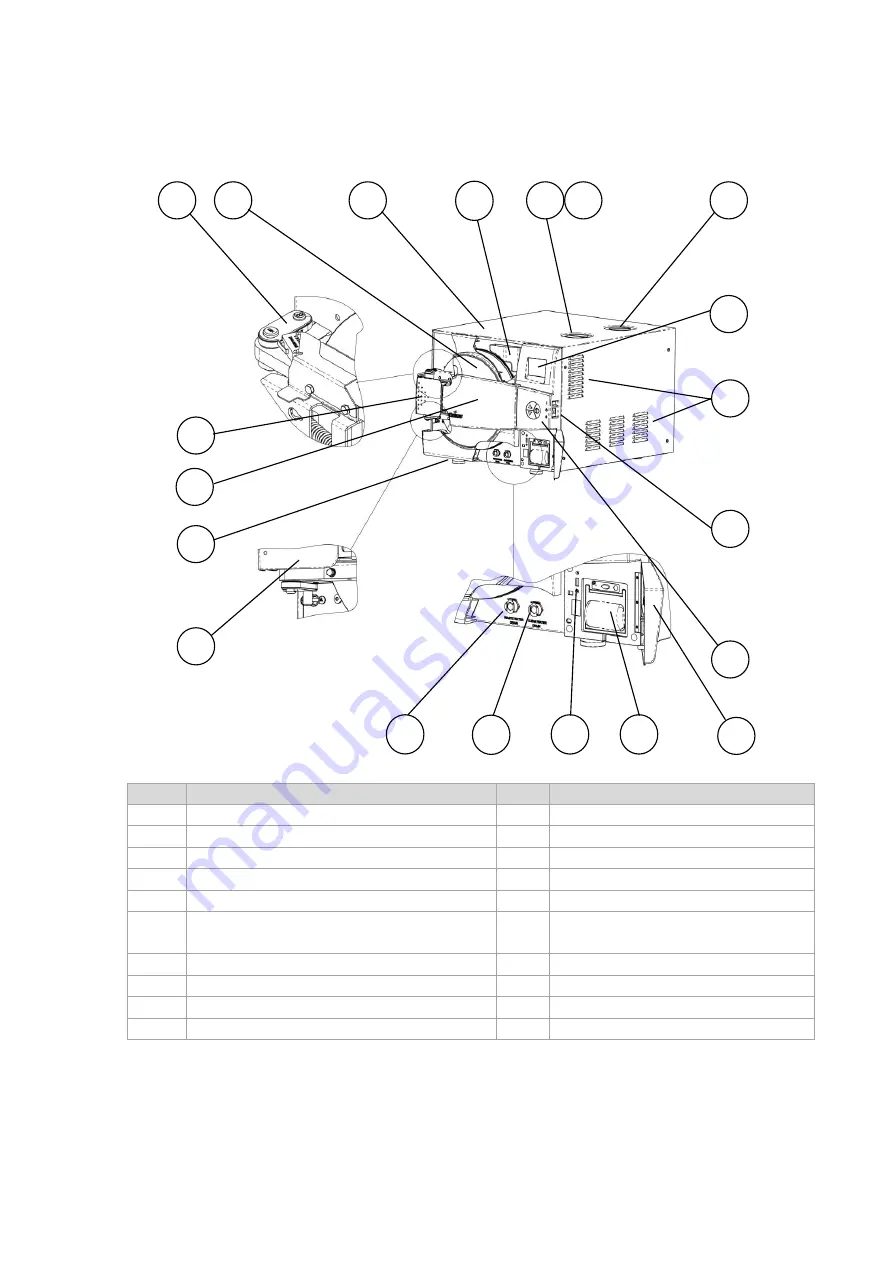
Page 12
1.12.
Front View
No.
Description
No.
Description
1
Door microswitches
10
Keypad
2
Autoclave door
11
Printer cover
3
Autoclave outer cover
12
Door opening grip
4
Mineral-free water reservoir
13
Plastic door cover
4a
Water reservoir fill and level gauge
5
Chamber and steam generator
safety valves (inside the reservoir)
14
Autoclave Leg
6
Wastewater reservoir
15
Wastewater drain
7
Display
16
Clean water drain
8
Ventilation grill
17
USB port
9
On/off switch / circuit breaker
18
Printer (standard)
5
4
6
8
9
10
11
14
1
2
3
7
16
15
17
18
12
13
1
4a