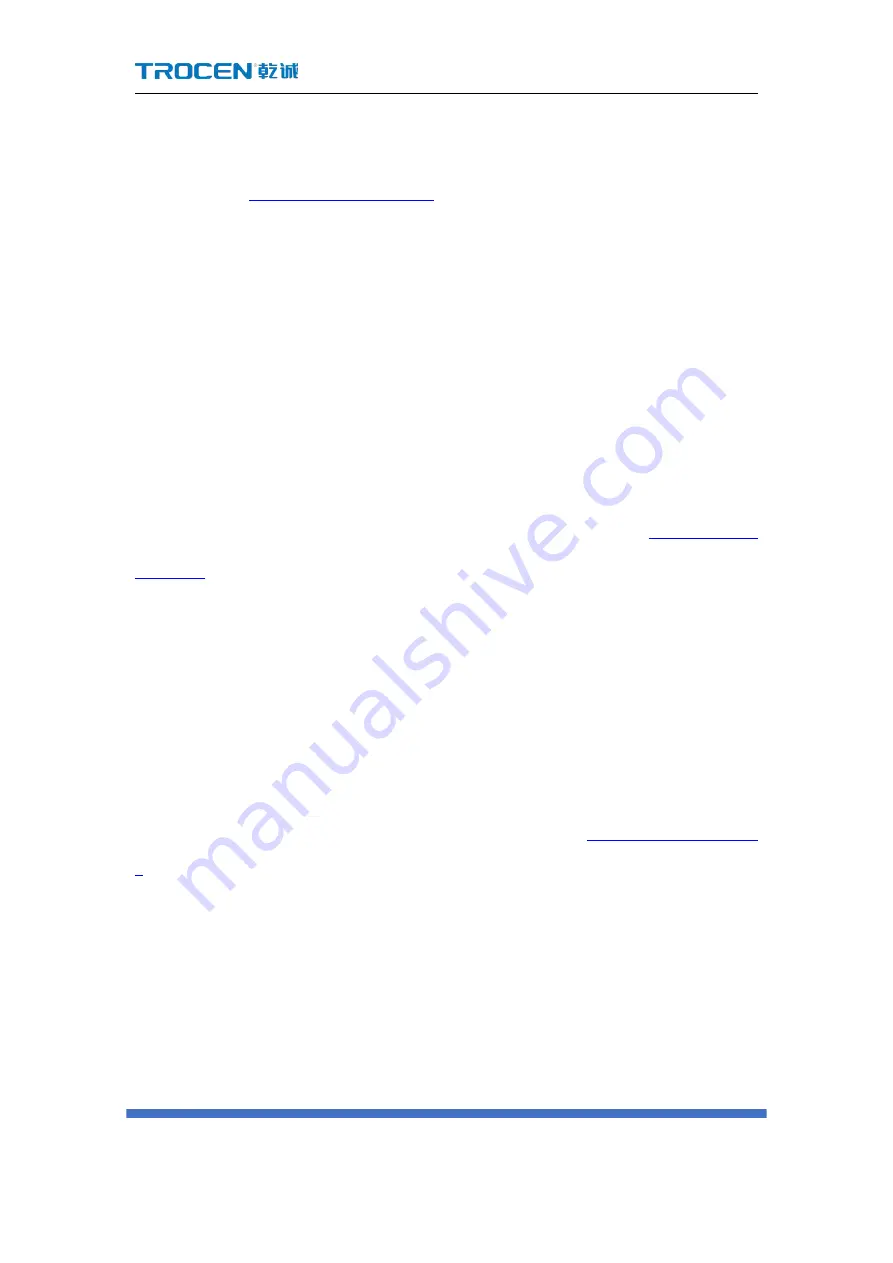
AWC7813 motion controller user manual
WWW.SZTROCEN.COM
47
3.13.1 Set origin coordinates
1) In the
interface, click
【
Menu
】→【
origin manage
】
→【
origin 1
】
;
2) If you know the coordinate value of a certain origin, directly enter the value
key after XY, and then click
【
Set Current position as the origin
】
to set it;
3) If the coordinate value of the origin is not clear, click the right direction
button to move the laser head to the desired origin and then click
【
Move
head to the origin
】
to set it, and the other three origin are the same.
3.13.2 Move the laser head to the set origin
When the laser head position is not at the required origin
,
in the
interface 2
interface, click
【
Menu
】→【
origin manage
】→【
origin 1
】→【
Move head
to the origin
】
to set it.
3.14 Motion Parameters Settings
【
Motion parameters
】
are restricted by
【
Axis Parameters
】
in
【
Manufacturer
Parameters Settings
】
. If the user encounters a situation where the
【
Motion
Parameters
】
cannot be adjusted, you need to adjust the
【
Axis Parameters
】
first,
such as
【
Start Speed
】
,
【
Max Speed
】
,
【
Max Acc
】
. In the
2
interface, click
【
Menu
】→【
Motion parameters Settings
】
then enter the motion
parameters settings interface.