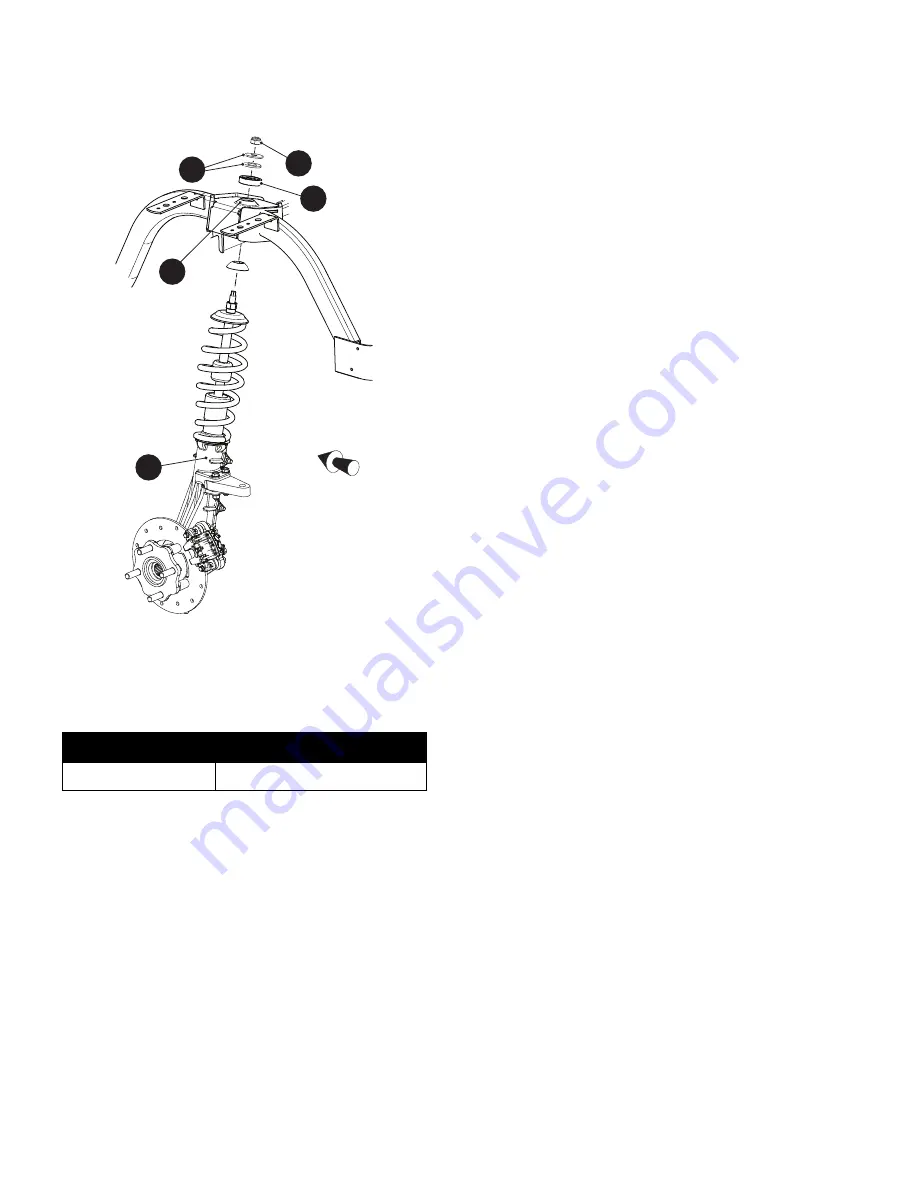
B
88
Repair and Service Manual
REAR AXLE AND SUSPENSION
Read all of SAFETY and this section before attempting any procedure. Pay particular attention to Notices, Cautions, Warnings and Dangers.
10002660
Fig. 5 Strut Assembly
Assemble in the reverse order of removal using new lock
nuts.
Tighten the lock nut to the torque values specified below.
Strut Assembly Maintenance Items
The following maintenance procedures are identical to
the front strut assembly procedures (See FRONT SUS-
PENSION on page 53):
•
Lower Ball Joint Replacement
•
Wheel Bearing Replacement
Strut Replacement
Item
Torque Specification
27
14 - 16 ft. lbs. (19 - 47 Nm)
Front of Vehicle
27
29
28
13
24