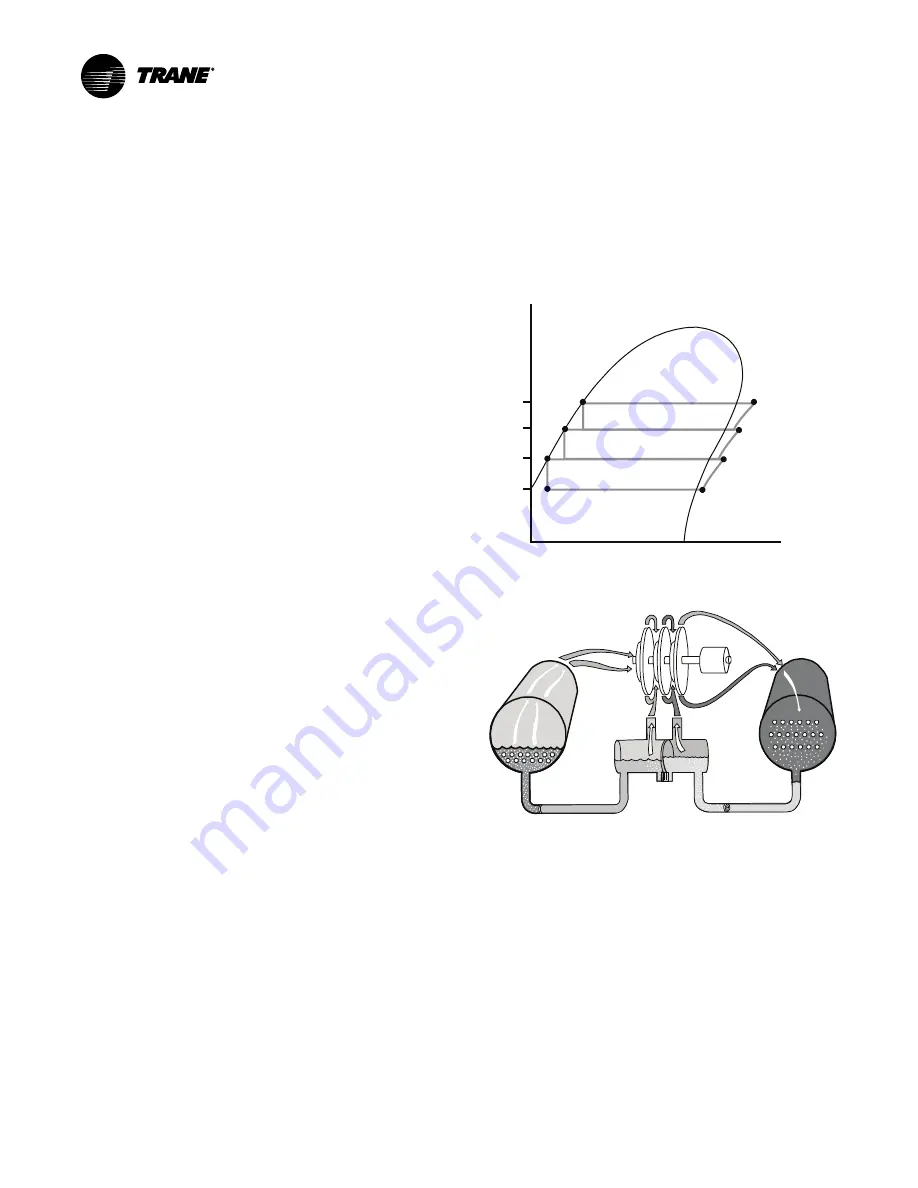
CVHE-SVX005B-EN
71
Operating Principles
General Requirements
Operation and maintenance information are covered in
this section. This includes both 50 and 60 Hz centrifugal
chillers equipped with the Tracer
®
AdaptiView
™
Symbio
™
800 control system. This information
pertains to all chiller types unless differences exist, in
which case the sections are listed by chiller type as
applicable and described separately. By carefully
reviewing this information and following the
instructions given, the owner or operator can
successfully operate and maintain the chiller. If
mechanical problems do occur, however, contact a
Trane service technician to ensure proper diagnosis
and repair of the unit.
IIm
mp
po
orrtta
an
ntt:: Although CenTraVac
™
chillers can operate
through surge, it is NOT recommended to
operate them through repeated surges over
long durations. If repeated surges of long
durations occur, contact your Trane Service
Agency to resolve the issue.
Cooling Cycle
When in the cooling mode, liquid refrigerant is
distributed along the length of the evaporator and
sprayed through small holes in a distributor (i.e.,
running the entire length of the shell) to uniformly coat
each evaporator tube. Here, the liquid refrigerant
absorbs enough heat from the system water circulating
through the evaporator tubes to vaporize. The gaseous
refrigerant is then drawn through the eliminators
(which remove droplets of liquid refrigerant from the
gas) and the first-stage variable inlet guide vanes, and
into the first-stage impeller.
CVHE and CVHG 3-Stage Compressor
Compressed gas from the first-stage impeller flows
through the fixed, second-stage inlet vanes and into
the second-stage impeller. Here, the refrigerant gas is
again compressed, and then discharged through the
third-stage variable guide vanes and into the third-
stage impeller. After the gas is compressed a third
time, it is discharged into the condenser. Baffles within
the condenser shell distribute the compressed
refrigerant gas evenly across the condenser tube
bundle. Cooling tower water circulated through the
condenser tubes absorbs heat from the refrigerant,
causing it to condense. The liquid refrigerant then
passes through an orifice plate and into the
economizer.
The economizer reduces the energy requirements of
the refrigerant cycle by eliminating the need to pass all
gaseous refrigerant through three stages of
compression (refer to the following figure). Notice that
some of the liquid refrigerant flashes to a gas because
of the pressure drop created by the orifice plates, thus
further cooling the liquid refrigerant. This flash gas is
then drawn directly from the first and second stages of
the economizer into the third- and second-stage
impellers of the compressor, respectively. All
remaining liquid refrigerant flows through another
orifice plate to the evaporator.
Figure 45.
Pressure enthalpy curve, 3-stage
Condenser
High Side Economizer
Low Side Economizer
Evaporator
Compressor
Third Stage
Compressor
Second Stage
Compressor
First Stage
6
5
7
4
8
3
1
2
Pressure
Enthalpy
P
4
P
3
P
1
P
2
Figure 46.
Refrigerant flow, 3-stage
CVHF 2-Stage Compressor
Compressed gas from the first-stage impeller is
discharged through the second-stage variable guide
vanes and into the second-stage impeller. Here, the
refrigerant gas is again compressed, and then
discharged into the condenser. Baffles within the
condenser shell distribute the compressed refrigerant
gas evenly across the condenser tube bundle. Cooling
tower water circulated through the condenser tubes
absorbs heat from the refrigerant, causing it to
condense. The liquid refrigerant then flows out of the
bottom of the condenser, passing through an orifice
plate and into the economizer.
The economizer reduces the energy requirements of
the refrigerant cycle by eliminating the need to pass all