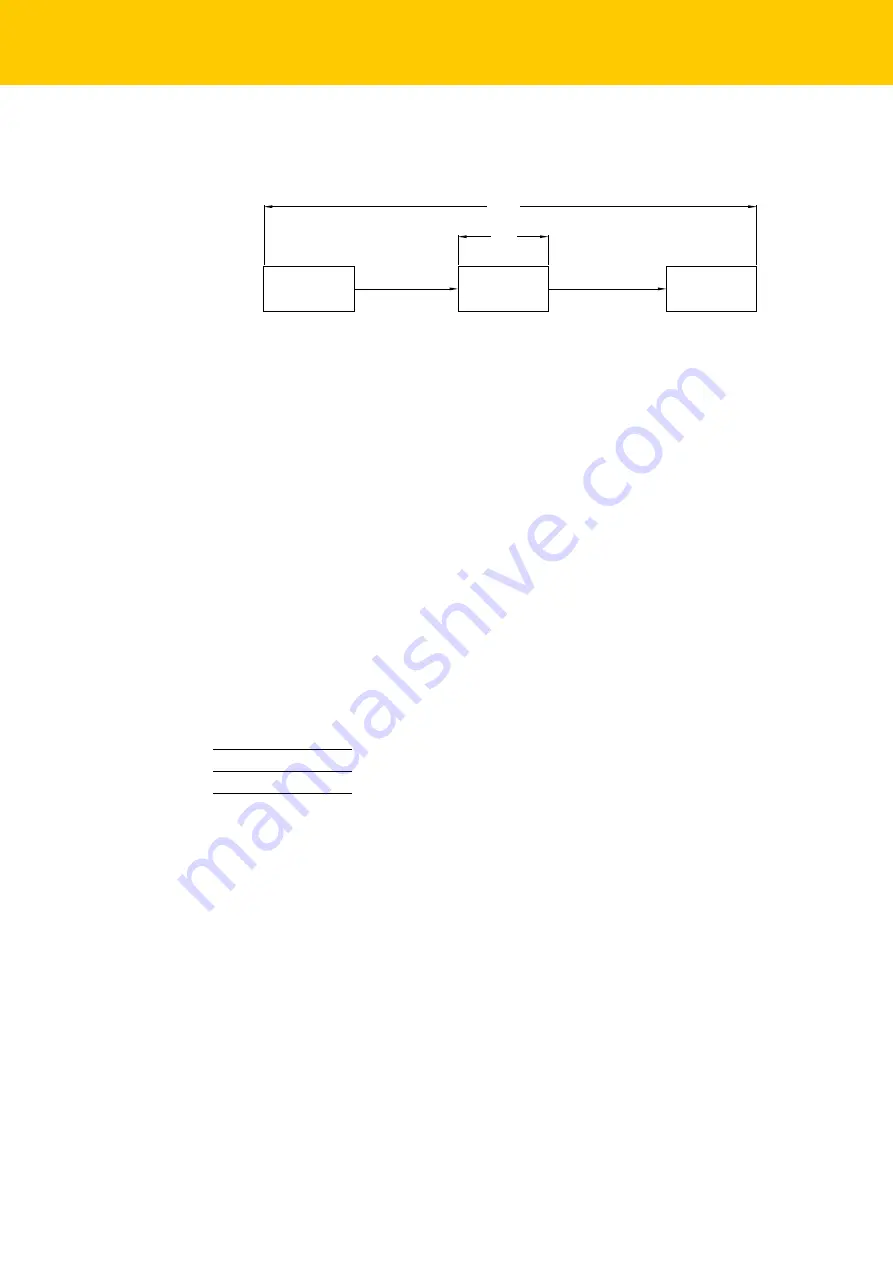
8
Hans Turck GmbH & Co. KG | T +49 208 4952-0 | F +49 208 4952-264 | [email protected] | www.turck.com
Safety-Planning
10%
100%
IM
Actuator
Sensor
This means that the failure limit value must be less than
10
-3
.
The basis of the consideration is a test interval of 8760 h and an MTTR or MRT of 24 h.
5
Safety-Planning
Planning a safety-related loop
This chapter provides information for planning a safety-related loop.
The device is not specified for a certain application. Make sure that the data provided in this
chapter is valid for your target application.
Special application-specific factors may cause the premature wear of the device and must be
taken into consideration when planning systems; take special measures to compensate for a
lack of experience based values, e.g. through implementation of shorter test intervals.
The suitability for specific applications must be assessed by considering the particular overall
safety-related system with regard to the requirements of IEC 61508.
Safety-planning must only be carried out by trained and qualified personnel.
If there is any doubt contact Turck directly.
5.1
Architectural specificatons
Due to architectural considerations the following characteristics are specified:
Type
A
HFT
0
Useful lifetime:
Experience has shown that the useful lifetime often lies within a range of 8 to 12 years. It can
be significantly less if elements are operated near their specification limits. However, it can
be extended by appropriate measures. For example, heavy temperature fluctuations could
potentially decrease the useful lifetime, as constant temperature below 40 °C could potentially
increase the useful lifetime.
5.2
Assumptions
■
Failure rates are constant for 10 years, wear out mechanisms are not included
■
Propagation of failures are not relevant
■
External power supply failure rates are not included
■
All components that are not part of the safety function and cannot influence the safety
function (feedback immune) are excluded.
■
The activations of line-monitoring can improve the results