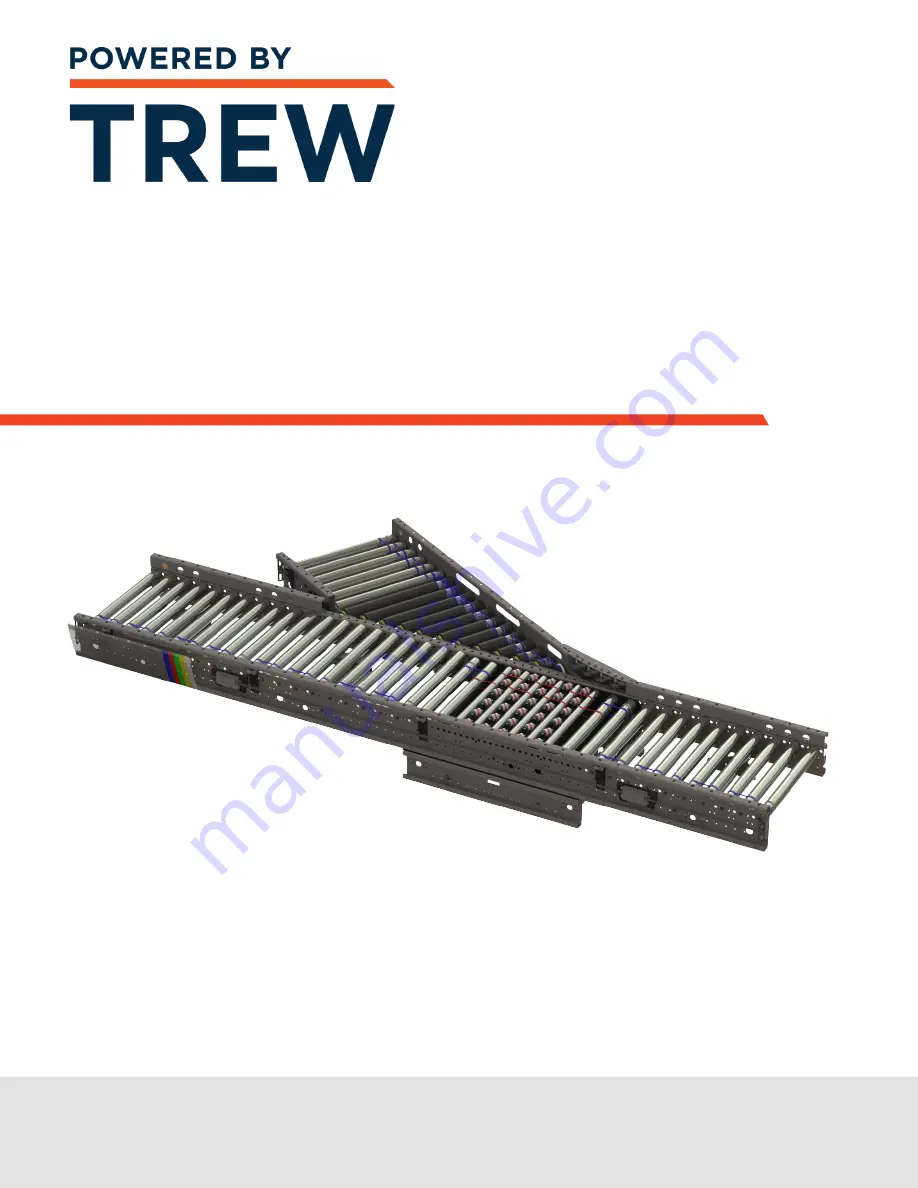
SERIES 1500
24VDC MOTORIZED DRIVER ROLLER
HCAT30 POP-UP DIVERT SECTION
INSTALLATION &
MAINTENANCE MANUAL
1.800.571.8739 poweredbyTREW.com [email protected]
SERIES 1500
24VDC MOTORIZED DRIVER ROLLER
HCAT30 POP-UP DIVERT SECTION
INSTALLATION &
MAINTENANCE MANUAL
1.800.571.8739 poweredbyTREW.com [email protected]