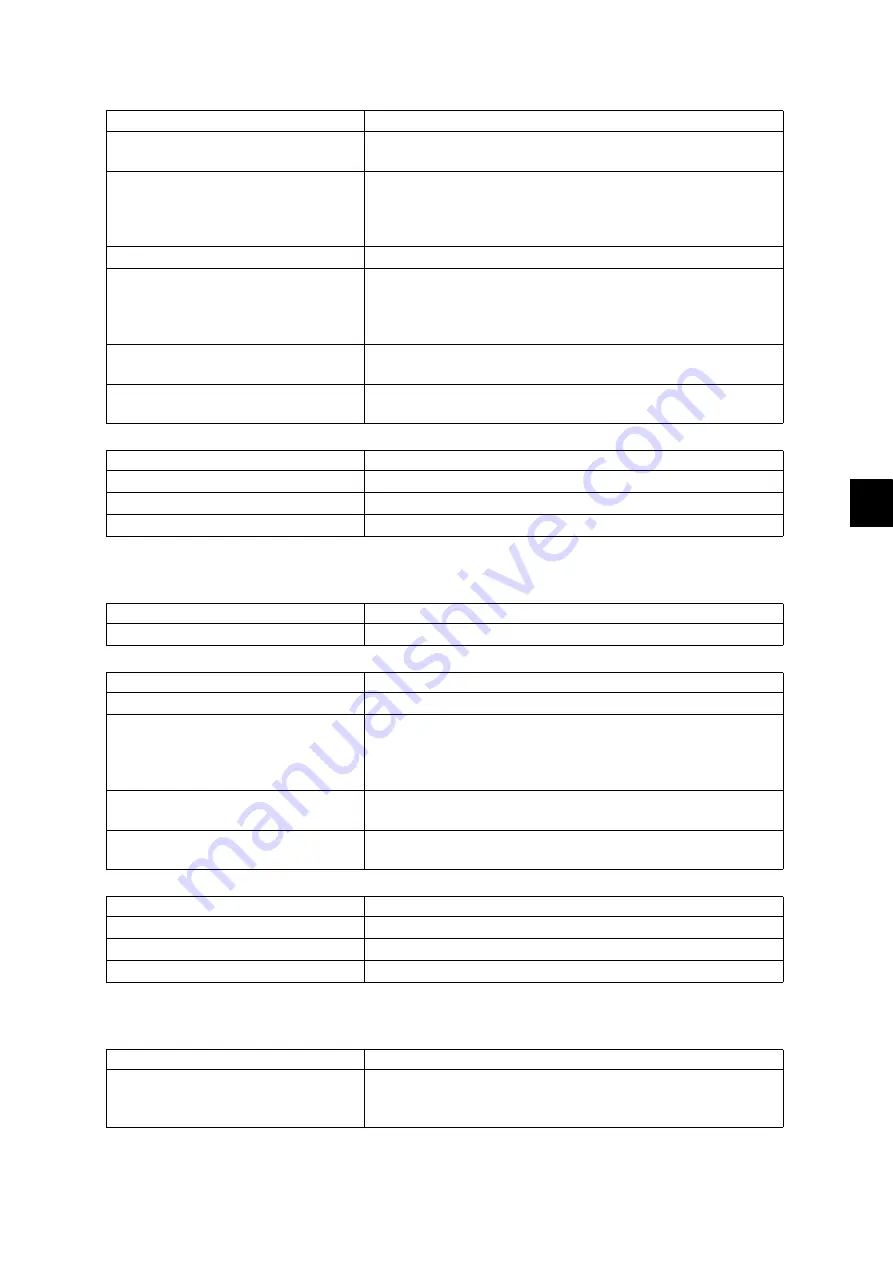
8
© 2011 - 2015 TOSHIBA TEC CORPORATION All rights reserved
e-STUDIO5540C/6540C/6550C/5560C/6560C/6570C
ERROR CODE and TROUBLESHOOTING
8 - 81
[E729] Stop jam at the original reading end sensor
[E731] Stop jam at the original exit sensor
Check item
Measures
RADF
• Check the RADF position adjustment.
P. 6-112"6.12.1 RADF position adjustment"
RADF
• Check the Adjustment of the Reversing Automatic
Document Feeder (RADF).
P. 6-112"6.12 Reversing Automatic Document Feeder
Read end roller
• Cleaning
Original reading end sensor
• Sensor check
(Perform the input check: 03-[FAX]ON/[5]/[D])
• Connector check
• Harness check
RADF board
• Connector check (CN75)
• Board check
Drive unit, Rollers
• Gear check
• Roller check
Replace parts
Remarks
Original reading end sensor
RADF board
Perform the 05-3210
Roller
Read end roller
Classification
Error item
RADF jam
Check item
Measures
Read end roller
• Cleaning
Original reading end sensor
• Sensor check
(Perform the input check: 03-[FAX]ON/[5]/[D])
• Connector check
• Harness check
RADF board
• Connector check (CN75)
• Board check
Drive unit, Rollers
• Gear check
• Roller check
Replace parts
Remarks
Original reading end sensor
RADF board
Perform the 05-3210
Roller
Read end roller
Classification
Error item
RADF jam
The trailing edge of the original does not pass the original
exit/reverse sensor after its leading edge has reached this
sensor.