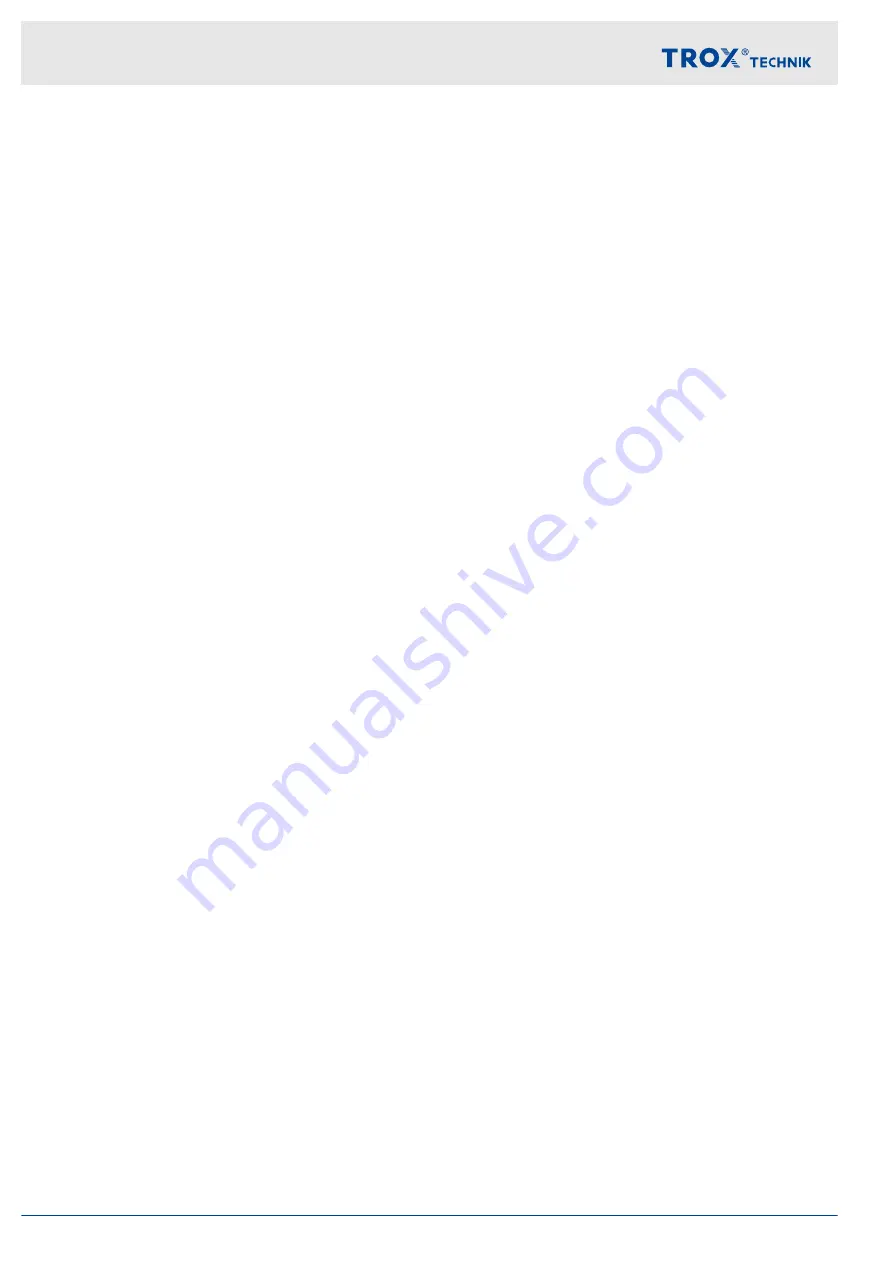
8
Troubleshooting
Check the installation situation
Accessibility to the VAV terminal unit and the control
component sufficient?
Specified airflow direction maintained?
4.4 ‘Direction of airflow’ on page 15
Required upstream section maintained?
4.5 ‘Upstream conditions’ on page 16
Installation orientation of control component main-
tained, depending on transmitter type of control
component (observe installation orientation sticker
Differential pressure measuring hoses undamaged
and kink-free?
Only for VAV terminal units for differential pressure con-
trol
Selection of a suitable pressure measuring point
Selection of a suitable pressure reference as com-
parison value (reference room with stable pressure
conditions, with a constant atmospheric pressure)
Select the measuring range of the pressure trans-
ducer with sufficient reserve. The measuring range
must allow the detection of the setpoint pressure
range plus an appropriate tolerance.
The following applies in particular to room pressure
control systems:
–
Sufficient cross section of the pressure meas-
uring tubing, in particular when using ring ducts
for the reference pressure
–
The pressure-controlled rooms must be suffi-
ciently airtight to be able to build up the desired
room pressure.
–
The pressure-controlled rooms must allow air
transfer flow so that the room pressure can be
regulated. (At least 10% of the total room extract
air to air transfer flow.)
–
All doors and seals must be installed and holes
must be closed in the walls in order to commis-
sion the rooms that are to be controlled.
Check system readiness
Fan switched on?
Sufficient pre charge pressure available at the VAV
terminal unit, i.e. minimum differential pressure com-
plied with in accordance with the data sheet?
Fire dampers/shut-off devices opened in the duct
section?
Check control component (for additional details, see
commissioning instructions for control components)
Error-free wiring and supply voltage within tolerance
zone?
Characteristic curve of the setpoint value control
input signal suitable for the control component or its
parameterisation?
Zero point correction performed on control compo-
nents with static transducer?
If necessary, adapt the actuators again (only
required for certain control components)
Check control operation
Setpoint control within the control range of the VAV
terminal unit and its control component.
Check operating point at Vmin; if necessary, tempo-
rarily disconnect external setpoint setting to prevent
influence of external control input signal and only
check the controller itself at operating point Vmin.
Check the operating point at Vmax; check the direc-
tion of rotation of the damper blade in each case.
Check damper blade position relative to the setpoint
value; if the damper blade is fully open, the setpoint
value is not reached. This is an indicator for an inad-
equate differential pressure. Detection of the
damper blade position,
.
Room situation (pressure conditions and air
transfer behaviour)
The overall situation in the room depends on many fac-
tors, in particular:
Supply air volume flow rates and their tolerance
zone
Extract air volume flow rates and their tolerance
zone
Tightness of the room or size of air transfer open-
ings – type of control components used (control
speed) and their control input signal
Type of the selected leading control concept, control
based on volume flow rate or pressure
Note: The planning concept – and not the individual VAV
terminal unit – is decisive for achieving compliance with
the desired room situation. Even if the technical data of
the installed volume flow controller is complied with, the
desired room situation can only be achieved if the nec-
essary components have been selected during the plan-
ning phase, taking into account the requirements.
Troubleshooting
VAV terminal units VARYCONTROL
28