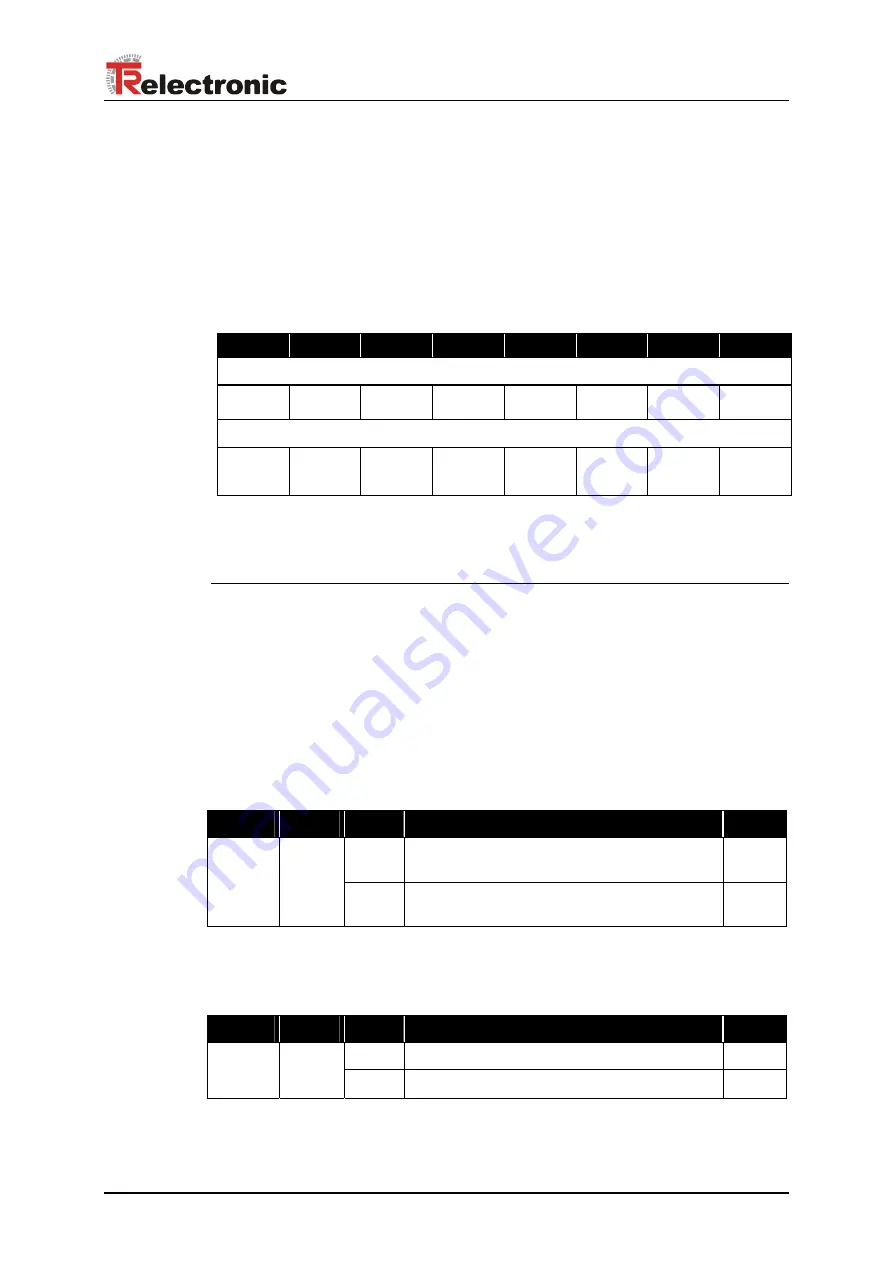
Parameterization and configuration
Printed in the Federal Republic of Germany
©
TR-Electronic GmbH 1998, All Rights Reserved
03/09/2010
TR - ECE - BA - GB - 0014 - 03
Page 23 of 31
7.2.2 GET DATA CHECK - command
Instance 17, r/w
If the parameters are programmed via the "Parameter-Class", for taking over and test
the data, a Data-Check must be performed subsequently. The result (2 bytes) of the
SET DATA-CHECK can be read with GET DATA-CHECK. Are all bits of the returned
UINT value "0", no error is available. The possible errors are indicated in following
table:
GET DATA-CHECK:
Bit7
Bit 6
Bit 5
Bit 4
Bit 3
Bit 2
Bit 1
Bit 0
Low Byte Error Receive Buffer Master
0 0 0 0 0 0
Write-
error
Read-
error
High Byte Error Receive Buffer Master
0
Steps/Rev.
exceeded
3)
TNOS/Rev.
=0
upper
1)
SL
out of
range
upper
2)
OL
out of
range
lower
2)
OL
out of
range
lower
1)
SL
out of
range
0
An error bit can only then be reset when the data is corrected and a DATA-CHECK
command is executed.
1)
SL
= Safety Limit
2)
OL
= Operating Limit
3)
TNOS
= Total Number of Steps
7.3 Parameters / Range of values
7.3.1 Direction
Instance Service Value Description
Default
= 0
Position increasing clockwise
(view onto the shaft)
X
1 r/w
≠
0
Position decreasing clockwise
(view onto the shaft)
7.3.2 Output Code
Instance Service Value Description
Default
= 0
Binary code
X
2 r/w
≠
0
Gray code