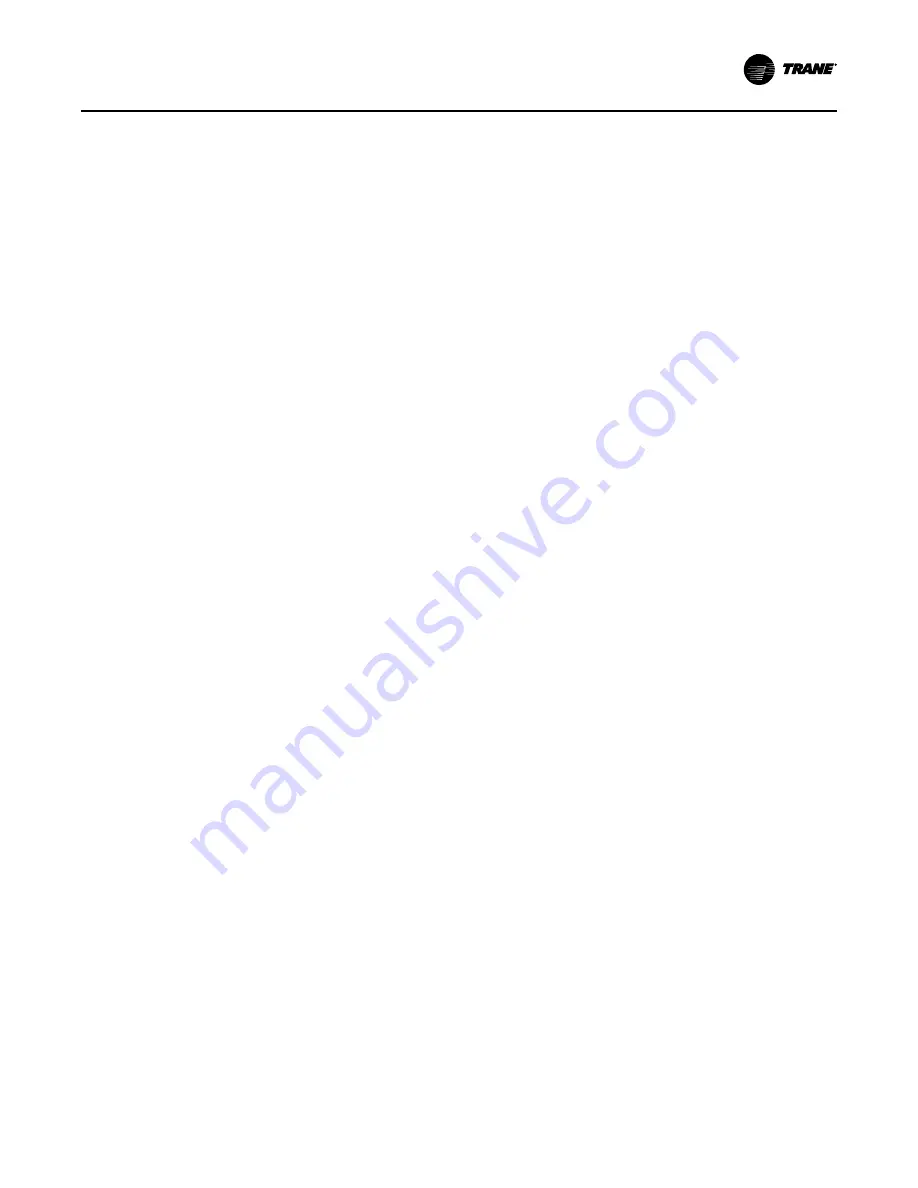
RT-SVX072A-EN
33
☐
Remove the shipping hardware from each
compressor assembly.
☐
Remove the shipping hold-down bolts and shipping
channels from the supply and relief /return fans
with rubber or spring isolators.
☐
Check all supply and relief/return fan spring
isolators for proper adjustment.
☐
Verify that all plastic coverings are removed from
the compressors.
☐
Verify all discharge line service valves (one per
circuit) are back seated.
Main Electrical Power
☐
Verify that the power supply complies with the unit
nameplate specifications. Refer to Main Unit Power
Wiring in the Installation chapter.
☐
Inspect all control panel components; tighten any
loose connections.
☐
Connect properly sized and protected power supply
wiring to a field-supplied/installed disconnect and
unit
☐
Properly ground the unit.
☐
All field-installed wiring must comply with NEC and
applicable local codes.
Field Installed Control Wiring
☐
Complete the field wiring connections for the
variable air volume controls as applicable.
N
No
otte
e:: All field-installed wiring must comply with NEC
and applicable local codes.
Electric Heat Units
☐
Verify that the power supply complies with the
electric heater specifications on the unit and heater
nameplate.
☐
Inspect the heater junction box and control panel;
tighten any loose connections.
☐
Check electric heat circuits for continuity.
☐
On SEH_L units with 200V or 230V electric heat
(requires separate power supply to heater) —
Connect properly sized and protected power supply
wiring for the electric heat from a dedicated, field-
supplied/installed disconnect to terminal block
3XD5, or to an optional unit-mounted disconnect
switch 3QB4.
Gas Heat (SFH_)
☐
Gas supply line properly sized and connected to the
unit gas train.
☐
All gas piping joints properly sealed.
☐
Drip leg installed in the gas piping near the unit.
☐
Gas piping leak checked with a soap solution. If
piping connections to the unit are complete, do not
pressurize piping in excess of 0.50 psig or 14 inches
w.c. to prevent component failure.
☐
Main supply gas pressure adequate.
☐
Flue Tubes clear of any obstructions.
☐
Factory-supplied flue assembly installed on the
unit.
☐
LP (Propane) kit parts installed (if required).
☐
Connect the 3/4" CPVC furnace drain stubout to a
proper condensate drain. Provide heat tape or
insulation for condensate drain as needed.
Hot Water Heat (SLH_)
☐
Route properly sized water piping through the base
of the unit into the heating section.
☐
Install the factory-supplied, 3-way modulating
valve.
☐
Complete the valve actuator wiring.
Steam Heat (SSH_)
☐
Install an automatic air vent at the top of the return
water coil header.
☐
Route properly sized steam piping through the base
of the unit into the heating section.
☐
Install the factory-supplied, 2-way modulating valve
☐
Complete the valve actuator wiring.
☐
Install 1/2", 15-degree swing-check vacuum breaker
(s) at the top of each coil section. Vent breaker(s) to
the atmosphere or merge with return main at
discharge side of steam trap.
☐
Position the steam trap discharge at least 12" below
the outlet connection on the coil.
☐
Use float and thermostatic traps in the system, as
required by the application.
O/A Pressure Sensor and Tubing
Installation
(All units with Statitrac or return fans)
☐
O/A pressure sensor mounted to the roof bracket.
☐
Factory supplied pneumatic tubing installed
between the O/A pressure sensor and the connector
on the vertical support.
☐
Field supplied pneumatic tubing connected to the
proper fitting on the space pressure transducer
located in the filter section, and the other end
routed to a suitable sensing location within the
controlled space (Statitrac only).
Modulating Reheat (S_H_)
☐
Install space humidity and temperature sensors.
Refer to unit diagrams for guidelines.
Summary of Contents for IntelliPak 1
Page 161: ...RT SVX072A EN 161 N No ot te es s ...
Page 162: ...162 RT SVX072A EN N No ot te es s ...
Page 163: ...RT SVX072A EN 163 N No ot te es s ...