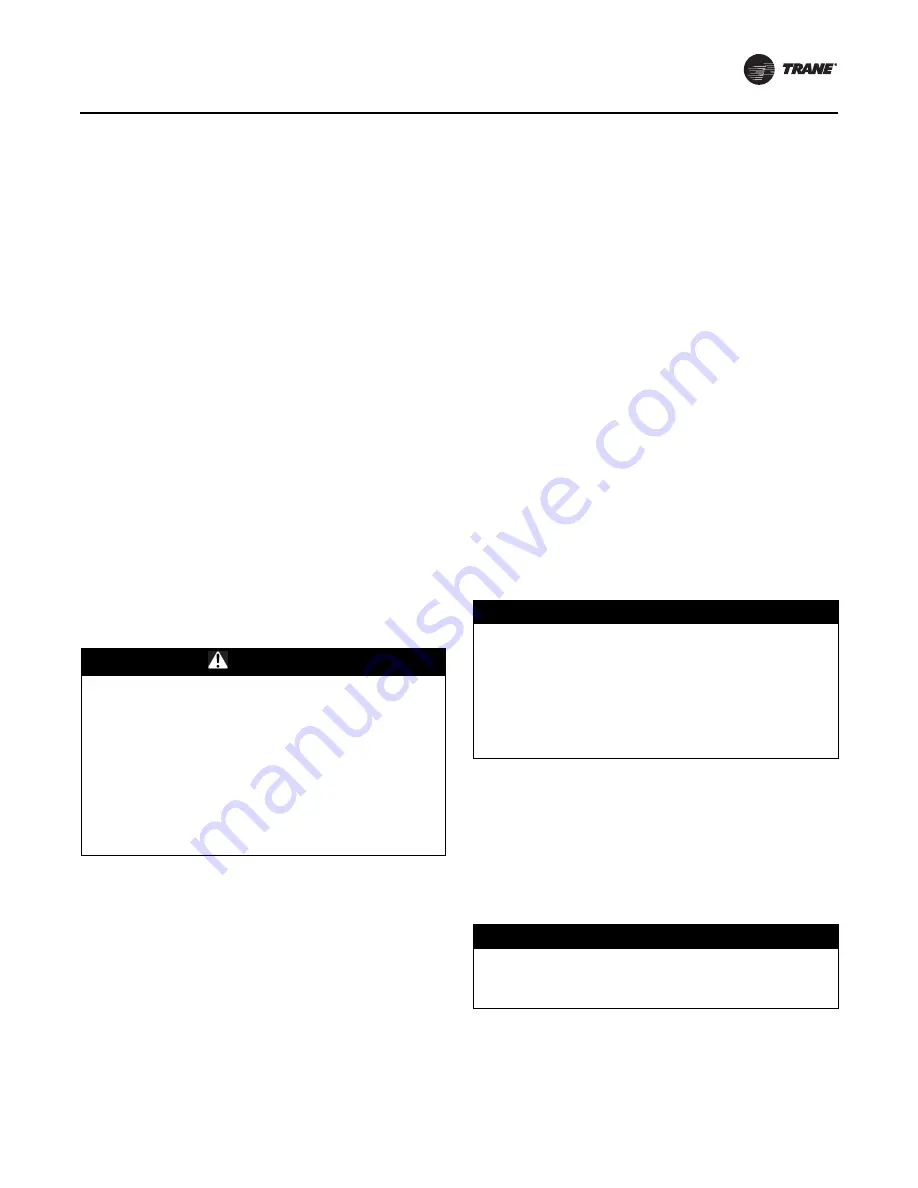
Installation
SS-SVX002B-EN
33
down to 500 microns or less. Close the vacuum pump
isolation valve and pressurize the system again with
dry nitrogen and allow the system to stand for two
hours as in step #5.
7. After two hours release the pressure. Turn on the
vacuum pump and complete the process of evacuating
the system, this time with a goal of achieving a 250
micron vacuum or less. Close the vacuum pump
isolation valve. When you can hold the vacuum at 500
microns or lower for at least 2 hours with no significant
rise in pressure, the system is ready to charge.
8. Replace the Schrader valve cores if you removed them
during the evacuation steps. You may now introduce
the refrigerant charge through the Schrader valves.
Refrigerant Charging Procedures
R-410A refrigerant must be weighed in when performing
the charge. Referring to
“Estimating Refrigerant Charge,”
, calculate the estimated amount of refrigerant
needed for your system.
When charging a system using a blended refrigerant, it is
essential that the composition of the refrigerant is
maintained. To ensure correct composition, introduce the
refrigerant (R-410A) into the system in liquid form rather
than vapor form. Cylinders which are not provided with
dip tubes should be inverted to allow only liquid
refrigerant to charge the system. Keeping the temperature
of the cylinder below 85°F will help maintain the correct
refrigerant composition while the cylinder is emptied.
WARNING
Confined Space Hazards!
Failure to follow instructions below could result in
death or serious injury. Do not work in confined spaces
where refrigerant or other hazardous, toxic or
flammable gas may be leaking. Refrigerant or other
gases could displace available oxygen to breathe,
causing possible asphyxiation or other serious health
risks. Some gases may be flammable and or explosive.
If a leak in such spaces is detected, evacuate the area
immediately and contact the proper rescue or response
authority.
Initial System Charge
Follow the step by step instructions below to charge
systems using R-410A refrigerant. The initial charge will be
performed by introducing liquid refrigerant to the
discharge side of the compressor or an available liquid line
port with the A/C unit turned Off.
1. Bleed air from hoses and break the vacuum by
supplying liquid refrigerant (R-410A) to the discharge
port near the compressor until the pressure is
equalized. This holding charge allows the low pressure
switch to “hold” enabling the compressor to operate
throughout the process of charging the system.
Fine Tuning The System Charge
Once the initial charge is completed, refrigerant will need
to be added with the unit running.
Note:
An adequate heat load must be supplied to ensure
a proper charge.
2. Disconnect the refrigerant cylinder from the discharge
side of the compressor and connect it to the suction
side.
3. Referring to Section 3.0, start the A/C system and use
the system controller to lower the room temperature
set point 3-5°F below actual room temperature thus
ensuring cooling remains on as the unit is charged.
When fine tuning the charge on cool days it may be
necessary to restrict the airflow across the condenser coil
to raise the pressure. The fan closest to the header must be
running. When fine tuning the charge, ensure the
pressures are correct for the type of refrigerant used. Refer
to the tables in
“Refrigerant Characteristics,” p. 34
operating temperature and pressure ranges for R-410A
refrigerant.
4. Block off a portion of the intake air to the condenser
until a constant discharge pressure can be obtained.
This will lower the possibility of overcharging. Allow
the discharge pressure to rise to 445-480 psig and hold
it constant.
NOTICE
Compressor Damage!
Failure to follow instructions below could result in
compressor failure and/or reduced compressor life. To
prevent compressor liquid slugging, only add liquid in
the suction line when the compressor is running. Use
extreme caution to meter liquid refrigerant into the
suction line slowly. If liquid is added too rapidly,
compressor oil dilution and oil pumpout could occur.
5. Slowly meter liquid refrigerant through the suction
side while watching the pressure gauges and
monitoring superheat and sub-cooling temperatures.
6. Take a superheat temperature reading near the feeler
bulb from the auxiliary control module with the
temperature measuring device being well insulated.
The ideal superheat temperature is 12- 15°F. Maximum
allowable superheat temperature is 20°F.
NOTICE
Compressor Damage!
Do not exceed 20°F superheat. Exceeding this
temperature may cause failure of the compressor.