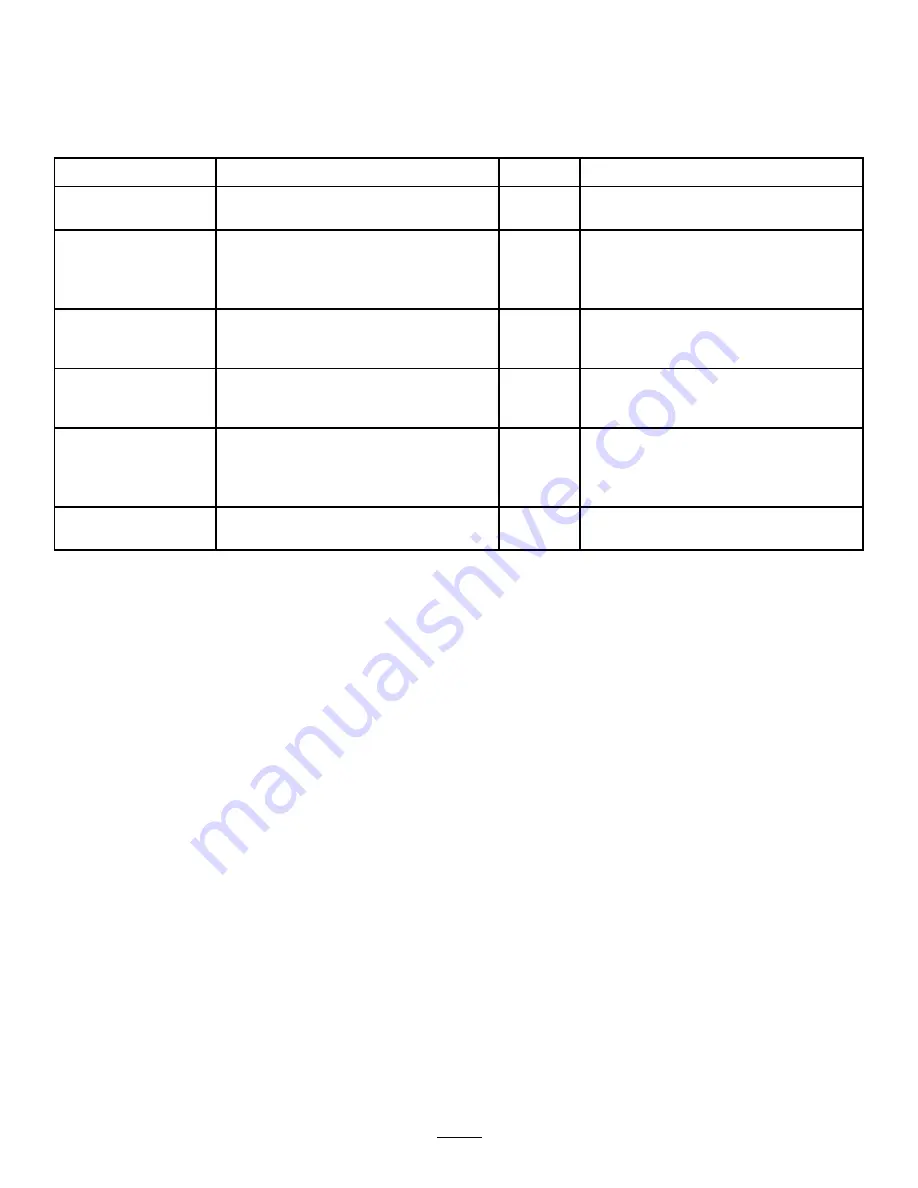
Setup
Loose Parts
Use the chart below to verify that all parts have been shipped.
Procedure
Description
Qty.
Use
1
No parts required
–
Remove the blower from the crate.
Drive shaft assembly
1
Roll pin
1
Bolt, 5/16 x 1-3/4 inch
2
2
Locknut, 5/16 inch
2
Install the drive shaft to the blower gear
box shaft.
Mounting plate
1
Bolt, 1/2 x 1-1/4 inches
4
3
Locknut, 1/2 inch
4
Install the mounting plate to the debris
blower frame.
Debris blower assembly
1
Locking pin
1
4
Hairpin cotter
1
Mount the blower to the traction unit.
Proximity switch assembly
1
Sensor plate
1
Carriage bolt, 5/16 x 1-1/4 inch
2
5
Flange nut, 5/16 inch
2
Install the proximity switch
6
General Purpose Lithium Base Grease
A/R
Grease the machine
Note:
Determine the left and right sides of the
machine from the normal operating position.
Note:
To install and operate the debris blower, the
traction unit must be a 4 Wheel Drive machine which
is equipped with the Front Quick Attach Front Frame,
Model 30509 and one of the following; the Electric
Accessory Kit, part no. 115–0019 or the Joystick Kit,
model 31219.
5