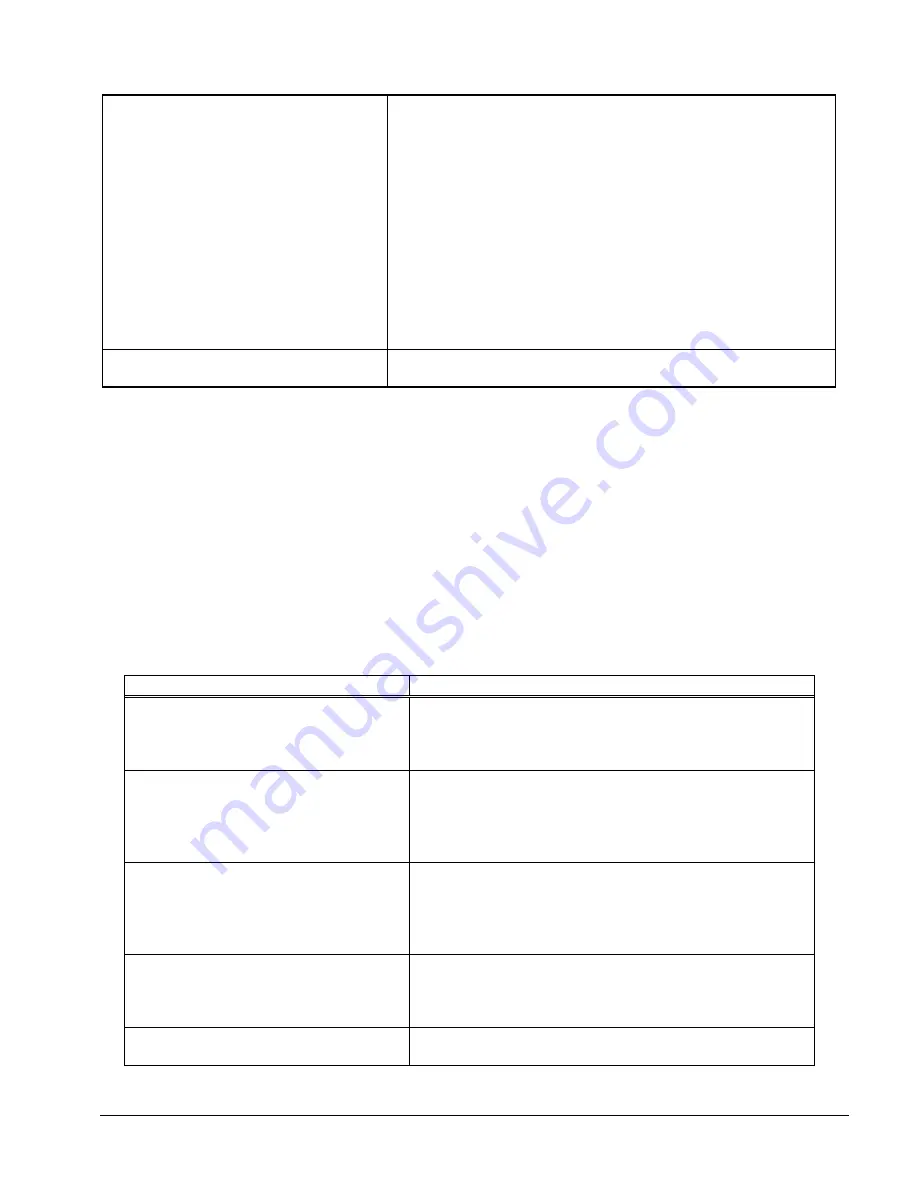
39
TRAK Machine Tools
Southwestern Industries, Inc.
TRAK TRL Lathe, ProtoTRAK RLX CNC Safety, Installation, Maintenance, Service & Parts List
Limit Switch failure
Try this
Switch 2 limit switch cables on the
auxiliary module in the electrics box.
Turn off all power to the machine. For the positive direction,
check for continuity between pins 1 and 6 on the Limit Switch
cable connector. You should hear a continuous beep from your
Multi-meter. By hand, manually depress the plunger on the limit
switch responsible for when the table, saddle, or ram is moving
in the positive direction. The beep from your Multi-meter should
stop beeping. This means the Limit Switch is triggering properly
for the positive direction. For the negative direction, repeat the
same procedure as described above using pins 5 and 9 on the
Limit Switch cable connector.
Does the limit switch problem move to the other axis? If it does
then the switch is most likely the problem. If it stays with the
original axis then it could be the auxiliary module or computer
module. See below.
Limit switch jumpers in cable breakout
box are making poor contact
Remove and reseat jumpers
3.2 Problems Relating to Machining Results
3.2.1 Poor Finish
Poor finish can be caused by a number of variables including: speeds, feeds, tooling, machine setup
and chatter.
Perform the following Service Codes:
Code 33
Software Identification. This is needed if you call SWI Customer Service.
Code 131
Manual DRO.
Used to move the axes to verify the encoders are counting.
Code 127
Measures backlash in the system.
Code 128
Enter backlash compensation.
Possible Cause
Check This
Inadequate or no Lubrication to
Ballscrews and Way surfaces
Make sure all the Way surfaces are getting proper
lubrication. If not, check to make sure that the lube pump
is functioning properly. Also check for any pinched or
blocked oil lines.
X & Z-axis Drive Trains are loose
Check Repeatability using the Repeatability and Positional
Accuracy procedure. Step by step, carefully inspect the
Drive Train for any looseness. It may be necessary to
disassemble and then reassemble the Drive Train. See
Mechanical Drive Train (X, Z) Section 4.2
Way surfaces are pocked, scarred, or
excessively worn
Visually check the condition of all the Way surfaces. For
machines that may have excessively worn Way surfaces
you may need to adjust the Gibs in this area. This will
affect performance when using the machine outside of
this area. Check lubrication to affected areas.
Machine set-up problem
Machine’s feet are not equally supporting weight. See
Leveling
,
Section 2.9.
Verify the tool holder is correctly centered to the dead
center of the spindle as well as the tail stock.
Tooling problem
Improper tooling, Work piece not properly supported
speeds too fast, Feeds too slow.