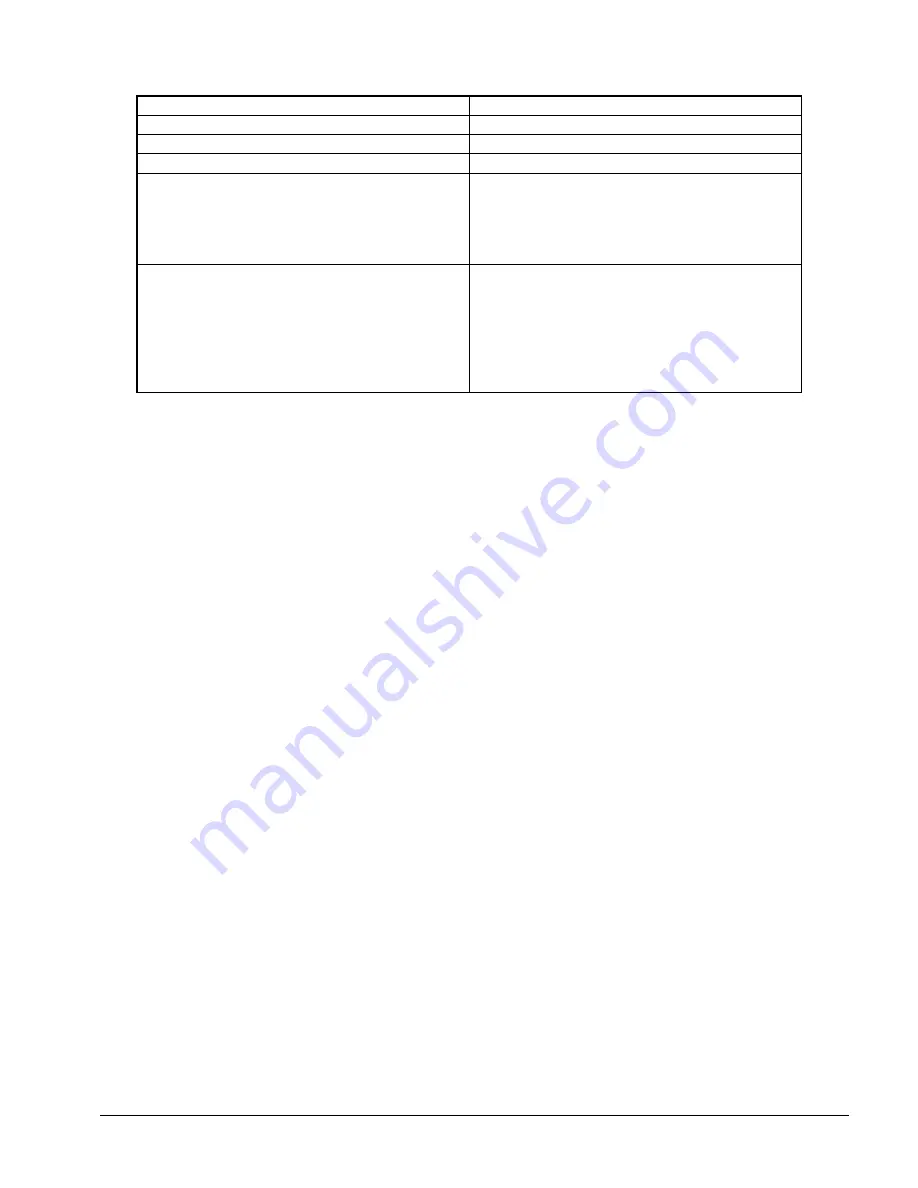
76
TRAK Machine Tools
Southwestern Industries, Inc.
TRAK TRL Lathe, ProtoTRAK RLX CNC Safety, Installation, Maintenance, Service & Parts List
b. Select Mode
b. Press SET UP
c. Select
c. Press SERV CODES
d. Select
d. Press “B”
e. Select Code 127
e. Press X or Z
f. Backlash Value = _ _ _ _
f. What is shown is the current value.
Follow the instruction on the screen and
press the appropriate soft keys.
Wait a few seconds between each
press of INCR VALUE or DECR VALUE.
g. The following is an example of what you
might see when running this code.
For example, if the up and down "Oscillation
Value" shown in the conversation line is .00278
inch, and the dial indicator is moving back and
forth .0012, then the true backlash value is
.00278 -.0012 = .00158 inch. Input this by
pressing MODE, SET UP, SERV CODE, 128, SET
and then .00158, SET, RETURN.
3.
The X backlash identified and stored in Step 2 should be less than 0.003” on a new machine. If
it is appreciably larger, inspect the drive train for loose bolts, brackets, bearings, etc.
The backlash can also be found manually with a 0.0001” indicator using the following method.
Load the indicator to zero from one direction and zero out the DRO.
Move the indicator to 0.002” and then back to zero. Do not over shoot 0, otherwise
start over.
Whatever number appears on the screen is the backlash value.
Enter this value into service code 128.
After entering this number redo the process. The DRO and indicator should now both
read 0.
CODE 128: Input Backlash Constant
Code 128 allows you to enter the backlash values for each axis. It displays the value after it
enters.
Be sure not to enter too much backlash on any given axis. Too much backlash in the system
may cause bi-directional repeatability problems or axis motor searching.
5.2.3 Lubrication
5.2.3.1
Headstock Lubrication
1630, 1845, 2470:
The pump needs to be primed if left unused for a couple days.
Priming the pump entails turning the spindle on at 1000 RPM for a few seconds.
An oil pump provides lubrication for an even distribution of oil to all the gears and bearings in the
headstock. One of the oil lines pumps oil to a site glass located on the headstock. Periodically
check to see that oil is flowing. Oil flows to this site glass only when the spindle is running for the
1630, 1845 and 2470. The 1630HS does not require headstock oil.
The plug to drain the headstock is located under the spindle cover towards the bottom of the casting. See
the figure below. Oil can be added to the reservoir by a plug in the top of the headstock cover or by
removing the cover and pouring it into the headstock. There is a level site glass located under the spindle
cover. The headstock reservoir holds different amounts depending on the machine. See Section 2.2. Fill
the headstock with Mobil DTE 24 oil or an equivalent grade.
The headstock gearbox oil must be drained and flushed after the first 150 hours of operation. A small
percentage of kerosene may be added to the gearbox to flush out dirt and sediment. Operate the machine