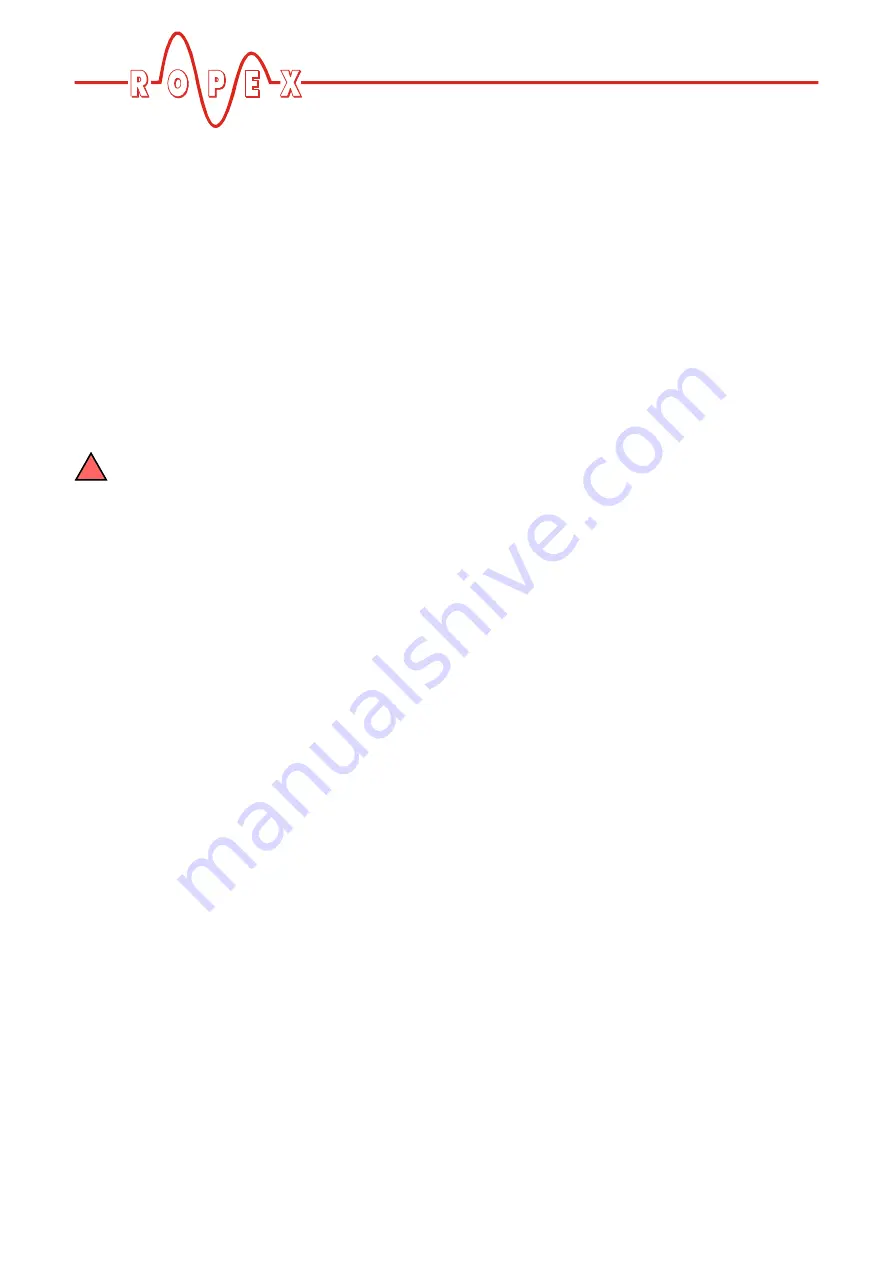
Controller functions
Page 44
RES-409
10.14
Undervoltage detection
(as of February 2007)
Trouble-free operation of the temperature controller is
guaranteed within the line voltage tolerance range
specified in section 6 "Technical data" on page 8.
If the line voltage drops below the lower limit of the
permissible range, the controller is switched to standby
mode.
This is also indicated in the controller status, bit no. 14
(
section 10.4.1 "Controller status" on page 36).
Normal operation is automatically resumed when the
input voltage returns to the specified tolerance range.
Standby mode is indicated by 0…3°C (corresponds to
approx. 0V) at the analog output.
Trouble-free operation of the controller is
only guaranteed within the specified input
voltage tolerance range. An external voltage
monitor must be connected to prevent defective
heatseals as a result of low line voltage.
10.15
System monitoring / fault output
To increase operating reliability and prevent faulty
heatsealing, the controller incorporates special
hardware and software features that facilitate selective
fault messages and diagnosis. Both the external wiring
and the internal system are monitored.
These features crucially support the system owner in
localizing the cause of an abnormal operating state.
System faults are reported or differentiated by means
of the following elements.
A.)
Red "FAULT" LED on the controller lights up
with three
states:
1.
Blinks fast (4Hz)
The "AUTOCAL" function must be run (error codes
8+9; as of February 2007 also: 104…106, 211, 302,
303).
2.
Blinks slowly (1Hz)
The system configuration is incorrect and the zero
calibration (AUTOCAL function) was therefore
unsuccessful (
configuration" on page 18). This corresponds to
error codes 10…12 (as of February 2007 also:
111…114).
1.
Lit continuously:
This indicates a fault that prevents the controller
from being started up (error codes 1…7; as of
February 2007 also: 101…103, 107, 108,
201…203, 307, 308, 801, 9xx).
Also in instances 1 and 2 if a "START" command is
simultaneously sent.
As a rule, this refers to an external wiring fault.
B.)
Fault relay (relay contact terminals
12+13+14):
The fault relay is set in the factory as follows:
•
NOT ACTIVE
in operating states A.1 and A.2, but
active if a "START" signal is activated in one of
these states.
•
ACTIVE
in operating state A.3.
If the fault relay is configured differently from the factory
setting (
section 9.2.3 "Configuration of the fault
relay" on page 19), these states are inverted.
C.)
Error code output by means of the CAN
protocol
If an error occurs, the fault bit is set in the controller
status (bit 4) (
section 10.4.1 "Controller status" on
page 36) and in the acknowledgment message (bit 14)
(
section 10.4.2 "Acknowledgment message" on
page 37). The error message appears at bit positions
8…11 in the controller status.
D.)
Error code output by means of the 0 to 10V
actual value output (terminals 17+18):
Since the temperature no longer needs to be indicated
if the controller is faulty, the actual value output is used
to display error codes in the event of a fault.
13 voltage levels (up to January 2007: 12 voltage
levels) are provided for this purpose in the 0…10VDC
range, each of which is assigned an error code
(
section 10.16 "Error messages" on page 45).
If a state that requires "AUTOCAL" occurs – or if the
controller configuration is incorrect – (error codes
8…12; as of February 2007 also: 104…106, 111…114,
211, 302, 303), the actual value output jumps back and
forth at 1Hz between the voltage value corresponding
to this error and the end of the scale (10VDC, i.e.
300°C or 500°C). If a "START" command is sent in one
of these states (or a "START" signal is activated), the
voltage value no longer changes.
Selective fault detection and indication can thus be
implemented simply and inexpensively using the
analog input of a PLC with a suitable evaluation
function (
section 10.16 "Error messages" on
!