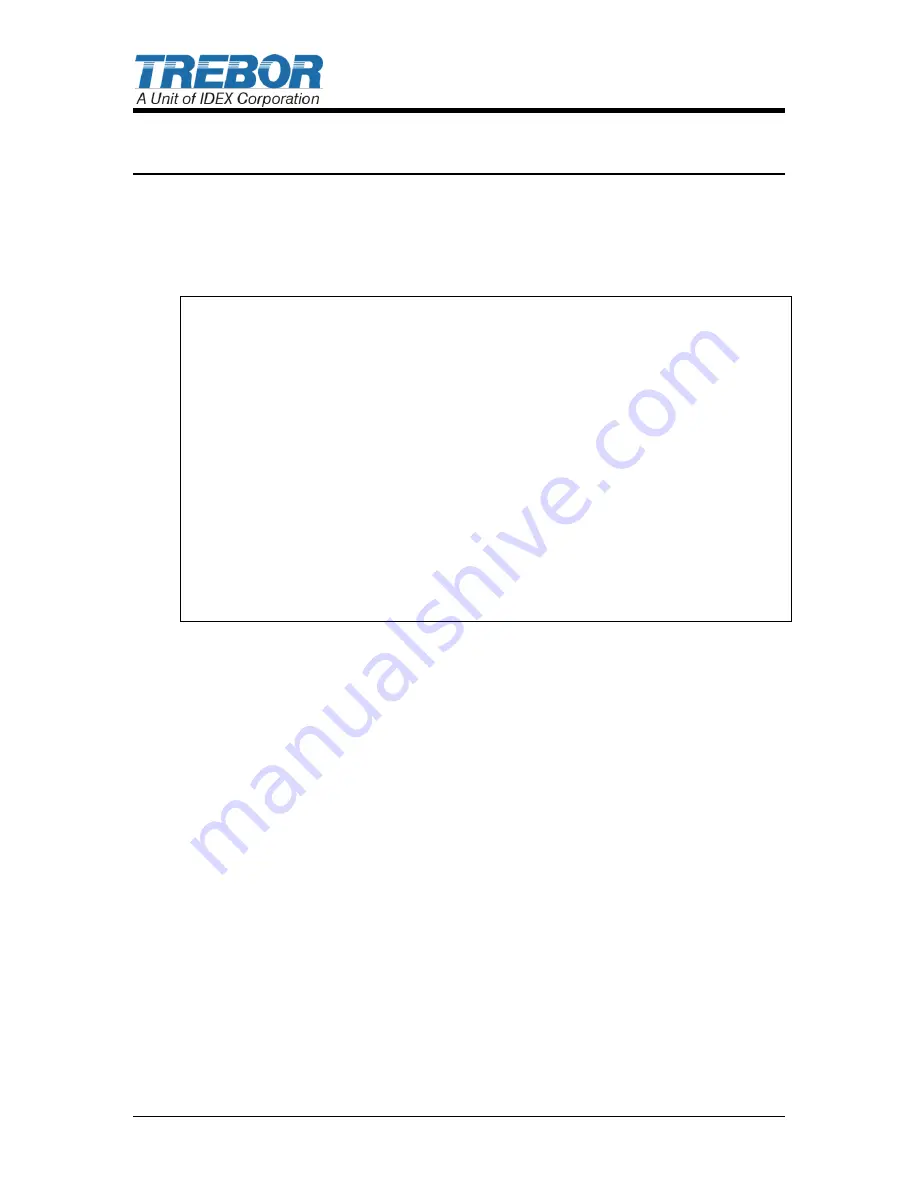
PAGE 10
MAGNUM 610R PUMP OPERATION / MAINTENANCE MANUAL
4
MAINTENANCE
Trebor pump maintenance can be divided into two categories: air system
maintenance and fluid system maintenance. The purpose of air system
maintenance is to prevent air system failures such as stalling or erratic cycling.
The purpose of fluid system maintenance is to maintain suction and lift
capabilities.
Pump Rebuild Service
Trebor International provides a factory rebuild service for customers using Trebor
products. Trebor will rebuild any standard pump (exclusive of options). Please
contact Trebor International Sales Department for current rebuild pricing. The
fixed rebuild price includes a factory rebuild and parts equivalent to the standard
rebuild kit. Each factory rebuild comes with a new one-year warranty. Repairs
requiring more extensive part replacements will be quoted prior to proceeding
with the pump rebuild. If the pump has exceeded its useful life and cannot be
rebuilt, the customer may elect to purchase a new Trebor pump. If the customer
chooses not to rebuild or replace the pump, a $150.00 evaluation charge will be
required.
All returned pumps are to be shipped freight prepaid with a valid Purchase Order
for the cost of rebuild service. Please contact Trebor International prior to
returning your pump to obtain an RMA Number and Pump Return Data Sheet to
ensure proper safety precautions. Each pump will be evaluated and repaired
within 5 working days of the receipt of pump at Trebor facility.
4.1 PREVENTIVE MAINTENANCE SCHEDULE
The following maintenance schedule is recommended to optimize pump
performance and minimize failures. Tie bolt torque should be checked within 30
days of start-up and at periodic intervals thereafter. If the pump is subjected to
thermal cycle operation, the tie bolt torque should be checked after the first 3
thermal cycles and periodically thereafter. Certain operating conditions that
require more frequent maintenance intervals have been noted. In positive
pressure inlet conditions where suction or lift is not required, fluid system
maintenance may be extended. However, tie bolt retorque is still recommended.
Adhering to the recommended preventative maintenance schedule along with
periodic inspection of the pump will ensure continued efficient operation and
overall reliable pump performance.
It is recommended that the Preventive Maintenance Record (Section 4.1.a) be
copied, maintained and kept with this unit for future reference.