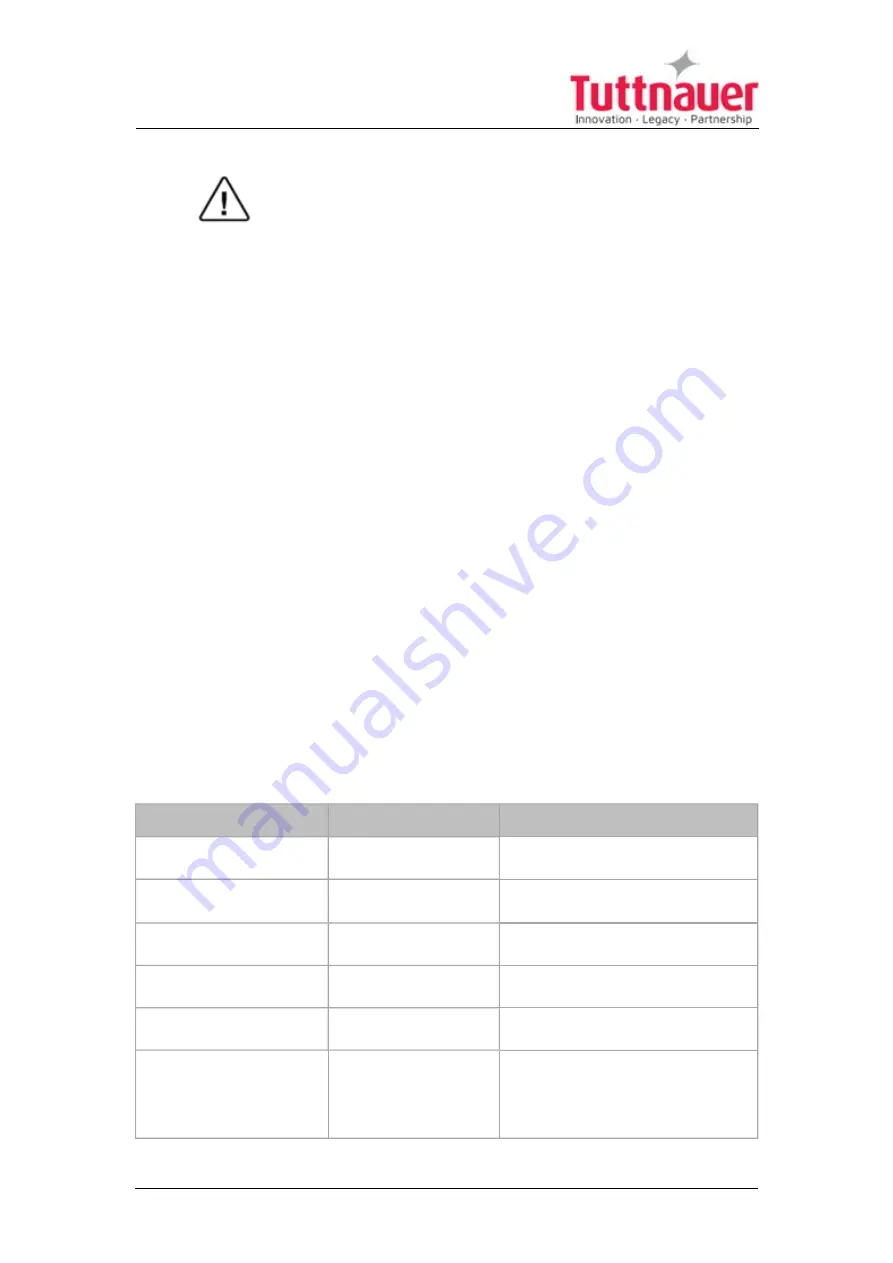
Caution!
In
order
to
avoid
any
injury
by
electrical
hazard,
it
is
recommended that a ground fault protection device (GFCI) be
installed in the electrical panel feeding the autoclave (local codes
may make this mandatory).
The electrical network must comply with local rules and
regulations.
Verify that there is an easy access to the main power switch and
to the current leakage safety relay (GFCI). The voltage supplied to
the device must comply with the label ± 10%.
1.11 Device Environmental Information
l
The peak sound level generated by the autoclave is 67dBa with
background noise of 48dBa during sterilization stage, and 65dBa during
drying stage.
l
The total heat per hour transmitted by the autoclave is <200Wh.
1.12 Requirements with concern to Water Quality
The distilled or mineral-free water supply to the autoclave shall be according to
the table below:
Suggested Maximum Limits of Contaminants in Water for Steam
Sterilization per EN13060
Table 5 - Water Quality
Substance
Feed Water
Condensate
Evaporate residue
≤ 10 mg/l
≤ 1.0 mg/l
SiO
2
≤ 1 mg/l
≤ 0.1 mg/l
Iron
≤ 0.2mg/l
≤ 0.1mg/l
Cadmium
≤ 0.005 mg/l
≤ 0.005 mg/l
Lead
≤ 0.05 mg/l
≤ 0.05 mg/l
Rest of heavy metals
except iron,
cadmium, lead
≤ 0.1 mg/l
≤ 0.1 mg/l
Page 13
Summary of Contents for AMS11-120-T
Page 2: ......
Page 4: ...https www tuttnauerusa com...
Page 16: ...1 10 Device Specifications 1 10 1 Overall Dimensions Page 9...
Page 56: ...Note For the results of the cycle see description in section 8 5 Page 49...
Page 67: ...Press to receive the entire printout of the selected cycle history Page 60...
Page 86: ...Page 79...